Outsourcing of Reliability or Maintenance
"IDCON - Should you Outsource Maintenance"
Outsourcing is a way to change operational processes. Care must be taken to secure that required quality and reliability levels will be met under new circumstances. Part 2/2 will be released in MaintWorld 3/2014.
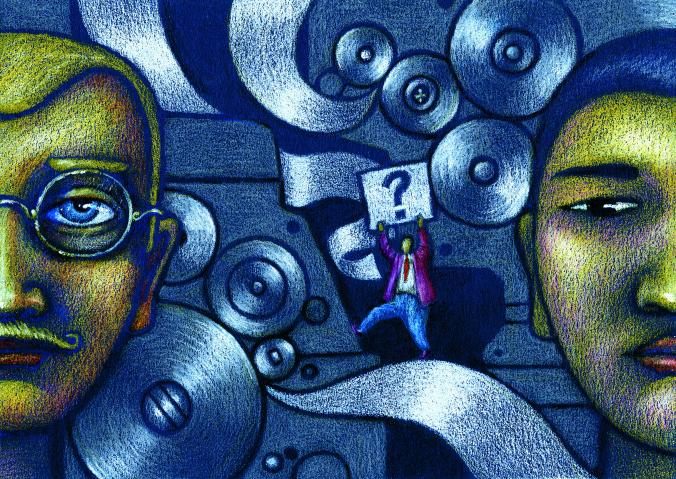
THERE ARE many levels of outsourcing maintenance work. The most common include:
- Outsourcing of the whole maintenance function. This is often done by forming a separate maintenance company. This company will provide reliability and/or services to the manufacturing organization.
- Outsourcing of work done during scheduled shutdowns and outages. This is very common in the pulp and paper industry. It is not cost effective to not bring in extra resources during peak loads.
- Outsourcing of special skills. Special skills that are not often used in your maintenance organization can be good to outsource, as it is otherwise difficult to keep up with new technology and maintain skills. A maintenance organization with fewer than 1,500 bearings in their vibration analyses programme can be an example of where outsourcing of this work can be cost effective.
- Outsourcing of equipment or a system function. Some companies offer to sell a guaranteed function at a fixed cost including operations and maintenance. Guarantee includes reliability performance. An example is pumps, compressors and mobile equipment. The difficulty here is that many problems are induced by abusive operations practices. This can make it difficult and time consuming to decide who will pay for these incidents.
- Outsourcing of spare parts store. You could sell your store and outsource this service to a company specializing in this area.
There are more levels, but these are the most common I have experienced.
Why outsource?
The reasons for outsourcing are many. Suppliers of outsourcing services promise lower costs and better reliability, often in that order. In my opinion, a contract should be based on guaranteed reliability and lower costs. Of course, there are many successful examples on the outsourcing of maintenance and it can be a good choice for many organizations.
If you consider outsourcing, you should always ask yourself why a contractor could deliver lower costs and better reliability than you can with your own organization. The provider will most probably argue that they can implement better reliability and maintenance processes. This might very well be true but they must also make a profit on top of that and you have to ask yourself why you do not have the leadership in place to do that yourself.
There are many examples where outsourcing was done as an “Act of desperation”. Often unions and management have been at gridlock, the final solution of which being outsourcing, and that has many times lead to real change and improvements.
A contributing reason can be that if you outsource, the fixed cost you had before outsourcing is now a variable cost even if it seldom varies much.
Outsourcing of maintenance.
Often, we only talk about the outsourcing of maintenance without much emphasis on reliability incentives. Outsourcing contracts based on the outsourcing of the whole maintenance function often focus too much on reducing the cost of maintenance instead of the results derived from improved maintenance performance.
The sales argument is often heavy on the cost savings you can achieve. The suppliers then have to set up better work management systems and most probably also provide lower total costs for labour and management. In today’s shortage of skilled craftspeople this is a very difficult situation. A paper mill reported that their contractor had electricians staying an average of only 18 months, then they left to a better paying job. This caused many problems for both the paper mill and the contractor.
Outsourcing of reliability.
Reliability is here measured as the percentage of Quality performance x the percentage of Time Performance x the percentage of Speed Performance. This is the most common way to measure reliability on a paper machine.
- Quality performance is the most important and is measured as the percentage of Saleable Quality paper made divided by total amount of paper made.
- Time performance, often called Availability, is often measured as percentage time “Sheet on reel” divided by available hours over the same period of time. (During a year that is 8760 hours or 8784 hours if it is during a leap year).
- Speed performance is a moving target and is set per grade of paper made. It is measured as percentage speed divided by set speed performance for that grade.
If an outsourcing contract is based on reliability the whole scenario will change.
In this scenario, the focus will be on delivering results with a focus on reliability improvements followed by lower costs about two years later. When entering into the first year or two of a reliability-based outsourcing contract, maintenance costs are very likely to go up before they start declining in the second or third year. Reliability will improve before that.