Taking Control of Plant Data with PlantSight Digital Twins
In the old days, project handover from contractors to owner/operator involved a big tractor-trailer and forklifts that moved crates of documents from the design and construction contractors to the plant’s records room. Most of that paper was never looked at again because it was hard to find a specific piece of information, and what one did find was likely outdated. Fast-forward to 2010, and the truck was smaller, as more of the data was in digital form — but it was still hard to navigate through the different formats and data creation tools to find the specific bit one needed.
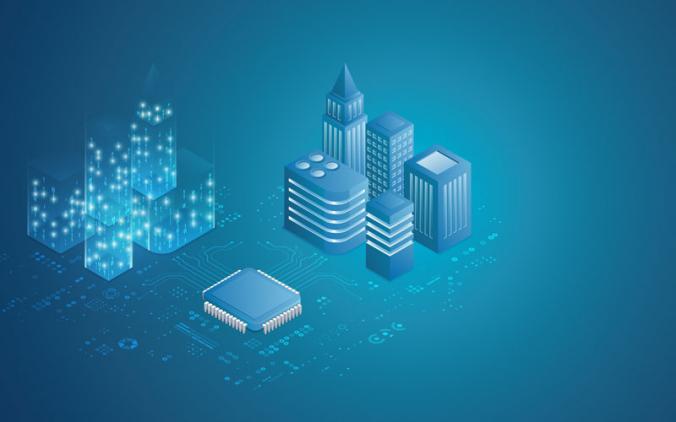
n 2020, we’re seeing the emergence of new tools like Bentley’s PlantSight, which aim to use cutting-edge technologies to capture, control, and serve out the many types of data that represent today’s operating asset. From process flow diagrams to 3D models of a plant, from as-designed to as-built, and from desktop to cloud technologies, PlantSight helps authorized engineers and plant operators quickly find the one piece of information they need to keep their plant or project running.
First, what is PlantSight?
PlantSight aligns 1D, 2D, and 3D data into a single, visual representation of an asset. In the screen capture below, a virtual gate valve is aligned over the reality captured as-is model. Tag numbers are the link between the different data types and ensure continuity across them all. This view is served to users via a web browser, making it easy to access from the office or a networked tablet in the plant itself.
Once PlantSight’s digital twin of the physical plant is created, it has many potential uses. Cloud access means the verified data is available to all authorized engineers and operators, regardless of their physical location. That means improved collaboration, on-site and with experts offsite, to assess and strategize to resolve issues. The unlimited computing power of the cloud, combined with analytics and artificial intelligence, can be brought to bear on predictive maintenance or analyzing economic alternatives for efficient operations.
If desired, the digital twin can be updated with live data from sensors on the plant floor via the Industrial Internet of Things (IIoT). Modeling technologies such as CAD and reality meshes can be combined to create augmented and virtual reality models to train workers, simulate responses, and develop scenarios for refits or rebuilds.
It does all start with a digital twin. It sounds simple: a digital twin is a digital representation of a physical asset. But it quickly gets complicated, since the digital version must include the processes and systems that create and operate the physical version if it is to duplicate it. In a plant, the first version of a digital twin is often the CAD model of the plant. But operators quickly realize that they need experts in using the CAD system that created the model to keep it current — limiting its usefulness and ultimately leading to it being so outdated that it is abandoned. And they also realize that the CAD model isn’t enough: it needs to be able to direct an engineer to operational data about specific pieces of critical equipment, to maintenance manuals, and perhaps to operating data to signal that failure may be imminent. In a perfect world, the model would also suggest corrective action.
To be truly useful, the digital twin starts with 1D, 2D, and 3D data, then adds maintenance manuals and other critical documents, and overlays this with data from sensors and physical observation to keep it current. Adding this together, federating it, creates a one-stop portal into the asset, allowing engineers to visualize components, check status, perform analysis, and generate the types of insights that ultimately reduce risk and optimize performance. Operators see the real benefit of a digital twin when they look over the asset’s lifetime, using consistent data from design to operations, enabling trade-off decisions to be made that are based on fact rather than gut feel. This is what PlantSight is made for.
