Analysing the Root Cause of Failures
Indicators like contaminated oil or broken actuator shafts can hide the root cause of failure. Failure analysis carried out correctly uncovers what is not working along with a strategy for improving a system’s design and reliability.
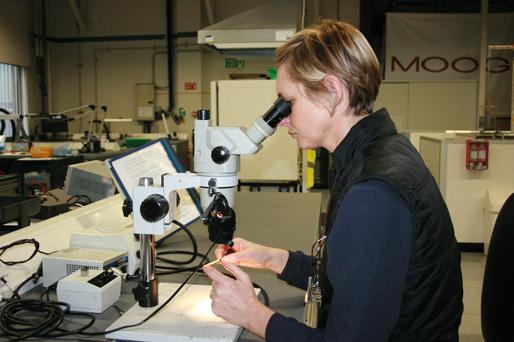
Failure analysis is the process of gathering and examining data to pinpoint why something fails. The best engineering teams go beyond repairing components; they recommend system improvements and maintenance programs aimed at decreasing downtime, minimizing repair costs and increasing productivity.
Sometimes, independent (or third-party) test labs will conduct a simple analysis such as oil testing. But the manufacturers of products like servo motors, hydraulic actuators and servo valves take analysis far beyond what a third-party lab can do. Here’s why: The original equipment maker not only designs and repairs the technology but in many cases offers access to design and product engineers able to undertake proper failure analysis and offer suggestions for enhancing the overall system.
Following is a scenario in which failure analysis plays a key role. Assume an electric actuator designed for directional drilling in an offshore, downhole oil and gas rig breaks down or fails in the well. The actuator will typically be used at drilling depths of more than 6,100 m (20,000 ft); it is designed to withstand temperatures up to 200 °C (572 °F), pressures up to 35,000 psi (2,450 bar), and high shock. Failures of this nature can cost drilling companies up to US$1 million per day. The drilling company technician has several options to service the failed actuator. An important option for the technician to consider is a failure analysis by the actuator’s manufacturer. That is because the equipment maker can determine the root cause of the system failure, plus offer solutions to prevent future downtime.
Design and quality engineers from Moog investigate the root cause of a variety of failures involving motion control products including structural failures, contamination issues, chemical compatibility, material analysis and electrical failures. As a designer and manufacturer of motion controls for a wide range of industrial applications, Moog understands the importance of reliability to critical operations.
Failure analysis incorporates the component designer’s know-how, which often includes the experience of a large installed base of systems in the field. For example, manufacturer’s engineers have seen its components in the context of a system from the drawing board through prototype, production and after sales service. The engineers also develop the specifications for the product with the customer, and they know why the materials were chosen and what part they play in the performance of the overall motion control system. Failure analysis ensures a customer conducting critical operations receives value beyond the simple repair of a product.
When, for instance, a servo motor stops working, the cause is not always the component itself; it may be related to the system. Engineers who take a truly collaborative approach with their customers will make the extra effort to use metallurgical lab results to help analyze the failure.
The actuator example mentioned in this article was part of a design for a downhole motor for offshore drilling, which Moog worked on approximately twenty years ago. The customer and manufacturer worked out the required performance specification and selected materials suitable for high temperature and high-pressure conditions. During the development of the initial drilling units, manufacturer analyzed failures and made improvements on the design.
For instance, when the drilling company experienced problems with the motors for its directional drilling tool, upon initial inspection it looked like the culprit was an external side load. But as the manufacturer analysed the problem, it discovered that the failure stemmed from the way several components were assembled. Until a product begins operating in real-world conditions, it can be difficult for even a customer to know how it will behave in a system. Feedback from users in the field on how they use the product is critical to both manufacturer and users.
Repairs as a Team Effort
When a customer turns to its equipment maker (instead of a local repair house) to carry out repairs, the manufacturer can become an extension of the customer’s engineering team. For example, a manufacturer can work with a customer’s engineers and project managers to define the requirements at the beginning of the project. Over the life of the equipment, the manufacturer will use capabilities such as failure analysis to ensure the product operates as new over a long service life.
While the example cited in this article was an electric product, the engineers have extensive experience analyzing the symptoms of failure at the hydraulic system level too. For example, when it comes to analyzing oil samples, a customer can use a variety of local labs for a determination of contamination. But being told that your system’s oil is bad does not tell you what is wrong.
The manufacturer can analyse the data, assess the condition of the failed product and most importantly recommend changes to the system’s design. For instance, manufacturer’s engineers might determine certain components are superfluous to the design, or specific parts are putting undue stress on the system. A company that looks at failure analysis holistically can even recommend the replacement or elimination of components to streamline a design.
Experience Improves Failure Analysis
When it comes to failure analysis, customers can benefit from having the original equipment manufacturer work on the problems. Not all component makers can (or want to) analyze your equipment failures beyond the repair stage. But some companies truly are solution providers; these companies have the know-how, resources and desire to improve how your technology is operating, not just make a repair.
The costs of non-productive time and unexpected product failure have never been higher. Among the best investments a company can make is uncovering what is causing the failure and eliminating the issue for the long term, through better design. Failure analysis is your key to reliability over the life of the equipment.
R. Scott Scheffler, market manager for Oil and Gas Solutions at Moog, has over 15 years of experience in engineering, systems integration and sales in the motion control industry including providing electric and hydraulic motion control solutions for applications in the O&G industry for downhole tools and drill rig equipment. He has a B.S. degree in electrical engineering and a master’s in business administration.