Facility Managers: How to Benchmark your Mechanical Assets
Failed assets can quickly ruin your day. As any facility manager can attest, an asset that fails unexpectedly takes time and money away from the business. With the right tools and methods, however, any maintenance team can detect and solve problems within mechanical assets before they break. Here's how benchmarking and ultrasonic technology can improve how your facility prevents asset failure.
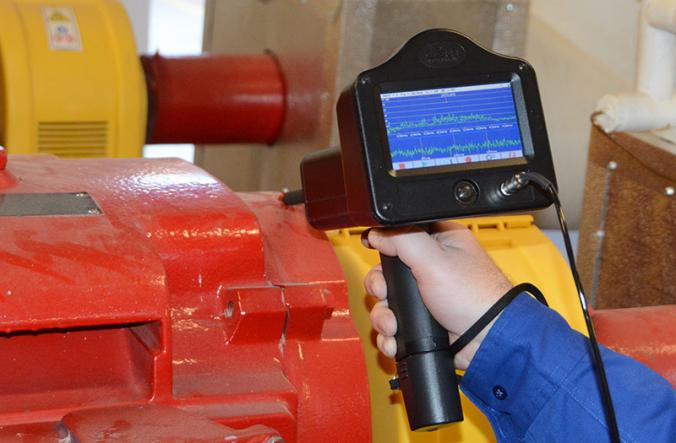
Having a standard by which to judge your mechanical assets enables you to create a condition monitoring system that optimizes your facility's productivity and efficiency. When developing a maintenance schedule for your facility's mechanical assets, you may choose to set your own benchmarks, or use industry standards. If you want your assets to be the best of the best, defining your own benchmarks may be a good option, as this will allow you to make process modifications and check the outcomes against your previous data.
Benchmarking and monitoring your mechanical assets has a number of benefits, including cost saving, productivity optimization and reduced downtime. When an asset fails completely, it can wreak havoc on your entire facility. Downtime not only means lost productivity, but also increased costs. At the same time, an overactive preventative maintenance schedule can be likewise detrimental to your budget. For example, if your maintenance teams spend hours every week running diagnostics on mechanical assets, but only finds an issue once every few months, you could be spending more than you need to.
By recording benchmarks for each of your assets and monitoring key performance indicators, you enable your maintenance team to make informed decisions about which assets should be inspected at a certain time. And there are a number of ways you can formulate that schedule, depending on the asset in question. For example, you could check KPIs every time a vital asset is in use, or you could perform a manual inspection at regular intervals.
Ultimately, it all comes down to the kind of data that is available to your team. If your maintenance staff only relies on visual information to detect an impending breakdown, there is a good chance your condition-based maintenance strategy will not perform very well. An effective condition monitoring plan should have a solid foundation of reliable data. But how do you collect it? First, you will need the right monitoring equipment. Then, you will need to establish benchmarks for future use.
How Ultrasound Technology Provides Actionable Insights
Facilities with lots of mechanical assets tend to be noisy. An asset could be shrieking its last warning, but the human ear may not be able to hear it. And when you want to find problems early, you need a solution that can detect early warning signs. If your team is able to discover and repair small problems before they become big issues, your facility will save time and money.
Continuous Monitoring
To detect impending mechanical failures, you can rely on ultrasonic monitoring technology to give you an advanced warning. Let's say you purchase a new asset and monitor its work for a week to develop a benchmark. Then, at some point in the future, the asset begins to underperform, relative to that standard. A remote ultrasonic sensor such as the Ultra-Trak 750 will detect anomalies based on pre-set thresholds and warn your staff when something goes awry. The UltraTrak 750 is a permanent sensor that can provide benchmarking information on a remote continuous basis, and the data can be sent directly to PLC’s for alarms, or any other platform where 4 to 20-milliamp information can be sent.
Another solution for continuous monitoring is the 4Cast, used in conjunction with permanently mounted Remote Access Sensors (RAS). The 4Cast will also monitor your assets 24/7 by getting decibel readings from the sensors and send them via an Ethernet connection to a data management software (DMS), where alarms can be setup based on the benchmarking data. The 4Cast can also record sound files from the assets, which can be later analysed in a spectrum analysis software like Spectralyzer. Due to its online connection, the 4Cast is a very adequate tool to closely monitor critical assets.
Hand Held Ultrasonic Instruments
Likewise, a hand held instrument as the Ultraprobe 15000 gives maintenance staff the power to hear and detect minute changes in asset performance so that they can make informed decisions about how best to maintain those assets. This instrument allows technicians to read and manipulate data in-device, or transfer the data to a computer for further use.
Also, we should note how important it is to benchmark the lubrication of new motors and rotating equipment, since lubrication issues are one of the major causes for bearing failure. An instrument like the Ultraprobe 401 Digital Grease Caddy can also play an important role in optimizing lubrication PM’s on both the amount of grease that needs to be added and the frequency or how often the equipment is being lubricated.
Conclusion
Benchmarks and KPIs are necessary for any condition monitoring system, and they need to rely on accurate, trustworthy data. Ultrasonic technology can provide the highly granular data your team needs to stay one step ahead of asset failures. A combination of remote sensors and personal devices will give your team the competitive edge.