Building the PlantSight Engine
Bentley Systems and Siemens Digital Factory have been creating plant design and operation solutions for decades and saw the massive potential for improvement all along the chain from conceptual design to 3D modeling to operations and maintenance. Together, Bentley and Siemens created a vision for an open, cloudbased solution that federates data sources and provides specific role-based workflows via cloud-based services to build and use the PlantSight digital twin of the asset throughout its life cycle.
The partners architected PlantSight to be extremely flexible, using Bentley’s iTwin technology as the building block schema for adding data, manipulating it and managing change, and serving it out to engineers:
- Bentley’s iTwins are data repositories (called iModels) that could be drawings, specs, documents, CAD or analytical models, reality meshes, IIoT feeds, enterprise data and asset management data — in effect, any data that can be described
- iTwin Services are cloud services that enable users to create, visualize, and analyze iTwins. Bentley is rapidly adding more services, but one existing iTwin Service is visualizing and tracking change, including changes in real-world conditions from sensors and drones.
- The 2D/3D visualization iTwin Service is central to PlantSight since it is the visual front-end that ties together data created in multiple, often incompatible tools. This iTwin Service federates (or combines) repositories of different types and transforms the data into a standardized, open format that is suitable for visualization and analysis. The resulting information can be visualized in 2D or 3D using a web browser, manipulated and operated on. This iTwin Service uses ProjectWise Bridge Service, which supports intelligent design systems such as SmartPlant 3D, PDMS, and E3D and OpenPlant and also RVT, .DWG, .DGN and .IFC file types.
- iModelHub is an iTwin Service that keeps a timeline of changes to each iTwin. Think of it as a record of who, what, and when for each iTwin. As an example: a complex project has many designers; who changed what system, on what date? Designers can roll backward and forward in the timeline, name significant versions, find differences between points on the timeline, and create reports.
PlantSight also follows best practices for cloud solutions, as do all of Bentley’s and Siemens’s well-established products: state-of-the-art cyber-security and access control, change management, and data traceability.
PlantSight embodies its creators’ belief that an open architecture is critical because all plant projects and operations today rely on dozens of IT solutions from increasingly deep supply chains. Every complex plant project relies on many IT providers’ solution sets. PlantSight’s open architecture means that engineers can build a digital twin from drawings created using one vendor’s tools, 3D models from another, and reality models from a third, and links to data from any number of enterprise and operations systems.
And, as you can see, the user interface is clean, visual, and easy to navigate, for both expert and novice users.
In the long-term, PlantSight future-proofs the installation, making it flexible to whatever IT emerges over time. PlantSight is a digital platform that is open to whatever engineering applications, repositories and files systems, and file formats and schemas designers and operators might need, today and in the future.
Bentley and Siemens realize that they cannot be the source of all connectors, supplying bridges for both commercially available and in-house tools. They have created an open, connected data environment (CDE) with iTwin Services, including iModel.js. iModel.js is an open-source library that enables anyone (who has the knowhow) to connect their data to a digital twin. Bentley believes that making the library open source will foster innovation and lead to many more novel uses of digital twins, far more than Bentley alone has the bandwidth to pursue.
The early adopters we spoke with are already using Bentley’s iModel and iTwin Services to connect their data to engineers and operators. For them, PlantSight creates a visual front-end that they intend to use across projects, to contextualize many different data silos, and to make it all easily accessible.
Why Bentley + Siemens?
Bentley Systems and Siemens AG have brought together their technology stacks, domain expertise, and unique capabilities to create PlantSight. Siemens brings its experience as a software powerhouse to PlantSight, providing IoT connectivity and analytics via its MindSphere and XHQ platforms, all supported by the COMOS 1D/2D process design, engineering, and plant automation platform. Bentley adds its deep bench of 3D plant modeling and reality capture technologies, the AssetWise asset performance and reliability platform, and the iTwin Services and iModel.js open-source platform to form the PlantSight technology stack.
The companies will be bringing other joint products to market — in each case, the idea is to create a solution to specific industry issues. With PlantSight, Bentley and Siemens want to address the 50 to 100- year lifespan of many operating plants, and the reality that few have consistent, reliable, and easily-accessible data about the asset. Once that data exists in the form of a PlantSight digital twin, they want operators to start using it to improve performance and reliability, for a higher return on their investment. How? By using PlantSight to digitally simulate physical, production, or reliability-based engineering changes before implementing anything in the operating asset.
