Reliability - What Fails and What Do We Do About It?
Companies in the Oil & Gas industry have been attempting to improve the manufacturing reliability of their operations to improve financial performance by setting up effective Asset Performance Management (APM) strategies. The driver of this has been the potential to realize a 20-25 percent reduction in conversion costs, accompanied by a 15-25 percent increase, in real production capacity, without additional capital investment.
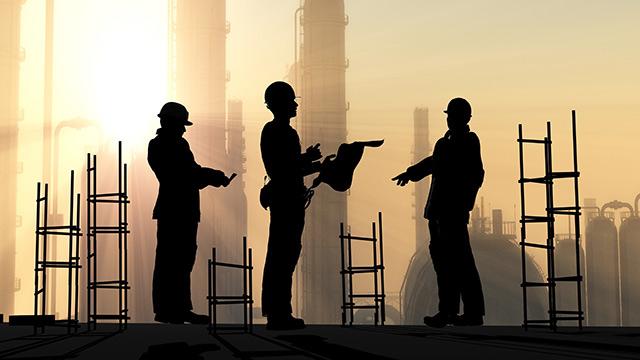
While the prize is large, and pressure on margins is heavy, many efforts made by companies in the Oil & Gas industry to improve their manufacturing reliability through APM will, or already have failed. (See Figure 1. below)
Let’s look at some examples of why these sort of efforts fall short by looking at the following aspects of APM as they relate to Strategy Management and referring to Figure 2.
1. What does Reliability mean?
2. What equipment / component to track?
3. The interactions of behaviour (culture), work processes, and tools.
1. What does Reliable Operation mean?
Does a Maintenance department create or “do” Reliability in your facilities? Wouldn’t that be the same as expecting the Safety Department/HSE to “do safety”?
We need to realize that Reliability of Operations is an output of a system, supported by People (culture!), Processes and Technology (tools!). Just in the same manner safety is.
Tasking a single department to “do reliability” will not lead to success. Achieving Reliable Operations requires at least four of the core business functions to work coherently together, toward the same end goals:
- Engineering
An Engineering Business Function, should be responsible for selecting equipment that maximizes design reliability, and in a joint design process with Production and Maintenance is set up to be designed for maintainability.
This is where the essential initial strategies of run-to-failure (design for maintainability), interval-based maintenance (maintainability/reliability) and condition-based maintenance first need to be planned for. Making access to components made as easy as possible to shorten downtime durations.
The decisions taken during the Engineering phase will linger on for years after decisions are made. Choices for equipment and systems decided on, or specified, during this period can affect upwards of 80 percent of the total lifecycle ownership costs. Only 20-30 percent of this cost can be influenced in later stages of the lifecycle.
- Production
Alongside taking ownership of the required operating procedures for start-up-, produce-, switch-over- and shutdown or equipment and systems, production teams play an important role in the early identification of technical issues, and should be the first line of defence by conducting operator inspections of the equipment they operate, performing daily maintenance tasks (cleaning, lubricating, etc.), and operating within the constraints of the operating specifications of the equipment.
- Maintenance
The role of any maintenance department towards a Reliable Operation is essentially to take ownership of monitoring the condition of equipment. Identified (potential) issues can be processed into actions in an effective and efficient manner to execute work that stops completely, or slows down further degradation of the equipment.
- Procurement and Logistics
The decisions taken to realizing lowest cost of ownership are far more complex than simply choosing the least expensive piece of equipment. It may be that the best mid-long term buy is one that costs most initially but last far longer than a “similar” item provided by another manufacturer. The procurement agent must consider the Total Cost of Ownership over the lifetime of the equipment.
That the procurement agent is familiar with the technical complexity of components is not a reasonable expectation. Interactions need to be close between Engineering and Maintenance to educate and support the procurement department to develop an understanding in evaluating technical proposals.
2. What equipment / component to track?
Most capital projects are focusing on designing systems based on the production processes required. Basically these designs result in a collection of components, organized into individual pieces of equipment, which are then coupled together to form systems.
Seen from the other side this implies that when our assets fail to function, it is caused by components that fail. A compressor does not fail. A bearing in an electrical motor on a compressor may fail. Or perhaps an actuator on a valve in a discharge system may fail.
Traditionally inspections are built up into text heavy “PM’s” defining fixed time-based overhaul or inspections of systems or large assemblies. Results that allow tracking the condition of equipment as it may start deteriorating are either not registered sufficiently, or are not easily retrievable. Information is lost and things will go awry fast.
