Digitalisation of production systems:
The fact that digitalisation of production systems is progressing has become an established consensus among manufacturers, operators, and service providers in the mechanical engineering sector. At the same time however, statements such as the following from T-Systems often cause uncertainty among OEMs in the mechanical engineering sector: “Digitization is disrupting existing”.
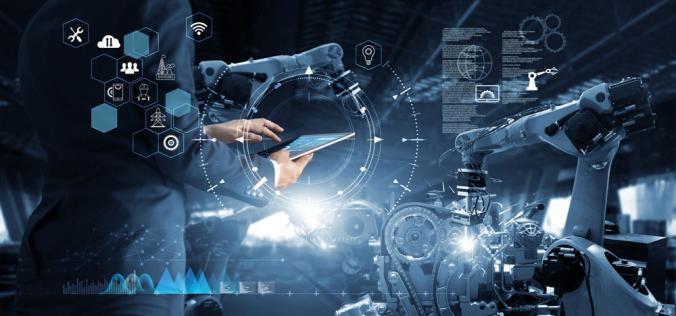
The correlation, as well as the resulting transformations of business models and the associated risks, must be viewed in a highly differentiated manner. The mechanical engineering sector in particular, featuring its typical structure of SMEs and "hidden champions", is in a very good position worldwide to perceive digitalisation not as a threat but as an opportunity to expand existing business models and, over the long term, to open up new markets by leveraging new technologies. In the final instance, it is clear to all business players that digitalisation will secure the long-term competitiveness of OEMs in the mechanical and plant engineering sector.
Which arguments support such a view?
1. Digitalisation can only be successfully mastered in many individual steps. For those involved, this cannot be about all-encompassing umbrella functionalities, as described under the terms "IIoT", "Industry 4.0", "Digital Engineering" and the like. Far more, it is about concrete approaches that can be used to advance the efficiency and cost-effectiveness of machines along the entire "life cycle" with as little input and effort as possible. And because automation in mechanical engineering has been driven principally by digitalisation for decades, it is primarily those OEMs that can successfully implement these approaches based on their core competencies. Only OEMs are able to implement specific measures that combine existing functionalities and systems with the most promising new control and data transmission technologies! [2]
2. Digitalisation in industry is often mentioned along with the keyword "Industry 4.0", a term which stands for the 4th industrial revolution: consequently, the disruptive potential of current technical developments is equated with the effects of the industrial use of steam engines, electricity and computers. Successful players such as Amazon, Microsoft and Google are often cited as prominent examples of the forces of change. In the case of the medium-sized mechanical and plant engineering industry, on the other hand, these developments appear at least partly as a threat. The protagonists of digitalisation are endeavouring to take the edge off this.
Hans Beckhoff, the founder and CEO of Beckhoff Automation, very aptly explained during an IHK event in 2017 that these changes and shifts represent opportunities for industrial manufacturing and that the speed of the upheaval is slower than initially assumed: "From today's perspective, the introduction of the steam engine seems like a revolution. However, at the time it took more than half a century for its use in industry to result in substantial changes." In a similar manner, he stated, one should regard the impact of digitalisation for industrial production today, which is triggering an evolutionary development at all levels and in all processes. At the same time, Beckhoff also emphasises that this realisation by no means guarantees that one should sit back and do nothing! According to Beckhoff, it is precisely the courageous protagonists who will be rewarded if they creatively develop new business models for production systems.
HARTING has analysed the implementation strategies of its customers and can decidedly confirm Beckhoff's theses. Accordingly, in order to achieve sustainable success with digitalisation projects, it is above all advisable not to want to achieve everything immediately [3].
Whether the development is revolutionary or evolutionary: All parties involved agree that data forms the basis of more rational processes - and indeed all types of data. The catch phrase "Data is the new oil!" originally referred to "Big Data" or the storage and availability of consumer data. But this characterisation can certainly also be applied to data in the industrial arena. However, to stay with the metaphor, this "new oil" still requires functioning "pipelines" and other structural elements.
Consequently, "Data is the new oil" not least describes the current situation of many machine and plant manufacturers who are in the process of revising the generation, processing and transmission of data for their products.
The OEM's "data view" of production systems today can be summarised as follows:
- OEMs are experts for many existing technological, machine-related data, as well as for the use of this data in intrinsic machine functions, and for advanced automation functions
- The increased use of the "internal intelligence" of automation components such as drives, smart sensors, actuators or HMI systems with all the associated data transitions is also part of an OEM's standard toolkit today
- In addition, this comprises all possible data transfer layers on the level of interlinked machine or production lines that use known data origin, machine, user and process models, which are also considered proprietary know-how
- However: In terms of digitalisation, not all the aforementioned data structures and transmission layers that are part of the control and automation systems should simply be "discarded" and replaced by new ones. This is due to the fact that almost the entire functionality of modern production systems is based on software and suitable specific interfaces - these functionalities have been developed with an enormous amount of material and engineering effort.
