Failures and diagnostics of asynchronous motors
Asynchronous motors are the most common type of motors used. They are known for their advantages such as low purchase price, high efficiency, easy regulation and simple but robust construction.
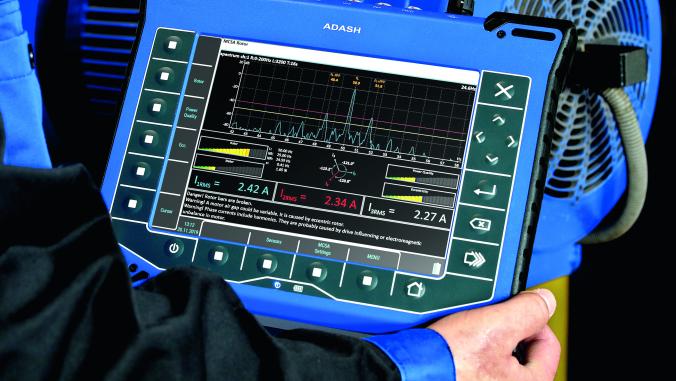
Despite their high reliability Asynchronous motors suffer from some malfunctions of machine parts. We can divide failures in an asynchronous motor into failures of mechanical and electrical origin, and also on stator, rotor and bearing failures.
Stator faults
Stator winding faults are majority problems of stators. The most common source of faults due to the winding is broken isolation. Thermal stress has the greatest impact on the life and quality of isolation. Another undesirable effect is the electrical stress of the transient voltage. In the case of more and more frequent use of inverters for soft-start, rectangular voltage pulses are modulated at the output of the inverter.
Rotor faults
The rotor of an asynchronous motor consists of a shaft, insulated sheets pressed on the shaft that form the rotor magnetic circuit and windings. Mostly the winding of the rotor consists of a cage structure, which is formed by bars, which are connected at the ends.
Rotor eccentricity (unevenness of the distance between the rotor and the stator) is the most common fault, followed by rotors bars interruption. The cause of these faults can be the use of poor quality materials, overloading or heavy starts. In the case of rotor bars, the fault may increase the resistance of the bar, or completely break the bar electrical circuit. Rotor bars failures result mainly in engine starting deterioration and generating parasitic moments. Also the broken bar causes additional faults in others bars, because the current in them is bigger due to missing bar (the broken one) current path.
Bearings faults
All parts of the bearing are subject to degradation. The cause of bearing failures can be considered as mechanical stress during rotational movement and bearing currents. Mechanical stress can be caused by poor: installation, assembling, or using and maintaining. The bearing currents can be caused by induction (due to asymmetric electrical circuit or power supply) and by frequent voltage changes (caused by power supply from semiconductor converters).
Bearings faults detection is almost cover by vibration analysis. All mechanical (and some electrical) faults have unique signature in vibration spectrum of machine and vibration analysis can recognize them.
Electrical (and some mechanical) motor faults have unique signature in frequency spectrum of motor current. And the MCSA method can recognize them. The MCSA abbreviation means: Motor Current Signature Analysis.
In motors with faults, excessive sidebands are created, which distort the frequency spectrum. Each fault then has its specific signature. Individual defects can be distinguished from each other according to the amplitude bands and the frequency.
The basis of this method is to measure the course of the stator current of one or more phases in the time domain (with sufficient resolution) and its subsequent spectral analysis.
The ADASH VA5Pro vibration analyzer offers unique possibility of analyzing vibration and current in one device. The MCSA module allows you to do analysis of current signature from the spectrum - based on your knowledge and experiences. Or you can use automatic detection function. It is the similar idea as ADASH automatic Fault Source Identification Tool (FASIT) for vibration analysis. The device can automatically recognize the main causes of failures as unbalance, looseness, misalignment and bearing faults. The MCSA module of the VA5Pro device is able to automatically identify rotor and stator faults, eccentricity and power quality.
Before the Adash
THE ADASH founders, Adam Bojko and Radomir Sglunda first met at the Physical-Technical Testing Institute in Ostrava in the late 1980s.
THEIR FIRST JOBS were related to seismic measurements in coal mines. That was the first experience of using a vibration analyser, which supporting written materials referred to “rotating machinery analysis”.
Further studies of this topic led to various side jobs such as modal analysis, operating deflection shapes, on-site balancing, vibration analysis etc. while still working as government employees.