Both companies have repeatedly said that PlantSight and their other joint offerings will be agnostic. This means that data will not be locked into a Bentley or Siemens ecosystem and that engineers will be able to use the CAD, asset management, IIoT, or other tool of their choice.
Building a PlantSight Digital Twin
Most engineers usually start building their PlantSight digital twin with the central driver for most refineries and chemical process plants: the process and instrumentation diagram (or P&ID). Even in older assets, the P&ID is usually up-to-date and so makes a good starting point for a digital twin. Next, they layer on more data, more data types, and work processes. PlantSight doesn’t require a 3D model — 2D schematics are sufficient for many uses. But that’s not really the best use of PlantSight.
PlantSight is a visual front end to the digital twin, so a 3D model increases the utility of the twin for nonexperts. 3D models can help engineers quickly locate physical objects in a crowded space, perhaps overlaying operating parameters or maintenance instructions using augmented reality tools.
If a CAD model is available, PlantSight can read in all major formats using iModel bridges, or create a 3D representation from laser scans or photogrammetry to update older CAD data or create a 3D model from scratch. Using a combination of techniques, PlantSight can be used to create the twin of a single piece of equipment or a complex, fully operating plant, that’s brand new or decades old.
What kind of data might you incorporate into PlantSight? You might use engineering models, reality meshes, and schematics from OpenPlant, Siemens COMOS, SmartPlant 3D or AVEVA E3D, or most other toolsets. You could use asset models from AssetWise, XHQ, SAP, IBM, or any data historian, computerized maintenance management system (CMMS) or enterprise asset management systems (EAM). As you can see from the example below, it could be an overview photo of the site, with system data laid on top. But the point here isn’t a list of what you could use; it’s that the iTwin microservices allow you to create a container for almost any data type.
Once PlantSight has acquired the 1D/2D/3D data, it aggregates this data and links it to IIoT, or other data, using the item’s tag as the linking mechanism. Then, it’s time to visualize it and publish it out to engineers. The digital twin is only updated when assets are updated to reflect the current reality in the field. Each engineer can now walk through the model, analyze data, link to ERP or other external sources, and make informed decisions to today’s particular problem.
PlantSight is a specific iTwin Service for the process industries. Bentley’s generic iTwin services can be used for any type of infrastructure project – roads, bridges, railways, buildings, and even cities. Early adopters are trying iTwin Services on all sorts of other projects. One EPC is using it to monitor construction on a large project, using drone flights to capture as-is construction status. In this case, the digital twin is a reality model that is combined with other data to track construction and visualize change over time using iTwin services. This process also creates a digital record that will enable future workers to know exactly where underground utilities are buried, for example, or to see the sequence of installation of crucial equipment. This process feeds into later operations of the plant, jump-starting creation of the digital twin of the asset.
Once the bones of the digital twin are in place, it’s time to consider how it will be managed. Remember that the point of the twin is to help operate the physical asset, so updating as things change is critical. The team building PlantSight needs to consider what data to access, connect, analyze, and visualize. PlantSight doesn’t replace asset management or maintenance management systems, so having access to real-time data is likely not necessary. Incorporating near real-time data such as analytical results of process parameters or inspection reports could be useful.
Using a PlantSight twin
How engineers and plant operators will interact with PlantSight, what types of issues they are likely to face, and how they should respond are vital in designing any specific PlantSight instantiation — and each will be different.
Consider engineers working with an aging asset, where the goal is to maintain acceptable levels of production with as little plant change as possible. In this case, a minimal model may be sufficient, as long as it allows operators to do shutdown planning, and track maintenance issues like leaks and corrosion.
On the other hand, if you’re looking at a plant that’s about to undergo a significant upgrade, you’ll need to add data required for collaboration between the engineering and design teams, such as specs. You’ll also need to facilitate planning and visualization by internal and external stakeholders, so you may need GIS data or a plot plan.
Or perhaps the plant is ticking along nicely, but in need of constant monitoring because of varying prices of inputs. You might want to focus your PlantSight digital twin on risk-based inspections and reliability strategies. Look for the data you need to inform your asset performance management and predictive engineering tools.
