How to Safely Align Wind Turbines
Safety engineers around the world can breathe easy. The PRUFTECHNIK ROTALIGN® and OPTALIGN® technology has made aligning machine shafts, especially gear shafts, much safer.
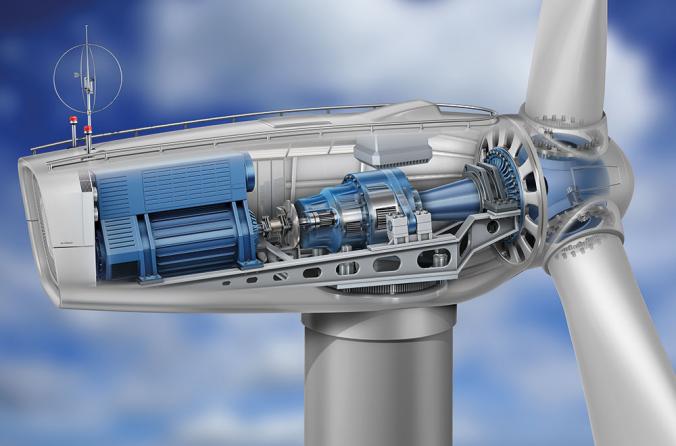
Text and photos: Pruftechnik
Coupled shafts that may not be rotated by hand during the alignment measurement, such as in gear generator wind turbines, can be measured absolutely safely for alignment thanks to the unique laser sensor technology. By now, this process has advanced so much that manufacturers of wind turbines explicitly require this special technology from Bavaria because of the special HSE regulations (Health and Safety Execution)!
The example gear generator wind turbine illustrates the importance of occupational safety. We all agree that an extremely heavy wind turbine rotor with a rotor blade diameter of well over one hundred or even two hundred meters generates tremendous forces on the generator shaft already at a low rotational speed – especially when a gear is interposed.
The rotor blades transfer the energy into a rotational movement in order to generate pure energy from wind in the form of electricity. The rotational movement runs via the hub into a directly connected gearbox in order to optimize the running speed for the power generator. The simple laws of physics suggest that the extreme leverage effects of the rotor blade to the input shaft create a tremendously high torque at the coupling from the gearbox to the generator shaft. Therefore for safety reasons, the complete drive linkage must operate under a protective cover during normal operation.
A special challenge is now the alignment of the gear shaft to the generator drive shaft. Both shafts are regularly connected to each other via a coupling. However, both shafts and the coupling run “invisibly” under the protective cover. In order to ensure a safe, trouble-free and low-maintenance operation, both shafts must be aligned precisely to each other within the specified tolerances. The only safe and precise way to align both shafts of the manufacturer’s specifications accordingly is the laser-optical alignment procedure. In the process, a laser and a sensor are mounted onto the coupled shaft, rotated around the shaft axis, thereby measuring the alignment. But this is exactly where the crux lies!
The cover of the drive linkage may only be removed if the system is shut down. In other words, the rotor must be secured against strong gusts of wind with the service brake and at the same time also mechanically with a locking pin. This ensures that no torque can be transferred to the input shaft. Conversely, however, this also means that the shaft cannot be rotated for the alignment measurement. The process is thus virtually impossible: The cover has been opened to mount the laser-sensor unit and cannot be closed with the measurement device installed. According to HSE regulations, it is not permitted to tamper with the open drive linkage with a freely rotatable rotor! The brake and locking pin rule out a manual rotation.
Nevertheless, PRUFTECHNIK technology makes a simple, quick and above all safe alignment measurement possible while remaining within the bounds of occupational safety! Once the laser-sensor unit has been securely mounted, the service brake and the locking pin are released. The rotor blades are turned by the wind so that a rolling operation is briefly set. The on-site maintenance workers move as far back from the shaft as possible or to a safe location, even in the narrow enclosure if possible, during the axial rotation. PRUFTECHNIK’s own SWEEP-Mode in the ROTALIGN® and OPTALIGN® alignment devices makes it possible to determine the quality of the alignment in any angle position. This is already possible from a minimum torque angle of just 60° degrees. During the shaft rotation, all readings are automatically and continuously recorded. However, in practice a wind turbine can never be stopped again so quickly. Several rotations at once are the reality and are absolutely no problem in SWEEP mode. On the contrary: the higher the torque angle, the more precise the measurement.
The ROTALIGN® or OPTALIGN® computer calculates the alignment result in just a few seconds. The angular position at which the laser-sensor unit comes to a standstill does not matter here. The sophisticated sensors with two detector surfaces can calculate the alignment result from any position in which they are located. They do not have to be rotated to a certain work position for this purpose, which is almost impossible given the technical prerequisites in the wind turbine without endangering one’s own health by manually intervening in the input shaft. The PRUFTECHNIK technology is completely contact-free and does not require any additional manual controls. Of course, all brake and locking mechanisms must be active again for the subsequent mechanical alignment process: Rotor brake on, locking pin locked! The laser and sensor remain mounted to monitor the alignment process.
Since all braking device are activated, the shaft cover can still remain opened. In PRUFTECHNIK’s own “Live Move” function of ROTALIGN® and OPTALIGN®, the alignment result can be tracked at any time in real time (i.e. ‘live’) until the alignment targets are met at the end! HSE regulations must also be observed and implemented here. There is no conflict here with the PRUFTECHNIK devices. The work steps can be carried out properly and with the necessary care.
This safe alignment process means that operators of wind turbines have already become aware of it. The unique safe PRUFTECHNIK procedure has therefore already found its way into various installation instructions of wind turbine manufacturers. They explicitly refer to the obligatory use of only PRUFTECHNIK equipment. The world market leader for laser optical alignment equipment from Bavaria is therefore synonymous with perfect and safe alignment in the wind turbine industry. The PRUFTECHNIK devices from the ROTALIGN® and OPTALIGN® series perfectly symbolize the two most important features of aligning wind turbines: Safety and Precision!