Condition Based Maintenance in the Paper Industry
A Paper mill had entailed excessive unplanned production downtimes. The condition-based maintenance plan was designed and implemented in several phases.
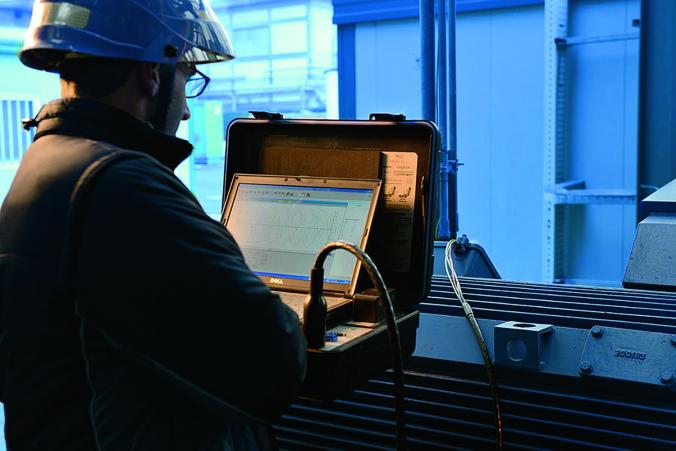
SCA HYGIENE Products, a division of the Swedish multinational SCA, has four facilities in Italy. The Collodi site (in the province of Pistoia, in the region of Tuscany) is recognized as one of the leading European producers of coloured tissue reels for table napkins, toilet rolls, handkerchiefs, facial tissue and kitchen towels. It has a production of 38,000 tons per year, a portion of which is converted by the SCA group and the rest sold to customers not just in Europe. Two Recard Crescent Former PMs are installed at the facilities, with relative rewinders.
ISE, Industrial Service Engineering, is an engineering company that supplies maintenance services and solutions. It has customers both in Italy and abroad and develops and integrates specific solutions that allow customers to reduce operational risks connected to systems operation, to optimize maintenance organization and works as a maintenance partner for outsourcing predictive and diagnostic maintenance. Through its product division, ISE also proposes avant-garde diagnostic systems and instruments thanks to partnerships with international companies working in the field of Condition Monitoring.
For those employees in charge of maintenance, it is not always easy to direct their choices towards one strategy rather than another. Some criteria for choice making comes from the UNI norms, but it often happens that identical machines operating in different contexts require different maintenance strategies and policies. Furthermore, the strategy adopted must be effective and efficient and must take into consideration the constraints that maintenance personnel often face. It is therefore necessary that, starting with the maintenance project phase, specific instruments be supplied that support the decisions made, in order to obtain objective indications on the results expected by the policy adopted.
Maintenance management: the predictive solution
Within the SCA Hygiene Products group, as in the rest of today’s modern production industry, maintenance is of course a determining factor in the complex performance of the production system. In these last few years, numerous problems on the machines and system components has entailed excessive unplanned production downtimes at the SCA Hygiene Products facilities in Collodi. This, in turn, has had a substantial influence on lost revenue and on management costs. For this reason, it became fundamental to establish a correct maintenance strategy, implementing it through the use of the most appropriate processes and technologies available today.
Presently, maintenance management consists in defining, for each system and relative components, the most appropriate maintenance policy, choosing among the different ones available in the industrial field: corrective, preventive, condition-based and proactive maintenance.
Corrective maintenance is the traditional replacement of a part or component that is no longer functioning, with a new part. This generally implies machine downtime and is not a programmable operation in terms of time and cost. To avoid unforeseen and random malfunctions taking place, preventive maintenance involves the planning of periodical replacements of parts, scheduled at regular time intervals, independently of whether the component is still performing satisfactorily or not. Condition-based maintenance rationalizes prevention, because the physical variables that determine the symptoms of a failure are monitored. According to the survey of these variables, specific measures are taken before the actual failure takes place, including the possibility of scheduling a maintenance intervention. Pro-active maintenance takes the process one step further. From the analysis of the machine, of the physical data and of data concerning the specific failure, it is possible to find its causes and propose the appropriate modifications to be made on the machine. This is the role of maintenance in reengineering.
The primary need was to optimize costs related to maintenance.
At the SCA Hygiene Products facilities in Collodi, the primary need was to optimize costs related to maintenance, since the critical machines/devices entailed machine downtime – something economically expensive and also a safety risk for the people involved. Thanks also to ISE’s contribution, a condition-based maintenance plan was set up at SCA Hygiene Products that would also define – together with the priorities – the survey operations, data analysis procedures and surveys of the technologies to be adopted.
The synergy with ISE has also allowed the making of appropriate choices concerning the instruments to be used, the data acquisition systems and methods of analysis of such information. It is important not to underestimate the fact that a correct maintenance procedure requires the use of the proper technology, and it is the correct choice of such technologies that leads to the success of the maintenance policy as a whole. This fact carries fundamental importance.
How the condition-based maintenance plan was implemented
The need to have a definitive improvement of industrial costs deriving from the frequency of failures imposed the implementation methods and schedules that are coherent with short-term economic return. The condition-based maintenance plan designed together with ISE personnel and implemented at the SCA Hygiene Products facilities was compiled through the following main phases:
a) Analysis of the critical components of the systems, choice of the condition-based maintenance technologies, definition of inspection schedules: a preliminary phase to select the systems to be monitored, the condition-based technologies to be adopted and the cadence of the inspections of the instruments and inspections.
This phase, underestimated by a less attentive user pool, has a decisive importance, because in many cases it determines the success of the predictive maintenance programme. It is clear that an over estimation of the systems to be monitored, or of their monitoring frequency, would lead to unneeded costs and dispersions.
Table 1 indicates the frequency with which some operations are carried out in the specific case.
b) The subsequent phase is the inspection phase and is carried out by paper mill personnel together with ISE experts for the technically more complex measurements.
In preparation for this phase, particular attention was dedicated to selecting the parameters for setting the instruments and the database related to the machines/devices to be controlled so as to correctly code and name the machines/devices themselves.
c) Once the software to be used has been set-up, we proceed with the periodical acquisition of the data of the components being observed. Then, the inspection report is compiled, containing the following information:
- Identification data of the machine/device
- Working conditions of the machine/device
- Acquired data
- Data analysis
- Description of the malfunction
- Cause of the malfunction
- Assessment
- Recommendations
- Cost assessment/benefits
During this extremely important phase, abnormalities are analyzed and classified according to 4 standardized assessment levels (Sufficient, Mediocre, Insufficient and Serious). The reports obtained are generally filed in a database that allows the measurements to be historicized relative to each machine or system, with the possibility of analyzing data trends in the course of time. The database is enhanced with other information, of course, such as components not inspected during the last check because not operating, replacements and any intervention carried out on each component, etc.
The implementation of an efficient condition-based maintenance plan determines the immediate advantages on the decrease of production losses and repair costs, optimizing the availability of the machines.