Ten Tips to Tune Your Servo Hydraulic Machine for Profit-Making
Performing pre-emptive, scheduled maintenance is the key to not only extending the life of your equipment but also protecting profits. Ignoring something because it is already running, or cutting corners for the sake of expediency takes uptime out of your control and puts it into the hands of luck.
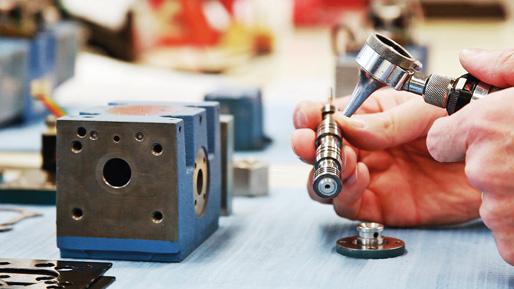
If you regularly change your car’s oil and oil filter, you might expect your engine to last more than 400,000 kilometers. Ignore that schedule, and you will be lucky to get a third of that distance. Some industries are better than others about pre-emptive maintenance.
For example, the power-generation industry knows that running a machine and its parts to failure can lead to a unit shutdown. Failure for power plants means buying energy on the spot market. Ultimately, the plant cuts into its profits and loses money. Here are ten tips to stretch uptime, revenue and the life of your machine.
1. Commit to Fluid Cleanliness
Hydraulic systems require clean fluid. For companies that invest in servo control components, the servo valve is key to either the speed or position (or both) of the most critical axes on the machine; companies must keep servo valves running in severe environments including high temperatures and 24/7 operations.
The servo valve also has extremely small parts manufactured to very tight tolerances. Precision is necessary to meet the performance objectives of a machine and ensure it achieves the desired product quality or production throughput.
What does clean mean? ISO standard 4406 measures cleanliness as the quantity of particles at different sizes in fluid. There are two ISO 4406 cleanliness standards for servo valves. The first, 14/11 (ISO 4406:1987) or 17/14/11 (ISO 4406:1999), allows the valve to function as designed with an average wear rate. The second standard – offering extended life and performance – is: 13/10 (ISO 4406:1987) or 16/13/10 (ISO 4406:1999).
2. Analyze Oil Regularly
The price of analysis has dropped considerably with laser particle count technologies. Request one monthly. After three consecutive passing grades, slowly increase the period between analyses. Remember to analyze at least once per quarter.
3. Double-Check Your Oil Analysis
The accuracy of a laser count can deteriorate whenever there is a high degree of variability in particle size. Smaller particles can go undetected behind larger particles, which shield them from a laser count.
So check the results at least annually with the patch-count method. With patch-count, a technician runs fluid through the patch and counts the different sized particulate. The patch-count method can detect particles 2 micrometers and larger.
4. Use Proper Filter Elements
Use a filter element that filters the fluid to the required standard. If full-flow elements cannot meet your system requirements, consider adding a kidney loop filtration system (See Tip 8.) Some purchasing departments will focus on the filter element’s size and not understand the ISO standard you are trying to meet. In so doing, they will source a less expensive filter, but it will not be designed for your needs.
5. Make Sure Breathers Are Installed in the Hydraulic System
Poor breather maintenance leads to contaminated fluid. All hydraulic systems have tanks with a breather to filter the air that enters. In some cases, workers will remove the breather because these components become clogged and interrupt operation of the system, especially in a work environment with a lot of dirt and dust. By doing so, they are ignoring the purpose of the breather.
There are many breathers for any given environment, including integral desiccant systems to prevent condensation in your reservoir or crankcase. A qualified distributor will know a filtration expert who can ensure your breather and servo valves run properly.
6. Drain, Clean and Flush when Changing Oil
When changing oil, it stirs up a lot of particulates and debris. Drain the system and clean the sump whenever changing oil. Install flushing blocks on servo and proportional valves to bypass this equipment during commissioning to clean the fluid prior to start-up.
7. Filter New Oil
Do not assume new oil is clean enough for a system. Filter new oil to meet the system requirements before pumping it into the reservoir. Keep in mind that brand new oil does not meet the recommended ISO requirement, since it is usually 18/12, not the 13/10 or 14/11 needed for operating precision equipment.
8. Consider Using Kidney Loop Filtration
Installing a kidney loop filtration system is a cost-effective way to clean oil, while the main system is offline. These systems come with many options such as micron filtration size, dirt indicators and water retention systems.
9. Monitor the System with Predictive Maintenance
Many companies monitor servo valve performance by recording the amount of current it typically takes to hold the actuator or system mid-stroke or at null. Technicians place minimum and maximum limits around the current and track the performance over time.
For example, a 10-milliamp (mA) valve might operate at 5 mA to hold position at null in a closed-loop system.
The limit could be +/- 1.5 mA. If the current passes over the established threshold, check the valve or system for contamination in the servo valve or friction in the actuator and/or system. By establishing a baseline for a machine while new or newly refurbished, plant managers can monitor performance over time to prevent the next major breakdown.
If a manager does not have someone on staff experienced in developing a preventative maintenance programme, then the manager could contact the plant’s suppliers. Machine component makers often have the know-how and contacts to develop a maintenance programme, which plant managers can then take on.
10. Reduce Servo Valve Sprawl; Have One Model for All Machines
Many companies reduce downtime and lower costs for their machines by reducing the number of servo valve models from different vendors. Some servo valve makers even offer a trade-in programme. The benefits of this approach include:
- Reducing inventory
- Eliminating obsolete valves, which makes repair programmes easier
- Reducing the number of unique model numbers
- Upgrading to the latest technology
- Making it easier to develop an effective stocking programme
With these ten tips and the discipline to stay on a schedule, you will be sure to increase your machine’s life, uptime and profitability.
Steven Beddick is an aftermarket specialist for Moog Industrial Group, a part of Moog Inc. He has nearly 30 years of experience with application engineering support for industries ranging from automotive to power generation. Beddick holds a bachelor’s degree in electrical engineering from Grove City College. Contact him at sbeddick@moog.com.