Steam Trap Inspection Basics Using Ultrasound
High energy prices and global competition dictate a need to reduce energy waste and improve system efficiencies whenever possible. Steam, aside from being one of the costliest utilities in plants, is an essential component to product quality in many processing industries.
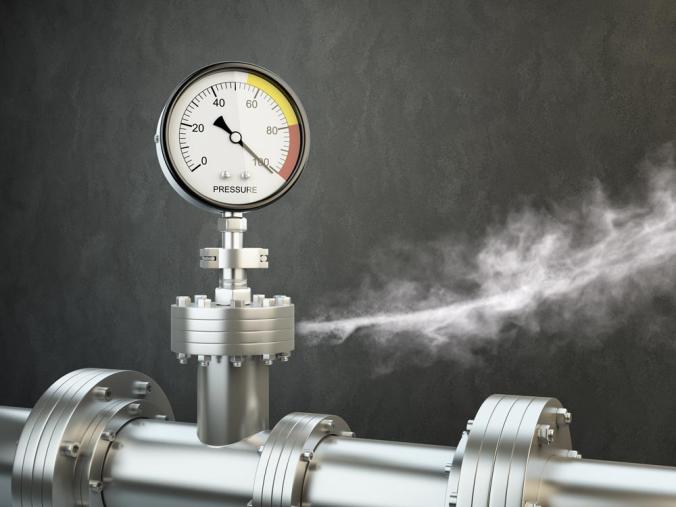
A major contributor to waste and inefficiency is leaks: both to atmosphere and through valves and steam traps. According to the United States Department of Energy, a typical facility can realize steam savings of 20 percent by improving their steam system. Experts have also said that as much as one fifth of the steam generated at the central boiler is lost to leaking or failed steam traps. With current steam prices averaging between $8.00 to $12.00 per thousand pounds of steam, a steam trap inspection programme is a must. For example, if a steam trap with an orifice size of 3/32” (2,4 mm.) operating at 100 psi (7 bar) steam can lose nearly 30 lbs. (14 kg.) of steam per hour. At a cost of $8.00/1000lbs. of steam, that results in a loss of over $2,000 per year from just one failed steam trap.
The purpose of a successful steam trap inspection programme should be to repair any faulty steam traps and steam leaks that can impact safety, to reduce energy waste and promote sustainability, and to repair any failed steam traps and steam leaks that impact product quality.
Why Ultrasound?
Ultrasound technology is used by maintenance and reliability professionals around the world, and is considered to be the most versatile of any Predictive maintenance (PdM) technology. Typical applications for ultrasound include compressed air & gas leak detection, bearing inspection, motors, gearboxes, electrical inspection of energized electrical equipment, valves, hydraulic applications and steam traps.
However, when it comes to steam trap inspection, one technology alone can’t do everything. World Class maintenance and reliability programmes utilize multiple inspection technologies when it comes to inspecting the assets that they are responsible for. Visual inspection, temperature measurement, and ultrasound should all be used during a steam trap inspection route.
Planning for Success
Before beginning any steam trap inspection, it will be helpful to think a few things through that will help to make the survey successful. First, walk the area to identify and tag every steam trap. The tag should include a number, and all information should be noted, such as the manufacturer, type of steam trap, orifice size and the purpose of the steam trap. This information can then be entered into data management software, such as UE Systems’ Ultratrend DMS.
While walking the area, it would also be a good idea to note any possible accessibility issues: will a ladder or man-lift be needed for any steam traps that are overhead and out of reach? Are any steam traps located in areas where Lock-Out-Tag-Out procedures will need to be followed? Are any of the steam traps inside of hazardous areas where Intrinsically Safe instruments will be required?
Testing Steam Traps with Ultrasound
To make it easier to manage the data for reporting and inspection purposes, it is recommended to break the inspection areas into zones. Follow a logical progression from steam production, steam use, and condensate return. Start at the boiler, then to the steam distribution and distribution branches. Then, proceed to process equipment, and finally to the condensate recovery systems.
When the inspector is at the steam trap, before testing with ultrasound, it is recommended to take temperature readings with a simple spot radiometer first. Not only will the temperature let the inspector know if steam is coming to the trap or not, but the temperature can also be used to estimate the steam pressure. If the temperature of the steam trap is cold, the inspector should check to make sure that the valves are open or if the trap has been taken out of service. If it is warm/hot, then the inspector can note the inlet and outlet temperatures and proceed to test with ultrasound.
The most important item that the inspector will need to know is which type of trap is being inspected. Knowing the type will determine what the steam trap should sound like once contact has been made with the ultrasound instrument. Steam traps will have one of the following sound characteristics: On/Off or Continuous Flow.
Typical types of steam traps that have the On/Off (hold/discharge/hold) sound are: Inverted Bucket, Thermodynamic, Thermostatic (Bellows), and Bi-Metallic. Steam traps with a continuous flow sound characteristic are: Float & Thermostatic and Fixed Orifice. It is recommended that you listen to a number of steam traps prior to starting the inspection to determine a “normal” sound characteristic for how it is operating under the normal conditions of your steam system.
Physical contact between the steam trap and the ultrasound instrument is necessary in order to “hear” how the steam trap is performing. If using an ultrasound instrument that has frequency tuning, adjust it to the recommending frequency setting of 25kHz. If it does not have frequency tuning, it is more than likely set to 38kHz. Regardless of the type of trap, the placement of the contact probe or stethoscope module attachment on the ultrasound instrument will always be at the discharge orifice of the steam trap, since turbulence is created on the outlet side of the steam trap when the steam trap releases condensate.
Once contact has been made, adjust the sensitivity/volume on the instrument until the sound of the trap can be heard.
When inspecting steam traps with ultrasound, it is important to exercise patience. Make contact at the discharge orifice and wait for the steam trap to cycle. If the temperatures have been checked, and the trap has not cycled for approximately one minute, move on to the next steam trap. If the steam trap has not cycled within one minute’s time, it may be difficult to know when the trap may cycle again, but if the temperatures are ok and there’s no indication of a plugged condition, proceed to the next steam trap to be tested. When first starting out, it may be helpful to compare sound characteristics from similar types of steam traps to help the inspector learn what a good or failing steam trap sounds like.
Reporting the Results
Now that the inspector has gathered all the information for the condition of the steam traps that were inspected, it is important to document the findings. Not only should the operating condition of the steam trap such as failed, leaking, or ok be reported, but also the loses from the failed or leaking steam traps. To generate a Steam Loss Report in the Ultratrend DMS software from UE Systems, the inspector will need to know the following for each steam trap: Type of Trap, Orifice Size, Inlet & Outlet Temperature, Operating Condition and how much it is costing to generate 1000lbs (450 kg.) of steam.
With an increased focus on energy and sustainability within our industry, steam trap testing with ultrasound is a great way to show potential customers and suppliers that energy loss is taken seriously and that there is a continuous effort being made to correct problems related to energy loss. Ultrasound instruments are valuable inspection tools that can not only provide insight into the health of steam traps, but also other components of the steam system such as heat exchangers, shutoff valves, control valves, solenoids, relief valves, cavitation in condensate return pumps, and steam leaks to atmosphere.
Examples of steam trap sound recordings can be found at
www.uesystems.eu/sounds/