Consequently, an initial conclusion is as follows: In order to drive digitalisation forward with as little effort and input as possible and to cope with the associated rising data volumes, machine and plant manufacturers must be able to continue to use existing data structures and interfaces!
In the sense of ‘the data is the new oil’ analogy, proven and sufficiently functional "pipeline structures" must continue to be used and extended to include new "pipelines".
In this way, companies will succeed in enhancing their competitiveness and gaining new market shares in their own business segment or in other fields of production technology. To put it in terms of control technology for industrial systems: An OEM active in mechanical engineering needs its proven fieldbuses and interfaces for evolutionary digitalisation. At the same time, suitable physical interfaces are advantageous for the expansion of new systems and services in the edge areas, as well as for the most seamless connection possible to the world of "Big Data". Players mastering both disciplines will be best equipped to meet the growing and, in some cases, still unknown future requirements of machine users.
The trend-setting requirements for developments related to digitalisation outlined in the following section are based on the experience of the HARTING Technology Group. The company provides solutions for all types of data interfaces of modern drive, control, HMI and communication technology in mechanical engineering production systems. HARTING is also a pioneer in many ground-breaking developments for power and signal transmission in the industrial arena. In the field of Industrial Ethernet,
HARTING is playing a key role in shaping and designing various standards on the physical layer: for example, the company is actively involved in solutions for the so-called SPE (Single Pair Ethernet) technology.
Decades of experience in the field of interfaces for factory automation, combined with the expertise of a trendsetter in the latest data transmission technologies (including the "Big Data" world), make it possible from HARTING's viewpoint to always find optimal solutions on the physical layer for each and every specific interface design. With the help of the right interfaces, OEMs can decisively drive the migration to digitalisation forward that is so vital for them. In each solution here, the respective application with its mechanical, environmental and EMC conditions and other requirements must remain leading.
"What is the simplest and most effective way to design data transmission interfaces in production systems - at all conceivable levels of the factory and all the way into the 'cloud'? " This question often causes headaches in the R&D and engineering departments of machine building companies that want to gradually shape and design individual actual digitalisation aspects in their projects. The requirements that need to be met are as follows:
- All types of data interfaces should be implementable, both well-proven but also current innovations
- The range of interfaces must be scalable, i.e., the same interface type can be designed in the required normative version, IP protection class or for the required environmental conditions (EMC, resistance to dirt, UV radiation, mechanical stresses such as shock & vibration or the hygiene requirements)
- With regard to the transitions between sites or sections, it must be possible to use interfaces that function reliably and conform to standards
- Product variants must be available that are designed for different manufacturing and assembly processes at the OEM, e.g., for tool-free assembly if flexibility is required, or for automatic assembly in the case that higher quantities are to be manufactured in connection with a high level of process reliability
- Data interfaces must be combinable with each other and must be placeable with other signal and power interfaces in one enclosure or even together in one insulator in order to save space and costs and to simplify processes.
The approach outlined above allows developers and project managers to concentrate on the central tasks for their respective application during the design phase - without having to spend time on the "less important criteria" of interfaces. At the same time, they can be certain that there is a suitable interface available for every expansion stage of a machine module or a data transmission link. The corresponding solutions are both cost- and function-optimised and scalable. The cost-efficient, technically straight forward expansion of services and system extensions at all levels of factory automation and beyond can be implemented at any time, even retroactively, at the respective machine user.
Figure 1 presents the approach in an exemplary way: It provides an overview of the best-known network systems for industrial data transmission and describes selected actual HARTING solutions, which are shown as product families. It is apparent exactly how great the freedom in the design of the data interfaces actually is: for practically every type of field bus or Industrial Ethernet there are several options available for designing the physical layer. This means that it is (almost) always possible to find a solution that is optimally suited to the application - even for requirements that are still unknown today and/or for digitalisation requirements that are growing along with the application.
Dipl.-Ing. Jakob Dück, Global Industry Segment Manager
Sources:
[1] T-Systems: Accelerate Digitalisation (
t-systems.com
)
[2] HMS: "The goal is to generate value from data."(industry-of-things.com)
[3] HARTING:
http://www.us-tech.com/RelId/2651702/ISvars/default/Weighing_the_Cost_and_Benefits_of_Digitalization_in_Manufacturing.htm