Most Common Myths about Accelerometers and Frequency Range
In this article I will talk about the frequency range of accelerometers and about common mistakes in understanding them.
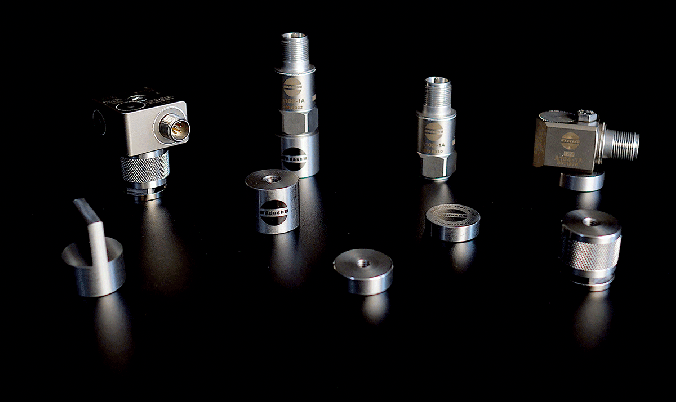
The most common accelerometer has 100 mV/g sensitivity. The frequency range declared by its producer is: 0.5 Hz - 15 kHz, with plus minus 3 dB bias.
Many people think that +/- 3 dB is not too much, that it is something around +/- 3 percent. But this is not true.
The +/- 3 dB is much, much more. Minus 3 dB is minus 30 percent, plus 3 dB is plus 40 percent. But the frequency range is not the primary subject of this topic.
Let's suppose that the response function is flat. Most of the users want a very low frequency limit. They say: “I have to measure a slow speed machine, my machine speed is only 30 rpm, I need to measure 0.5 Hertz.”
If I ask them why, they do not answer, because they do not understand the question. Let me give you an example: If I want to measure the acceleration on low frequency, what acceleration level can I expect? Would it be for example 1g?
Most of the people are not able to imagine the vibration acceleration and velocity. Everybody can imagine the displacement. When you say that a machine vibrates +/- 3 mm, then everybody understands.
So, we can use this formula for conversion of acceleration to displacement and displacement to acceleration:
acc [m/s2] = disp [m] * (2 × π × speed [Hz])2
Using this simple math, we can convert 1 g to meters. If the speed is 30 rpm it means 0.5 Hz. (Do not forget to convert g to m/s2 firstly.) The corresponding displacement level is 1 m. Not one millimetre, but one meter. No machine could work with such a vibration level. The corresponding velocity level is
3,200 mm/s, it is 125 ips, impossible... Now I suppose the displacement level is 1 mm. The corresponding acceleration level is 0.01 m/s2. It is 0.001 g.
If the sensor sensitivity is 100 mV/g, then the voltage for 0.001 g is 0.1 mV.
It is not too much. Can you measure such a voltage level?
The answer is NO, because the usual sensor noise level in the field is from
0.2 to 0.4 mV. With such noise it is very difficult to measure the 0.1 mV because it is lower than the noise level. But let's go back to the basic question. Why measure the amplitude on 0.5 Hz?
Another answer is: “I would need it when I would want to balance the machine or investigate the looseness or misalignment.”
Yes, in these cases I need to measure the level on speed frequency, but I do not know who really wants to do it. When the speed is so low, then you should have the unbalanced mass tens of kilograms to increase the vibrational level. The centrifugal force depends on the square of the speed. At 30 rpm it will be very low.
But the users say: “No! I do not want to balance, I want to measure the condition of the roller bearing.”
And this is the key point.
For such measurement I do not need the low frequency.
When the bearing balls are passing scratches or it goes through bearing pitting if you wish, on inner and outer races, then the shocks appear in time signal.
The natural frequencies of shocks are very high. Typically, between 500 Hz and 25 kHz. We do not need to measure low frequencies; we need to measure these very high frequencies. And this is not easy for low speed bearings (machines). We need high resolution of the signal (high sampling frequency) and at the same time we need a long-time signal, because the time interval between shocks is very wide. So, the whole measurement is extremely demanding on data processing and data storage. ADASH has therefore developed and put into use the ACMT measuring method for low speed bearing analysis, which through smart compression solves the mentioned problems and keep most of the information in the signal.
The next most common misunderstandings are bearing fault frequencies. They can be very low for slow speed machines and users again use the wrong rule. They say that the accelerometer has to be able to measure the frequencies. This is wrong. The fault frequency is the repeating frequency of shocks, it is not pure sine frequency which should be captured by a sensor.
We need to measure the natural frequencies of shocks. And they are again higher than 500 Hertz.
In Figure 2 we measured the spectrum in a 25 Hz range only. The repeating frequency of shocks for this bearing is around 1 Hz. You see nothing around 1 Hz.
If I want to see the repeating frequencies in spectrum, then I must apply the demodulation. It means, I must add the energy. Demodulated spectrum can display something visible. The demodulation spectrum uses the time signal which is enveloped. We want to measure only in the band from 500 Hz to 25 kHz. We are not interested in low frequencies.
You can imagine the enveloping like simple electrical circuit: the shock comes and charges the capacitor and then the capacitor is discharged through the resistor. Discharging is much longer than the length of the original shock.
This is the additional energy which helps us in spectrum. And it really helped.
In the third picture you can see the repeating frequency 0.85 Hz and its harmonics. The harmonics always occur because the enveloped signal is distorted. It is not pure sine-wave which can display only one line in spectrum.
I hope you will remember this article when you face measurement on low speed machines and hope you will now be able to check these machines more efficiently.