Securing the flow of goods
High availability and the reliability of rolling stock comprise the basic requirements for modern rail freight. HARTING is researching solutions for condition-based maintenance strategies.
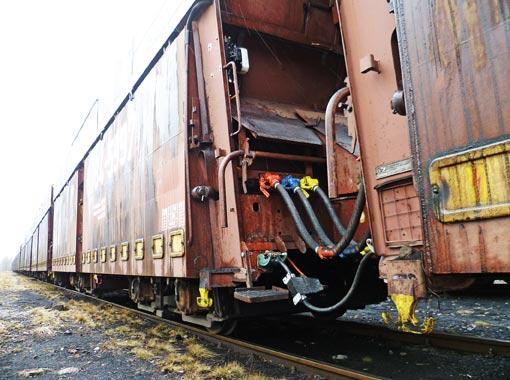
The long history of sustained, strong growth in global trade will lead to continued increases in the flow of goods in the future as well. Despite political advocacy and a broad range of environmental benefits, the share of rail freight transport in the modal split compared to road transport has failed to grow. The lack of availability of rolling stock and associated maintenance costs are particularly regarded as bottlenecks for above-average growth. New strategies and technologies designed to improve efficiency can decisively contribute to an effective increase in capacity.
Under current statutory requirements, freight car maintenance is performed at fixed intervals of six to eight years. This time-based maintenance does not take the condition of components into account, which, as a rule, depends on mileage rather than operational time – an approach that is inadequate for many components.
Several types of damage, e.g. brake wear or the generation of wheel flats, are the result of the operational profile or isolated events and are not detected by mileage-based maintenance. However, wheel flats represent a particularly serious problem in terms of noise pollution caused by rail freight and the potential of associated damage to discs and axle box bearings.
Condition-based maintenance
Significant potential to improve the situation can be exploited by developing condition-based maintenance strategies which centre around the monitoring of relevant components and lifetime predictions derived from such monitoring.
With support from the Federal Ministery of Economics and Technology (BM-Wi) and in conjunction with partners TU Berlin, Eckelmann, PC-Soft, Lenord + Bauer, Vattenfall and Wascosa, HARTING Technology Group has launched the CargoCBM research project with the aim of developing a condition-based maintenance system.
Robust system configuration
The CargoCBM system is divided into the areas of on-vehicle components, stationary components and the user interface. The on-vehicle hardware is tested to IP68 and designed for continuous operation under the most demanding conditions. The heart of the system is the on-board unit (OBU) installed on every freight car. The unit merges the measurement signals from all sensors, performs data pre-processing and contains the on-board communication devices.
In addition, the OBU features CAN bus and ZigBee interfaces that also allow the connection of wireless sensors. In conjunction with several OBUs, the ZigBee modules can serve as wireless train bus. The OBU contains an acceleration sensor that records severe switching impact, in addition to containing a temperature sensor and a GPS receiver. Specially developed combination sensors with integrated A/D converter and CAN module provide rotational speed, acceleration and temperature information from the axle bearings.
M2M-communication between the mobile OBU and the stationary servers takes place via a GSM module. The OBU’s high performance CPU handles the complex calculations used to extract damage characteristics, thus reducing the data transfer volume over the wireless interface during normal operation. In addition, software updates can be loaded to the OBU via this interface.
Automated data analysis
As of the current state of development, damage diagnosis algorithms feature functions for the detection of wheel unroundness, e.g. wheel flats, functions which monitor running dynamics and the associated wear condition of the wheel profile, functions which document severe switching events, and functions which monitor the temperature of axle box bearings.
The system provides information about the current position of the freight car and its mileage. The vibration-based monitoring of the wheel set bearings and the monitoring of brake shoe wear are currently under development. The flexible system design also allows for the implementation of tasks such as the monitoring of brake function, automatic brake testing or cargo monitoring.
Maximum possible customer value is created thanks to the automated analysis of the data that is generated. Data is fed directly into a database on the non-vehicle stationary side and the results are relayed to the zedas® Maintenance Planning Program (ISP) for final evaluation. The software provides all tools for managing maintenance and scheduling processes, which in turn permits both workshop and fleet management.
Successful trials
Since March of 2012, CargoCBM hardware has been in use on several cars at Vattenfall Europe Mining in the Lausitz region. Despite the harsh opencast mining environment, no system-induced downtime has been recorded to date. The functionality and accuracy of the algorithms that have been developed has been confirmed by comparing workshop protocols and measurements taken by stationary systems. In April of 2013, multiple container flat wagons of Wascosa running for the Wiener Lokalbahn between Austria and northern Germany have been equipped with HARTING’s CargoCBM hardware to prove the functionality of the system in autonomous operation on the public railway network.
The CargoCBM system not only enables the reduction of primary costs by optimizing maintenance strategies and improving the safety of rolling stock, it also constitutes the technical basis for entirely new business models that improve the competitiveness of rail freight traffic.