Are You Overlooking a Significant Source of Savings?
Some oil producers are using chemical management and saving up to 10 percent in chemical costs.
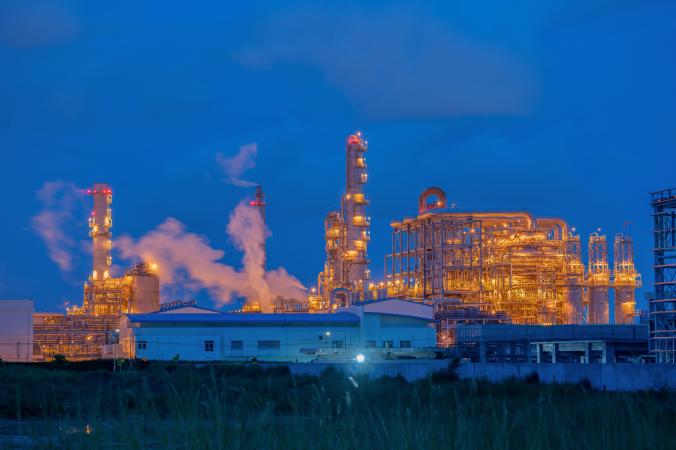
In the past, chemical usage was typically unmonitored. While oil prices are rising once again after the sharp decline over the last few years, there is still great emphasis on significantly reducing costs across all areas of production, both on and off shore. One area that is often overlooked in terms of applying solutions is the use of chemicals throughout production and processing. The injection of chemicals in a controlled and reliable process across an operation, be it land-based or offshore, is a key factor in the productivity, efficiency, and profitability of oil and gas producers. Applying a chemical management solution to an operation or field affects availability, performance, and maintenance in beneficial ways.
Often, there would be a tendency to add more than necessary to ensure pipes were never under dosed. What was thought of as an acceptable cost and part of the production process is now proven to be a waste of money and resources if not properly monitored and managed.
Inexact dosing can keep the chemical from reacting in the way it is intended, which can lead to hydrate formation (ice-like solids that form when free water and natural gas combine at high pressure and low temperature). Imprecise dosing can also lead to fines for the operator and damaged equipment, which can lead to costly unplanned process downtime. Due to the wide variety of chemicals used across the operation, the cost of over injecting can quickly mount if left unchecked. A reliable and robust chemical management system should deliver 10 percent savings in chemical costs or more.
Data Challenges and How to Deal with Them
One of the main challenges in creating a successful chemical management system concerns data. Chemical injection dosages, tank levels, and chemical inventory should be monitored and produce data from which you can draw insights. If you are monitoring data, it needs to be reliable, not have any gaps, and be accessible to those that need it in a timely manner. One of the main challenges for effective chemical management is connecting all relevant data and information sources together for reliable and accurate decision making.
The need for a dedicated chemical management system operating within a connected data environment should be high on the “strategic to-do list” for oil producers. While SCADA systems are popular for storing data,you need the right analytics and visibility to gain timely insights and act upon them to get the most out of your data. Many operations have separate applications collecting data for different engineering disciplines, such as chemicals, corrosion, integrity, erosion, production, environmental, and lab analysis to name but a few. The difficulty comes in bringing all data sources together in one system to provide a complete picture of chemical management and production.
One of the main challenges in creating a successful chemical management system concerns data.
In today’s digitally connected world, many processes are still manual and isolated, and a lot of time is wasted collating and analyzing data. By the time reports are produced, the information is already out of date. This inefficiency and ineffectiveness can be a result of data that is manually entered, stored in multiple or remote locations, in different formats, or is simply hard to access. To address this problem, Bentley’s AssetWise solution is underpinned by a connected data environment and is an illustration of how interoperability is the cornerstone of information accessibility. AssetWise allows the seamless integration of isolated systems and processes that bring the information you need into the Operational Analytics platform for consolidation and analysis. The data is turned into actionable information and viewed within dashboards that are easily tailored to specific needs.
Requirements of a Chemical Management System
A dedicated chemical management system will report on measurements like flow rates, levels, and discharge pressures. It will also be committed to providing alerts regarding any upcoming events that affect production, such as notice of potential equipment failure and drops in pressure or flow rates. The system can automatically inform events maintenance, so they can plan and schedule corrective action before the asset fails, as opposed to requiring unplanned site visits after a failure occurs.
With the large and complex set of assets, systems, components, and parts that make up any given operation, there are numerous things that can go wrong that affect process flow rates and pressures, operating temperatures, and the like, such as general wear and tear, equipment fatigue, and human error. It only takes a small change in one of these variables to upset the condition and performance of a finely tuned system, where the consequences of a small error can be large and costly if left unchecked. It’s important to know the day-to-day metrics of production against targets, chemical usage, and discharge, so you can measure performance effectively. However, it’s also crucial to have a system that recognizes these changes (or the results of these changes) and can address them and alert personnel to the problem before it happens.
A chemical management solution should have a template and replication feature to create a standard for commonly used systems and structures so that new additions to the registry can be swiftly uploaded. Any changes that need to be done across multiple sites or assets can be replicated across all required points easily by adjusting the template for a specific instance.
Many assets are owned by multiple vendors, so a flexible, yet secure, chemical management system is necessary for tracking who is using what while maintaining the security and privacy of each vendor. Each vendor needs to have their own secure access to the system. This would also include the ability to schedule truck services for manual sampling and injections so that vendors are aware of what chemicals are needed, where they need to be applied, and when they need to be applied, which is crucial, especially when dealing with assets across a large geographic area. This allows each vendor secure monitoring of their own activities and integrity maintenance of confidential information, while the overall operator has access and control of all information.
A critical, but often forgotten, requirement of a chemical management system is to create and maintain the chemical list. This is due to the variety and nature of the different chemicals used. As some chemicals become more concentrated, they could have a detrimental effect on the performance of the equipment with which they interact. The viscosity and frequency of chemicals also plays a large role in flow rates, pressure, temperatures, and general wear and tear. Creating and maintaining a chemical list is important within a chemical management solution to not only track chemical levels, but also to track chemical performance, suitability, and risk.
Lastly, the use of chemical injection systems is subjected to extreme conditions. These systems are often placed in remote hostile environments where the elements alone can cause serious equipment failure. Therefore, it is even more important to monitor and manage these assets closely to prevent failures. When operating in these harsh conditions, it is inevitable that these injection systems will eventually fail; it is a question of when, rather than if. Having a reliability strategy in place, such as the AssetWise Asset Reliability solution, that runs alongside the operational chemical management solution, such as the AssetWise Operational Analytics, is a win-win situation that serves the purpose of increasing uptime, reliability, and availability across the operation by driving a proactive approach to managing the maintenance of chemical injection pumps and equipment.
Chemical Management: A Step toward Operational Excellence
A reliable chemical management solution is the way forward to managing chemical costs and optimizing usage by ensuring you are applying the correct chemicals at the optimal rate to deliver best and continuous operating performance. Eliminate the nightmare created by spreadsheets, isolated data, unreliable information, and out-of-date information and replace it with a dedicated solution that brings all the important data together in one application. By doing so, you will dramatically reduce chemical costs, becoming more efficient, productive, and cost-effective.