How predictive maintenance enhances plant safety without sacrificing productivity
An effective predictive maintenance strategy leverages technology and analytic data to allow for optimized scheduling of corrective maintenance tasks. The goals of these programs are to reduce asset downtime, prevent unexpected failures, promote productivity and increase the safety of personnel.
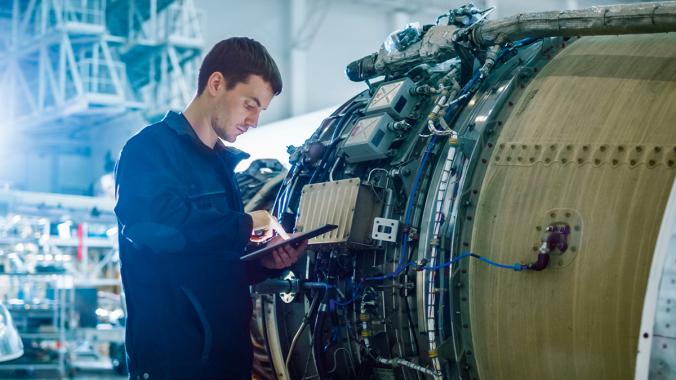
In the past, safety investments often meant a reduction in overall productivity or an increase in cost structure. However, modern technology has created new opportunities for facility managers to maintain or even increase productivity levels as the plant implements new safety protocols.
How maintenance impacts facility safety
Maintenance work can be dangerous, especially when assets fail in unexpected or catastrophic ways. In fact, a report from BLR (Business & Legal Resources) revealed that between 25 and 30 percent of workplace deaths in the manufacturing industry are related to maintenance activities. Shocks, burns and injury from moving parts are all common causes of fatal accidents.
A predictive maintenance strategy seeks to reduce or completely eliminate unexpected failures. Using technology such as ultrasound sensors, stakeholders can detect minute changes in sonic output to determine when an asset is likely to malfunction. Given enough data, stakeholders can determine expected life spans for all
facility assets and build a maintenance schedule around this information. This way, maintenance personnel can power down assets during a period that is not likely to interfere with the facility’s productivity goals. They can complete maintenance work well before an asset begins to behave erratically, reducing the risk of severe injury.
Combined with safety training and other fail-safes, a predictive maintenance program gives facility managers the ability to mitigate risk with precision.
Predictive maintenance can improve asset uptime without sacrificing safety.
Why predictive solutions optimize risk management
Reactive maintenance programs carry a lot of financial risk. According to the International Society of Automation, manufacturers across all industries lose approximately $647 billion annually to asset downtime, thereby losing out on a corresponding $13 trillion in production value. To put those numbers in context, ISA explained that the average cement mill loses roughly $7 million per year in lost production.
Traditionally, matters of financial risk and safety risks have been a balancing act. More safety measures often meant fewer resources available for production. Predictive maintenance changes this paradigm significantly. In a predictive scheme, both productivity and safety increase with the strategic scheduling of maintenance tasks. The program not only allows maintenance staff to know when an asset is likely to fail, but also specifically how the asset is likely to deteriorate. Combined, this knowledge gives stakeholders an unprecedented strategic advantage.
At the end of the day, safety issues and maintenance issues stem from the same problem: a lack of planning and analysis. Both types of risk are much easier to manage when stakeholders have the resources to plan for contingencies and eliminate the potential for risk before it manifests in a workplace accident.
How technology improves safety and productivity
An effective predictive maintenance strategy begins with good data. According to Control Engineering, this data can come from multiple sources, such as thermal readings and remote ultrasound sensors. The more performance indicators a facility manager has to work with, the more optimized the maintenance strategy.
For example, say a facility manager knows one of his or her assets enters a fail state approximately every six months. The manager could schedule maintenance every five months to prevent failure. A smarter approach might be to place sensors along the moving parts of the asset and continually monitor decibel readings for changes. These sensors can show maintenance staff exactly which part of the asset is beginning to fail, so they can take targeted action in a timely manner. Over the years, the system would improve continually as stakeholders understand exactly when and how an asset needs to be serviced for optimal performance.
Predictive maintenance requires forethought, strategy and intelligent technology investments.