The Five Most Expensive Savings Ideas for the Maintenance of Machinery and Equipment
Machine downtime is always expensive, especially if a whole production line comes to a standstill as a result. For new machinery, the machine manufacturer is still liable, but afterwards the responsibility for maintenance lies solely with the user. Maintenance staff must constantly justify their "unproductive" costs and, hence, try to reduce them. However, some short-term saving ideas lead to nothing but higher total costs in the end. The following are the five most expensive, and unfortunately, not uncommon errors when it comes to machine maintenance.
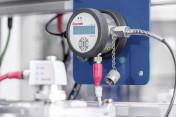
Waiting for wear and tear
This is the classic service approach, as it has been implemented since the beginning of machine manufacturing: comply with regular maintenance intervals and if a component should fail in the meantime, then replace it while being pressed for time. This strategy accepted downtime and surcharges for faster service because there was, for a long time, simply no alternative. This is no longer the case. Modern concepts use sensors and analysis software to detect wear and tear caused by changes in the operating conditions before it leads to a failure. If a component shows signs of wear, then maintenance staff receives an appropriate warning. They can then schedule replacement work during production-free time, order the spare parts without an express surcharge, and make the replacements calmly.
A different service provider for every technology
At first glance, the savings potential is clear: for the maintenance of control technology, service provider A has the best offer, for the hydraulics service provider B wins, and for mechanical questions, C gets the deal. No problem in routine cases, but as soon as things becomes more complex, the coordination effort grows enormously. Is it really a problem involving the hydraulics or the control? The buck is passed back and forth and then different service providers work simultaneously on the machine, incurring substantial costs. In this case, it helps to get a service provider for the entire drive and control technology as a partner right from the outset. Now they need to have a handle on the complexity involved.
Replace rather than repair
Under time pressure, the simple solutions are often the most popular, but rarely the least expensive ones. Complex assemblies, such as axial piston pumps are naturally subject to wear and tear. When it's time for servicing, it's easiest to order and install a new pump. With a little preparation, maintenance departments can significantly lower these costs. Manufacturers such as Bosch Rexroth provide exchange programs as an alternative to purchasing new components and assemblies. The replacement of a worn pump with an expertly reconditioned one saves costs and yet provides security because the manufacturer offers a new part warranty. And particularly useful for companies that use many such components: make a deal with the manufacturer to keep a defined number of outdated assemblies always in stock. If the maintenance department takes out a pump, the stock is replenished automatically.
Delaying modernizations
Never change a winning team - some companies also follow this approach when it comes to the electronic components in their machines, such as controls and the corresponding software. If they should fail after a long period, it may be too late for an easy replacement because the lifetime of electronic components is generally shorter than that of mechanical components. Whoever relies on being able to buy an original control unit from the 1990s or early 2000s might have bad luck when the time comes. Since then, most manufacturers have developed several product generations, and the current versions are not compatible with those of the past 10, 15 or 20 years. Often, the transition requires high programming costs and changes to the electric and automation equipment. The solution: regularly modernize electronic components. This increases the productivity of the machines and ensures their service ability: replacing a modern and powerful control board takes only a few minutes, completely reprogramming them can take weeks.
Savings on spare parts
It awakens the bargain hunter in all of us: special offers for spare parts, which sometimes cost only a fraction of what the manufacturer charges. A few clicks and you save vast amounts of money – or so it seems. These cheap deals are often fakes. From the outside, they strongly resemble the original parts, but they're often vastly inferior in terms of their performance and service life. Alleged savings are quickly lost since such devices wear out much faster, and therefore, lead to more frequent downtime. The use of reconstructed spare parts can lead to significant damage and loss of production. Penny wise, dollar foolish.