Bilfinger Maintenance ensures innovative shaft alignment
When it comes to shaft alignment, experts from industrial service provider Bilfinger have relied on the co-operation with Swedish company Easy-Laser for nearly two decades. Now, the company is introducing a new generation of devices, which will greatly simplify the alignment process for clients and employees, especially in potentially explosive environments.
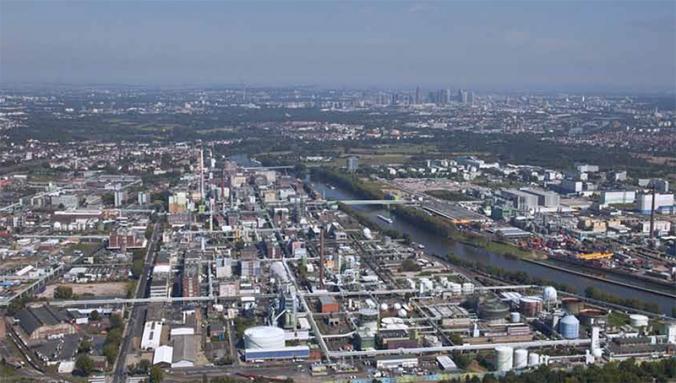
MAINTENANCE PERSONNEL at Bilfinger Maintenance in Höchst have been using laser-based measurement and alignment systems from Easy-Laser since 2001.
In addition to cost factors, the main deciding factor in our collaboration with Easy-Laser was their user interface, which is easy to understand and, there-fore, very user-friendly, explained Karl-Heinz Bank, head of Machine Technology and Service Technicians at Bilfinger Maintenance in Höchst.
In spring this year, the good working relationship strengthened further. After Easy-Laser had officially launched their XT550 EX shaft alignment system at the Hannover trade show, the innovative measurement system was delivered to Bilfinger, who was the first customer.
Without doubt, the old systems that had been in use for a long time were still reliable, as confirmed by Mr. Jurgen Rabe, Head of Pump and Engine Technology at Bilfinger in Höchst. However, the industry had been waiting with great anticipation for a new shaft alignment system.
Explosion protection is essential
A big plus for the intrinsically safe XT550 EX is its ATEX and IECEx-certification: The system can be used in the explosive atmospheres of zone 1 and 2, without the customer needing a separate ‘hot permit’ and having to shut down his production, which always means significant financial and time-consuming expenditure.
XT550 EX. There can still be an explosive environment and the neighbouring production line can carry on running as normal. This is a big advantage, saving considerable time for both us and the customer. To give you an example, we would never have gotten a hot permit from one key customer at all. Without an explosion protected laser device, we would not have been able to proceed, Rabe adds.
Advantages for maintenance staff and customers
Bilfinger employees have received intensive training for the new system and soon had come to grips with the new device. One of the special features is the intuitive user interface, no longer in 2D but in 3D. Also, you can choose from four different measurement methods: Measurements using the 9-12-3 method, the Easy Turn method, taking any three measurement points within a small angle of rotation, multipoint measuring and the very easy-to-use continuous sweep, with automatic, continuous measurement value collection during shaft rotation. Together with the locked feet function, the system solves also tricky alignment problems. In addition, there are many accessories that can be used.
A real bonus of the new Easy-Laser Generation XT is the extremely easy documentation of measurement results. When a machine has been repaired, operators need to carry out a check to comply with the official regulations on safety and health before recommissioning the system. And to do this, a certificate is needed.
Measurements and alignments with gauges are cumbersome: Gauges need to be precisely mounted to measure an assembly unit and values must then be read from the dial indicators and recorded manually. Later, back in the office, documentation containing the measurement report has to be entered into the computer. This documentation has to be signed and presented to the customer.
With the XT alignment systems, the user is on-site to carry out measurements and then creates a measurement report within the system, including graphs in a PDF or Excel format, before sending it off electronically. In addition, the measurement report can easily be saved to the system and can be re-used at a later date for new measurements.
This saves a lot of time and makes it easier for the customer because he has the documentation on his desk straight away and can start operating the machine again straight away, says Bank.
Using this technique has helped us to take documentation to a whole new level.
Mechanical processes have had their time
It is obvious why experienced pump and mechanical experts at Bilfinger only carry out alignments with laser measurement and alignment systems.
Working with four to eight gauges is a real science. The great advantage of modern technology is that it gives us precise values. Measuring with straight edges and light gaps always give room for interpretation. Here, we’re talking about measurements in hundredths and thousandths. For precision, a laser-based system is imperative, affirms Bank.
It is the customers that reap the benefits. The pure acquisition costs of pumps are only a fraction of their lifecycle costs. By far the greatest costs are energy usage, repairs and maintenance. For a precisely aligned shaft within the required tolerances, the lifespan of wear parts like bearings or couplings is significantly higher than for shafts without precision alignment, which eventually also influences the performance of the engine.
If a pump is not sufficiently aligned, in most cases, there will be damage to bearings sooner or later, says Rabe.
In the meantime, we perform a laser alignment for all pump completions so that we can document that the unit is correctly aligned. More and more customers are asking for these services as part of an on-site system exchange, he adds.
Flexibility is king
Bilfinger Maintenance is certain of one thing: In this industry, more and more work processes are going digital, so there is obviously an increasing need for alignment with flexible digital measuring instruments. Easy-Laser has responded to this development and offers all XT measuring programs for shaft alignment within a free app that works with iOS and Android tablets and smartphones. On those, also other applications can be run. Other systems that use the manufacturer’s proprietary display unit usually provide only the manufacturer’s application.
The XT550 EX is the first system to be equipped with an “open” tablet. If we need to, we can easily load the app onto another device and continue work-ing, emphasises Rabe.
Bilfinger service engineers are already considering buying a new Easy-Laser system to respond to increasing needs.
EASY-LASER AB,
www.easylaser.com
Information on Bilfinger
Bilfinger is a leading international industrial service provider. The business model increases the reliability of plants, ensures a high level of availability and reduces maintenance costs. Their portfolio covers the entire value-added chain: from consulting, engineering, production, installation, maintenance, plant extensions and their general overhaul up to environmental technology and digital applications. With around 36,000 employees, in 2017, Bilfinger generated a sales revenue of around 4.044 billion euros.