Whatever today’s starting point, the PlantSight digital twin will likely be built for one purpose —say troubleshooting yield issues— but will evolve to address many more topics. PlantSight is flexible and agile, so you can always add or change but do need to pick a point from which to start. Consider which workflows matter most to you, today:
- Troubleshoot problems in the plant
- Reduce engineering design time
- Involve more experts in and speed up design and other review processes
- Simplify the creation of work requests
- Improve operator training
- Speed up root cause analysis
- Share issues with suppliers and contractors
- Lower the HSE incident rate through better planning and preparation
Then gather the specific inputs needed to address that one issue. Going too big, too soon, is overwhelming. Start small, prove success, and grow from there.
Getting Started
Perhaps the most essential aspect of embarking on digital twins isn’t technological at all but goes to the heart of a company’s strategy. How digital do you want to be? How do you want to relate to your contractors, clients, and employees? Major engineering firms are already on a digitalization journey, looking for new ways to apply technology to make their projects more successful, reduce risk, and ensure timelines are met. They’re also looking for new business opportunities and see PlantSight as a way to stay relevant to their clients after handover, by creating a PlantSight twin for operations and, depending on the scenario, maintaining it on behalf of the plant’s operator. Owners see digital twins as a way of more effectively operating their assets, reducing risk, managing across a portfolio of old and new, underperforming and exceptional, assets to apply the best lessons across all.
So, it’s likely that the first and most crucial step to creating a digital twin is to create a corporate culture that values data, its creation, and its maintenance, above pushing paper. Capture, sanitize, and control data in case you have a downstream use for it. Start building the confidence that the data you have is accurate and accessible. Only then can you start encouraging people to rely on it for daily operations, perhaps with PlantSight as the front end.
Once the operations team is using PlantSight, start looking for more uses. What types of analytics are you currently doing, and what can you do in the future — and what data do you need to do that? The first PlantSight twin you build will likely evolve as you discover use cases — be sure to leave that door open.
Where’s the Proof?
The PlantSight use that’s gaining the most interest is for remote operations. PlantSight enables multiple users to have access to the same data at the same time — all they need is a browser, connectivity to the cloud, and the correct access credentials. Everyone can review the digital twin without having to go on-site. They see, zoom, mark-up, and otherwise interact with the digital twin to jointly make decisions. This up-to-date, always-on access is critical in a world where a plant is often far from decision-makers; it connects the plant to the office in a new, actionable way.
PlantSight can also be used to simulate potential alternative solutions to a problem: will a new piece of equipment fit into a designated footprint? Can we maneuver it into position without removing anything else? If connected to a CMMS, engineers can try out alternative maintenance scenarios. Simulating tasks reduces risk, saves money and time, and protects human life as well as the asset.
But back to the opening example: handover. In both traditional all-at-once and piecemeal progressive handover, the operator and contractors need to transfer and validate hundreds or thousands of documents across many disciplines, each created with a different toolset. Projects that choose a digital, data-centric approach for handover and operations have a head start: they avoid the mistakes and losses that seem to be the norm with paper-based processes.
If the contractor and operator agree that a digital twin makes more sense, they must work together to define this “handover twin.”
They must design the twin so that it will fit into the plant’s maintenance and operations process and then integrate it into the operator’s digital environment. This could mean connecting PlantSight to IIoT data, to the operator’s ERP system, to the CMMS for maintenance procedures and work orders, to the plant’s process simulation tools for start-up testing and training, and to build up a library of what-if scenarios for operations.
Transferring a PlantSight digital twin instead of paper,
- Creates confidence that the operator will have the data they need to deal with both routine and exceptional issues from day one
- That data will be accessible from one easy-to-navigate portal, rather than distributed across platforms and data formats
- The data will be in context, meaning each piece of equipment will know where it is in the plant’s physical layout, and what system it connects into. Any other pertinent data is a mouse-click away
- As the source data is updated, Plant Sight will also update, meaning that the data as current as the latest sync.
- In summary, PlantSight delivers a complete, living digital twin that can help plant operators run with greater confidence.
This brief was created by Schnitger Corporation at the request of Bentley Systems, Inc