Our inspections should however be focused on identifying potential problems with components, and tracking progress of deterioration. Using that realization enables us to apply the whole suite of predictive, preventative and corrective actions ranging from inspections during uptime as well as downtime, or inline, real-time monitoring, for parts or even a whole piece of equipment or systems.
Industry 4.0 / Internet of Things may help us in analyzing component failures, or it may drown us, depending on how our processes, and the cultures that drive decision making, are set up.
3. The interactions of behaviour (culture), work processes, and tools
Some of our clients have in the past few years tended to build the focus of their APM improvement efforts on Redefining fields in the system, renaming statuses, or restructuring Master Data. This we can call the SAP-gap, where the ERP is seen as the end-all solution to APM.
This does not change the fundamental premise of moving from the text heavy “PM Workorder” that inspects or overhauls systems or large assemblies.
Strategy Management improvements need to include restructuring inspections to focus on components and with tolerance limits set (process). In the field you need your inspectors to have a common reference for what is acceptable (culture). Inspectors will need a process to report the findings, defining what information to include. You will need to have people consistently executing the process (culture) and knowing how to prioritize the work. All those steps should clever information tools to make them efficient, but could fundamentally also be executed manually as well. A good rule of thumb is, if it wouldn’t work on paper, your IT system will probably not solve it, simply as the organization will fail to comprehend the processes and the information needs to support them.
Setting Your Strategies May Require a Restart
To be successful we need to have people executing the right actions, in the right way. Whether we equip them with a 10 Euro-tool from the nearby discount store, or a 50,000 Euro-tool, is irrelevant until they have the ability and skills to productively apply the tool in the first place in an appropriate fashion.
The basic “what” is simple:
- Define your work processes and create your training and SOP’s to define behaviours. Set your tools up to support your work processes, and coach your organization heavily. Make sure that the core functions of the organization all play their part in inspections, and are providing their aspects of reliability to the operations
- Organize your inspections to track components, know their condition, effectively prepare your work instructions, and schedule for effectiveness. Track what you did, and restart the circle.
The “how” is not.
Realizing that there are many more pitfalls to pay attention to, we will need to park those items for another time. At last it may however be worthwhile to touch on how important it is to be open to taking a step back, looking at the big picture, and openly asking: “Does what we have make sense?”
The reluctance to be honest with ourselves and our coworkers tend to derail improvement initiatives and sometimes become a devastating fungus in a company’s culture.
Appreciating that companies, or rather the individuals making up the company, want to pursue success in life. It is always frustrating to see people being pushed into Ponzi-like schemes to satisfy the end of the week, end of the month, end of the quarter cheat-sheets related to the personal appraisal structure to drive one’s career.
Issues in the company’s processes get chopped up in ever smaller pieces, cleaned up and stuffed with irrational arguments to make it palatable as a ”personal achievement” on the “tick-box-list”.
And “success” is then rewarded based on having the box ticked whether or not it has done something to the bottom-line of the business on the long term. And because such “achievement” is personal, they obviously become a point of personal interest for the individual in question to safeguard them for critique even when there is proof that it makes no sense at all.
In the end, such behavior becomes a root cause for “broken business processes” and forms artifacts in the culture making change harder than necessary.
Not surprisingly most of those “achievements” are coined as “improvements” and “innovations” and often relate to the themes like the “SAP gap” or other nice-to-have tools and gadgets. Why? Because that is sexy. It is not perceived as “sexy” to achieve an almost perfect schedule compliance at the end of the day or the end of the week. That’s ordinary “work” and tends to be taken for granted in the meeting rooms of the management echelons.
It requires determination and full support from top- and senior management to drive the required behaviors into the right direction.
This then adds one extra point to the to-do list:
- Make a point of doing the right work at the right time with the right people under the right conditions. Change perceptions and make success of managing work on a daily, weekly, monthly quarterly a “sexy” thing to do!! Because in the end, growing our business accounts is one-on-one related to our ability to reliably deliver quality products and services to our customers in a sustainable manner!
Benefits of successfully implementing Asset Performance Management (APM) strategies:
1. Increased availability of production systems, and reliability - knowing they will run when required.
2. Fewer failures of production systems and equipment
3. Lower costs for system and equipment maintenance, spare parts inventory, and capital replacement.
4. Improved product quality associated with a reduction in costs related to losing or reprocessing products
5. Higher profits to put in the bank, due to the compound effect of reduced conversion costs through factors above.
6. Additional real capacity as operating units are able to operate at higher yield levels for sustained periods without excessive failure rates.
7. Enhanced morale amongst management, craftspeople, and other employees as they learn to enjoy a proactive environment instead of surviving in chaos.
8. A continuously learning enterprise resulting from accurate analysis of equipment maintenance, repair, and replacement records.