Forces of Change How the maintenance team can thrive and grow during a time of disruption
The world has seen much change in 2020. The COVID-19 pandemic has brought many countries of the world to their knees as we are experiencing one of the most disruptive events in memory.
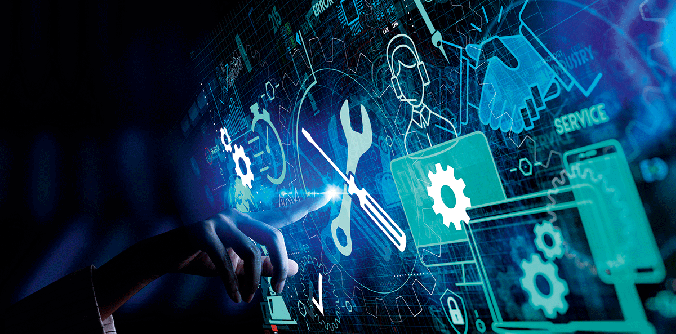
At the time of this writing, the terrible toll of the coronavirus pandemic on the US economy has continued unabated bringing the total of unemployed to more than 36 million. Fortunately, the latest figures from the labor department show the rate of unemployment claims are slowing, meanwhile many states and municipalities around the US are reopening their businesses.
As a result of the pandemic, the US Government and the CDC have recommended that citizens adopt new ways of interacting and working going forward. Recommendations include things like social distancing, wearing personal protection equipment (PPE), and frequent hand washing, to name a few. These changes are becoming a way of life.
This disruption caused by the COVID 19 virus is forcing change in all areas of society including organizations and businesses around the world. Organizations adjust to small changes all the time, possibly looking to improve productivity, responding to a new regulation, hiring a new employee, or something similar. The disruption caused by the COVID-19 is causing change on a massive scale.
Some call this a driving force of change. Forces of change manifest themselves two ways, internally and externally. The COVID-19 virus is considered an external force of change. External forces of change can be more relentless in forcing change. In some instances, an organization or business must change or go out of business and cease to exist.
So how do “forces of change” work? In Kurt Lewin's model there are forces driving change and forces restraining it. Where there is equilibrium between the two sets of forces there will be no change. In order for change to occur, the driving force must exceed the restraining force. See Lewin’s model below.
The COVID 19 disruption has presented many companies with a grim reality: adapt, improvise, and implement new ways of working or cease to exist.
Although COVID-19 has brought tremendous sorrow and loss of lives and livelihoods, some suggest that the driving force of change such as the disruptive COVID-19 virus can be harnessed and turned into something positive or constructive. With that in mind, it might be possible to capitalize on this current force of change and make some good things happen from it.
Below I am going to list 5 things that many maintenance teams can begin doing now to add value while preparing them for the future.
1. Master the Virtual Meeting: virtual meetings are becoming an indispensable way of doing business in this current business climate. Stay at home workers are becoming the norm as a result of social distancing requirements brought on by the pandemic.
- Organizations reluctant to adopt virtual meetings will now be forced to do so. Going forward, working from home will not only be acceptable but encouraged. To be successful, the maintenance team should do the following:
- Standardize virtual meeting software and learn how to use it.
- Ensure it’s compatible with smart phones as well as PCs.
- Make attendance and participation as easy as possible to ensure maximum participation.
- Use the camera! It’s important to see faces in the meeting as this helps understand and monitor engagement.
- Respect the time - start on time and finish on time.
- Engage and communicate with team members. This will be the way of connecting and communicating going forward.
2. Communicate with Internal and External Suppliers and Customers: Primarily, we will be concerned with our internal suppliers and customers (or partners as we often call them) e.g. the production team, the storeroom, engineering, vendors, and contractors. As our businesses are disrupted by the repercussions of the virus it’s important to communicate. We will have less face time with our partners at the plant and within the organization.
- The maintenance team must keep their suppliers and customers up to date on what’s changed and what’s not changed. Information that needs to be communicated:
- Equipment repair updates
- Maintenance schedule changes and updates
- Shutdown and outage timing
- Equipment problems
- Employee changes or absences
- Business priority changes
- Production line changes
All of the maintenance process partners, vendors and suppliers will be affected by the disruptions. Continuous communication will be absolutely essential to keep them informed. Consider a weekly e-newsletter sent out to key partners and external suppliers as well as phone calls and virtual meetings.
3. Empower your team - I’ve heard people talk about this for years and yet they only give it a half-hearted effort. Now is the time to make it happen and the reason is obvious – business survival. Empowerment is the process of enabling or authorizing an individual to think, behave, and take action, and control work and decision-making about their job in autonomous, independent, self-directed ways.
- Current conditions have made this essential. Here are some things you can do to empower your team:
- State what you need – be clear with team members about the new responsibilities, what’s required and expected. State it in measurable terms and be prepared to follow up and adjust.
- Release control - remove barriers that limit the ability of staff to act in empowered ways.
- Measure – Establish metrics that measure the team’s output. Review them with the team and let the metrics speak for themselves.
4. Employ game-changing maintenance strategies - For years you had several initiatives that you’ve needed to implement. All of these were designed to improve efficiency and effectiveness of the organization. A lot of things have held you back including a strong enough business case that would involve management support. Here some ideas to move forward:
- Identify time-based PM tasks that can easily be transferred to condition monitoring. This should be based on ease and cost of implementation. Consider using a vendor or outside resource. Allow them to manage the program while providing metrics, updates and action plans.
- Engage the operators! You’ve discussed it for years, now is the time. Studies have shown that a well-trained operator can prevent up to 75 percent of all impending failures. Benchmarking studies have confirmed at least 25 percent of plant operators' time can be utilized for carrying out certain types of maintenance work. Four operators doing frontline maintenance equate to one fulltime equivalent maintenance technician. This allows maintenance to employ the maintenance techs in more technical and value-added activities.
- Outsource some of the projects that can be done remotely such as procedure review and updating, PM reviews and updates, CMMS master data updates and builds, BOM development, and business process documentation, mapping and updating to name a few.
5. Invest in people - At this time, your people will be worried about their jobs and their futures. Leadership will need to communicate clearly and regularly what steps they are taking to secure their employees and keep them safe.
Some organizations are experiencing a shortage of workers. It’s therefore possible the maintenance team may not have the required skills to support it. This would be a good time to accelerate upskilling to cover these gaps in the team that are critical or will be when the crisis subsides, and the plant begins expanding. Some things to consider:
- Virtual training
- Online computer-based training
- Virtual coaching and mentoring
- On the job training led by staff or senior technicians
Many say change is inevitable and that may be true. Unfortunately, most are never ready or prepared for it. Change can be disruptive and at times brings with it fear, pain, and suffering. Today’s challenge is to face it and resolve to make something positive out of it.