Autonomous maintenance is a good starting point
When companies begin to implement Total Productive Maintenance (TPM) they often start by piloting Autonomous Maintenance (AM). This is understandable as AM is one of the key distinguishing features of TPM and also one of the most important activities when understood correctly.
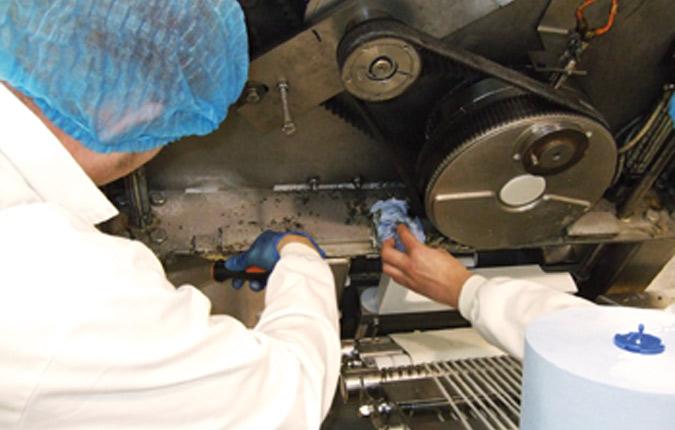
To understand AM correctly, it needs to be seen as an improvement activity within TPM, rather than production teams taking on maintenance activities. In the evolution of TPM in Japan, AM grew out of the 5S activities of production teams, as they found that in order to deal with barriers to Quality, Delivery and particularly Cost performance they needed to improve equipment conditions, initially by applying the principles of 5S and QC circles.
AM was not the result of a desire to reduce maintenance costs or maintenance departments wishing to hand tasks over to production, rather it was the result of production teams wishing to control and improve their equipment. Equipment performance is measured using OEE (Overall Equipment Effectiveness), which has become an industry standard, based on the Availability, Performance and Output Quality of the equipment.
These three factors are then broken down into Losses, of which Breakdowns, Changeovers, Minor Stoppages and Speed Loss are typically the largest contributors. Of these, TPM identifies the major cause of Breakdowns, Minor Stoppages and Speed Losses as the accelerated deterioration of the equipment – as much as 70 percent (95 percent in one French survey!) of equipment losses are due to preventable deterioration of equipment, and this is where Autonomous Maintenance comes in.
Autonomous Maintenance put simply is the restoration and prevention of accelerated deterioration and has a major positive effect on OEE. It is a step-by-step improvement process, rather than production teams taking on maintenance tasks. While visitors to TPM Prize Winning plants may be impressed by the operator maintenance standards displayed in the workplace, and the condition of the equipment and OEE performance, these are all the effects or endpoints of AM, and to reach these endpoints companies must follow the step by step process defined by the Japan Institute of Plant Maintenance (JIPM).
Start From Basics
The seven steps of Autonomous Maintenance follow three phases. At Industry Forum, an associate agency of JIPM, we also identify a Step 0 – understanding the equipment functions and safety risks. The first phase then follows the first three steps of Initial Cleaning, Elimination of Sources of Contamination and Inaccessible Areas, and Provisional Cleaning and Inspection Standards.
To conduct Step 1, Initial Cleaning, teams of production, maintenance and engineering staff shut down and lock off the equipment and then perform an in depth cleaning and inspection, looking for any signs of deterioration. Management are also often involved in these pilot exercises; one plant manager told me that he only really understood AM by taking part in an AM workshop. ‘The devil is in the detail’ – only by identifying and restoring all signs of deterioration can we ensure equipment performance is fully restored.
This raises another important point – AM requires some resources, and a rule of thumb is that issues raised during this initial exercise should be addressed within eight weeks, so the advice is always to look at one machine in depth, rather than trying to implement AM comprehensively. The advantage of this is that it enables a plant to rapidly discover the extent of equipment deterioration and the resource required to eliminate it.
Step 2 is to Eliminate Sources of Contamination and Inaccessible Areas – once equipment has been restored we need to ensure it does not deteriorate again by controlling all the contamination that leads to deterioration, and by improving accessibility for cleaning and maintenance. This is where we challenge teams to think creatively and look for the root causes of contamination, controlling them at source. Step 2 is important because if we do not control contamination we can become locked in an endless cycle of cleaning and restoration.
This then leads into Step 3, Establish Provisional Cleaning, Inspection and Lubrication Standards. Apart from the condition of the equipment, these standards are the most visible evidence of Autonomous Maintenance. Starting from current documentation, the AM team follows the lubrication and inspection schedule, noting any problems with accessibility, lubrication flow etc. and develops its own standard indicating items to be cleaned, checked or lubricated, the methods to be used and frequency and responsibilities. Some technical checks may still be the responsibility of maintenance rather than production and this is noted in the documentation.
This step also involves the visual management of the equipment and inspection process – marking gauges and sight glasses and even visually numbering the inspection route to prevent checks being missed. The final outcome of steps 1-3 should be a restored and improved piece of equipment with a visually-managed standard for cleaning, inspection and lubrication. This is what we see in the TPM prize-winning factories, but it does not happen without significant effort and attention to detail.
Continue to the End
The second and third phases, steps 4-7 consolidate the first three steps by improving production skills and knowledge and developing team autonomy, so that the production team develops owner-ship of its equipment, learns to set its own goals in line with company policy and manage its own improvement activities. This illustrates the dual aspect of AM, restoring equipment but also developing people and small group activities.
This can present a challenge in process industries where we have a large equipment base and a small number of people on rotating shifts and 24/7 working. Focussing the AM activity is even more important here and equipment ranking is often used to identify priority equipment for AM. Again the recommended approach is to pilot AM activities and learn from the pilot before attempting to roll out AM plant-wide.
The most common mistakes companies make in implementing Autonomous Maintenance are to start at the end point – the provisional standard – without going through the step by step process of restoration and improvement and also to start with too large an implementation before learning about equipment condition and resource requirements through pilot activities.
While the JIPM step-by-step process may seem overly prescriptive to some, it is a tried and tested methodology, which is the surest way of delivering the required result – with AM there are no shortcuts!