Managing the Crisis Effectively: How to Develop a Successful Asset Management Strategy During the Coronavirus Downturn
COVID-19 is disrupting all sectors including the process industry – plants around the world are operating in emergency mode or are shut down completely.
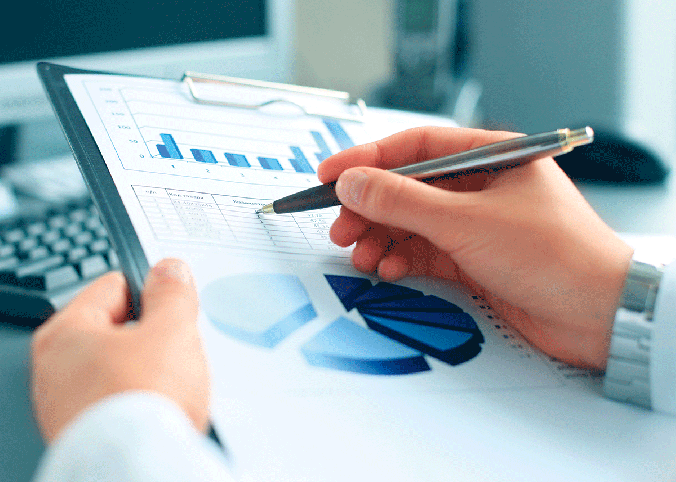
There is no hint about how long the situation will last nor can anyone realistically predict the scope of the economic impact it will have. Therefore, it is crucial to minimize costs while not compromising the effectiveness of the plants.
The "bull market" has collapsed. For eleven years, stock market prices knew only one direction: up. COVID-19 suddenly put an end to the seemingly eternal upward trend. A global recession seems inevitable. The only question that no one can seriously answer now is: Which development will the recession take? Economists distinguish between so-called "V", "L" or "U" movements depending on the curve shape. Within a few days, companies had to drastically limit their supply capacities. Airlines, travel agencies, hotels, car manufacturers, suppliers – all sectors are increasingly affected.
But what does the dramatic situation mean for asset management in the process industry? Currently, the maintenance community is no longer concerned with optimizing availability. Instead, those involved are fighting to cut costs without jeopardizing the reliability and safety of the assets. In order to make this balancing act – and thus the crisis – as successful as possible, clear and unambiguous leadership is required. But what does good crisis management look like during these times when COVID-19 is dictating all aspects of human activity? We present six recommendations to help you optimize your asset management decisions during this unprecedented time and to emerge from the COVID-19 slowdown unscathed and ready when business returns.
1. Advance planned plant shutdowns (turnarounds, cleaning, etc.)
Prepare your organization for earlier, legally or technically required plant shutdowns that were originally scheduled for late 2020 or 2021. Above all, check whether the necessary requirements are met. In other words, enough staff must be available both at your ser-vice providers and in your own company as soon as the current lockdown ends. If we have learned one thing from the 2008/2009 financial crisis, it is that the global economy will need around two years to fully recover from a shock of this magnitude. Conversely, demand and product prices will drop significantly over the next few months. The advantage: This also applies to almost all service and material costs. Use this “window of opportunity” wisely.
2. Avoid random budget cuts
We all know that maintenance must help reduce costs in times of tight budgets. How-ever, if you reduce your maintenance costs across the board, you will feel the effects more clearly in a year or two – exactly in the period when the economy – presumably – is slowly picking up speed again. For you, this would mean that if the demand on the market picked up again, you would not be able to deliver the required plant availability that is in demand. So, check very carefully and systematically where you can reduce your costs with the least possible risk so as not to accidentally cause long-term competitive disadvantages.
3. Reduce plant downtime (TA Scope) to a maximum
Turnaround (TA) work packages related to expansive capital investments should be challenged immediately. However, all work packages that serve cost-effective production should remain in the TA-Scope. Investments that don’t reduce cost in the near-term should be delayed until the economic forecasts look brighter. The same analysis should be applied to work packages that exceed the legally required examinations. So, minimize your TA-Scope as much as possible. Due to probable resource bottlenecks, it may be more cost-effective to run two small Turnarounds, rather than one big, complex one.
4. Maximize precision in maintenance and inspection work
Nothing increases Mean Time Between Failures more than the consistent monitoring of wear and tear, the main cause of most system failures. If assets are bucking, make noises, become hot or dirty, they will not last as long as their quiet, cool and clean counterparts. Let your plant operators know the optimal reference conditions for fasteners, lubrication, alignment and balance, and improve communication between production and maintenance.
5. PdM optimization and system troubleshooting
Almost every company that we have worked for in the past 25 years routinely performs PdM (Predictive Maintenance) work that is inefficient. Optimize all maintenance and inspection plans that have a high proportion of corrective costs despite defined PdM measures. Because the expected level of production is likely to be relatively low in the next few months, you should take the opportunity to carry out a root cause analysis of your major system failures ('bad actors'). Bad actors all too often fly under the radar but are responsible for a high proportion of unplanned maintenance and excessive maintenance cost. These are malfunctions which, although they do not have a great impact on the availability of the system, can (as a whole) cause high costs. Your operators and engineers can also easily carry out a bad actor analysis and the associated PdM optimization from the home office. Use the current situation and available time capacities to significantly reduce disruption costs in the future.
6. Adjust maintenance measures to market demand
The lower market demand will lead to a decrease in production volume. For maintenance, this means switching from an availability-driven strategy to a cost-oriented strategy. Therefore, evaluate all maintenance measures regarding their contribution to availability and the associated maintenance effort. Check all static maintenance strategies according to the new availability conditions and delete, stretch or postpone as many measures as possible without unnecessarily increasing the risk of failure beyond the desired availability level or violating legal provisions. Convert your maintenance to a 'demand driven maintenance model'. However, remember that maintenance and reliability function “out of phase.” If an investment today produces improved reliability two years from now. A cutback today results in reduced reliability during the same time period. Make sure that your reliability investments synchronize with the timing of market demand.
Conclusion
The Coronavirus crisis requires a cost-centered asset management strategy. For many plant operators, this will be a shift of their strategy by 180 degrees. To ensure that this process is as successful as possible, we have shown you the crucial areas of action.
The most important advice is hidden under point 2, since it directly affects all other aspects. It is essential to avoid reflex (panic) reactions to arbitrary cost cuts. Otherwise, careless short-circuiting operations jeopardize the ability to reliably run your systems at full load again when demand returns, which it invariably will. Be stringent and, above all, very methodical to utilize the time your employees spend in the home office to complete or optimize your asset management strategies. This is how you can turn the crisis into an opportunity.