Condition Monitoring Systems Readdressed and Revised
Industry is turning from conventional condition monitoring systems to three areas of maintenance, namely safety, monitoring, and diagnosis.
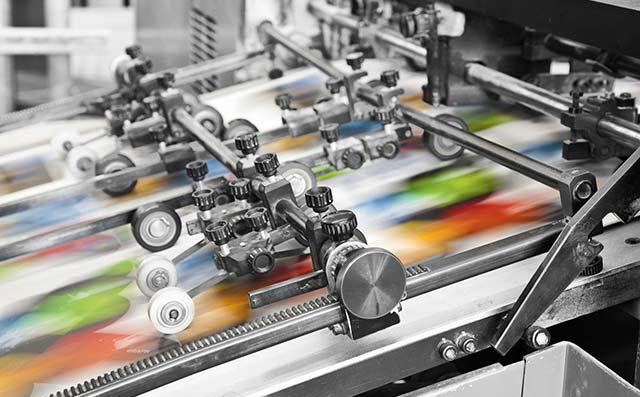
Big CMS players (companies like B&K, GE – including former Bently Nevada, SKF, Emerson, Allan-Bradley) have worked out a solid position on the maintenance market. However, the implementation of such brand name systems directs towards critical machinery and machinery, which calls for monitoring by regulations rather than solid industrial needs.
Due to a recent regress in the economy, potential private investments to CMS have decreased significantly, and industries are not interested as much in machine learning as they used to be. As a consequence, systems providing just monitoring functionality have become difficult to sell.
This scenario has readdressed, and currently redefined the expectations of condition monitoring systems. The currently accepted model changed direction from the typical monitoring activities to three explicit areas of maintenance, namely safety, monitoring, and diagnosis.
In this way, the literal notion of a classical CMS is no longer valid because it is too narrow. Moreover, a notion of SM&D (system of monitoring and diagnosis) is also too narrow. Therefore, a notion of safety-monitoring-and-diagnostic system seems more appropriate. The three aspects are discussed below.
Protection of Important Machines
Firstly, a currently demanded system is expected to be able to react real-time or quasi real-time upon detection of dangerous machine technical condition. Data collected and processes in a relatively high time resolution is processed, a number of predefined scalar analyses is calculated, and each of them is compared against allowable value, typical so-called alert threshold levels.
In case of threshold trespass, plus some possible hysteresis logic, an output (analogue or digital) is generated and sent directly to a relay, SCADA, or any other unit enabling the machine to immediate stop. In order to fulfil this requirement, the system must be characterized by high reliability, availability, and responsiveness. Because these features are typical for real-time operations, currently desired CMS are expected to be embedded on real-time operational systems platforms.
One of the aspects concerning protection, which still draw attention are recipes for setting threshold levels. Currently, three approaches are implemented. They are absolute values from norms, relative values from guidelines, and internal historical references.
In the first case, the most commonly applied norm are parts of a general ISO 10816 with a recently published group of ISO 13379 concerning data interpretation and diagnostic techniques. In the second case, guidelines provided by large CMS designers mention relative change of factors 2.5 and 10 as warning and raising an alarm respectively.
It is worth mentioning that it is still a large drawback of norms that they operate on wideband estimators, like root-mean-square of a velocity signal, which generally do not enable detection of fault development at an early stage. However, early fault detection is not crucial for protection of a machine.
Continuous Monitoring of Machine Health
Secondly, industrial clients expect improvements of the classical added value of CMS, which is monitoring of the machine health. In order to provide attractive monitoring, a system needs to provide an easy way to access and display all current and historical data on demand with a delay not exceeding a few seconds with a high degree of flexibility and display arrangement.
This expectation in turn imposes implementation of modern IT solutions, like instant and automated data transfer from an embedded unit to a local computer or to a database in case of a distributed system. It also includes the instant display of approximated large data sets, processing of very large raw data on demand, customized arrangement of things to display (like window undocking and moving to another screen) and user workspace definition, and finally user-friendly access to many features without displaying them all at a time, for instance with the use of ribbon technologies.
In opposition to protection, monitoring is expected to provide a clear upgrade from fault detection to identification. It should provide information that something is incorrect, and give details as what it is. In order to fulfil the latter requirement, a system needs to include a kinematic configuration of a machine with a phase marker. So it is a scheme that relates rotation of all the shafts to a reference rotation, on the basis of which characteristic component mechanical elements are automatically calculated.
Diagnostic Tools Are Needed
Tertiary, a modern CMS system needs to provide a variety of diagnostic tools. Typically those are charts and data extraction procedures for advanced data analysis. Such tools include in general verification of raw data against process channels, selection of raw data for referential analysis and display of historical data for fleet comparative analysis in case of distributed systems.
One particular demand that has been highly recognized by industrial clients is the access to all data that system records, and all data that the system calculates. It is no longer acceptable that CMS manufacturers provide only selected and moreover decimated data for customer, and require additional fees for further data access. With the usage of universal file formats, it is expected that a client is able to extract any data from the system, and process it with a customized application if needed.
Finally, regarding a general status of condition monitoring in recent years, certain aspects of development of condition monitoring and diagnostic systems have proven to be a success or a failure or at least have not reached expected level of maturity, which is summarized in table 1.
As illustrated in table 1, it turns out that industrial clients are not interested in fancy graphical solutions, because ultimately, after initially being amazed, a user becomes bored with too many pictographs. The wireless sensors still have footnotes about the final uncertainty of a range depending on a particular setup.
Large databases are currently not attractive because it is difficult to take high license costs without systems verification. And finally, the scientific achievements of analysis of root causes of failures are still customized sessions, and ready-to-use solutions are not available.
All of the above mentioned rough assessment given from industry might serve as a general guideline for CMS development or pivots for discussions serving towards the ultimate goal of an increase in safety, reliability, and maintenance costs.