Using Ultrasound for Friction, Impacts and Turbulence
A thorough Failure Mode and Effect Analysis, FMEA, might well highlight failure modes related to increased friction, the presence of impacts or the presence of turbulence. These are three key parameters detectable by airborne and structure-borne ultrasound. Whether evaluating equipment reliability or establishing a strategy, ultrasound has an important part to play.
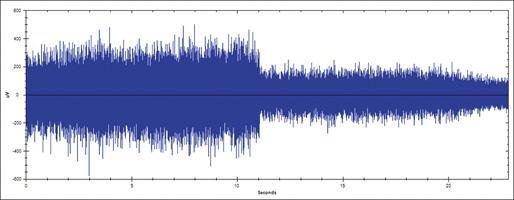
Ultrasound is high frequency sound – technically any frequency above 20 kHz, though a typical system of the kind used here is working around the 36 – 40 kHz region. Sound will travel through gases, liquids and solids. Ultrasound is no different. There are applications using ultrasound in all three media.
Since ultrasound is by definition inaudible to the human ear, signal processing is required to make the inaudible, audible. Ultrasound has been used by industries around the world to great effect on a number of very common, simple, day to day, reliability issues.
This is achieved using a technique known as heterodyning. Using this process, the 36 – 40 kHz inaudible region becomes an audible signal with a 2 kHz bandwidth. This essentially gives the user a sixth sense.
Effectively, using ultrasound means that the user can hear friction, turbulence and impacts. If your FMEA shows up potential defects whose characteristics are friction, impacts, or turbulence then ultrasound should be the most important tool in your toolbox.
What is FMEA?
In practice Failure Mode and Effect Analysis, FMEA, is a formal, structured, thorough application of Murphy’s Law.
- What can go wrong?
- How will it go wrong?
- How can we find that?
- How can we design it out of the process?
- How can we minimise its impact?
- What is the probability of occurrence?
This technique, when allowed free rein, will find the true show stoppers – the, often simple, things that trip you up. It is the small trivia that stops everything.
Most common mistakes are made at the How can we find that? phase. Instead of ensuring that the Company has the necessary tools to locate all of the defects, it is common at this stage to just settle for what can be measured now. This puts an inherent limitation on the potential success of the predictive maintenance programme.
Case histories
The rest of this article is devoted to relating the stories of a series of case histories involving process failures that could have been averted, and successfully identified potential failures.
- Instrument air leaks causing failure
- Valve problems causing processes to stop
- Developing an on-condition bearing lubrication programme
- Widening the scope of an electrical inspection programme beyond infrared
Compressed air leaks
Some organisations waste fortunes on air leaks, some organisations do something about it. On a recent visit to a large research facility, a rough calculation based upon their air production capacity, the price paid for electricity and a 25 percent air loss (the low end of the industry average 25-40 percent losses) gave a savings target of $1.7M. Other visits reveal huge savings achieved by bringing the external surveys in-house and then aggressively attacking the challenge of the leaks.
A very important use of air is the control air or instrument air and also the air used for pneumatic systems. The problem is that these systems are often overlooked by the air leak surveyors because the potential savings are tiny and they are overlooked by the FMEA performers because it’s air.
In one case, on a gas pumping station this hit the Company hard. This large organisation had built its own power station which burnt its own gas. There was a perception within the Company that air leaks were trivial and of no economic consequence. At 3 AM one morning (why is it always 3 AM?) a remote pumping station tripped. The station had three instrument air compressors and was designed to operate with only one. With all three running flat out the plant tripped out on low instrument air pressure resulting in losses of $250k per hour.
Sadly, the long-term fix was not to repair all of the air leaks. No, instead they bought an additional compressor to take the lead. It was with slightly larger capacity than the three original compressors and then used the old compressors for top-up.
Valve problems
When considering the condition of a pump, is that condition independent of the suction or discharge valves? Is the failure of a pump to deliver the required pressure and flow rate just within the control of the pump? Why then are valves so often assigned to a breakdown or time-based replacement strategy?
Isolation valves and control valves are just two examples where failure can be critical to the operation of a process. If a valve is leaking, blocked, cavitating or flashing for example there can be direct process issues and indirect process issues resulting from the failure of that valve.
On a recent implementation at a pharmaceutical plant, I had the opportunity to train the company’s steam engineer on the use of ultrasound. He introduced me to a series of steam isolation valves – some were suspect, some had recently been replaced. Sadly, all of them when inspected were found to be leaking.
Bearing lubrication
The bearing manufacturers will report that up to 40 percent of premature bearing failures are caused by over lubrication, yes over. So why is it that such a common and well-known cause of falure does not draw more attention? Why is it that so many organisations still run time-based lubrication programmes based upon the incorrect injection of variable amounts of grease?
Lubrication is supposed to reduce friction. Excessive lubrication increases friction – the walk on the beach analogy is a good one here: it is much easier to walk at the water’s edge than it is when the water is up to your knees. The same process applies to bearings; correctly lubricated there is a condition of aquaplaning with almost frictionless motion.
Since ultrasound hears friction, ultrasound can be used to evaluate the friction condition of a bearing and help, live, to get that bearing to its lubrication sweat spot.
Ultrasonic lubrication therefore not only prevents costly bearing failure, but also extends bearing life and reduces grease consumption. A rare win/win/ win situation.
Electrical inspection
Spreading from the US is a risk-control system for electrical installations called NFPA70E. This process deals with minimising the risks associated with arc flash and arc blast.
I find many organisations where the condition assessment of electrical systems is left entirely in the hands of thermographers.
Infrared (IR) thermography is an extremely useful defect detector. But it has limitations which are frequently ignored, or, are themselves the cause of problems. The two key problems here are:
- IR needs line of sight of the object
- The defect mechanism must generate heat (or cold)
Because IR needs line of sight it is essential to open the doors if IR windows have not been fitted. This process can be the initiator of an arc or expose the unwary thermographer to an existing arcing condition. The second point is also very important: there are defects in electrical systems like tracking (any voltage) and Corona (surface partial discharge normally above 2kV) which do not generate any heat. They do cause damage to electrical systems, but no heat.
The FMEA can now be flawed or can even be the root cause of a failure by stipulating the need to open a door or cover behind which there is already a problem.
Ultrasound can hear arcing and tracking and Corona taking place behind a panel. Using ultrasound as the primary detection tool for such defects can therefore not only identify failures which IR would have missed but also, and more importantly, perhaps prevent a severe injury or even a fatality.
A Heat Pump Plant Turns the Carbon Footprint of Textile Fibre Production Negative
Valmet launches intelligent fiber furnish control to secure better refiner operation
Valmet introduces the Valmet Fiber Furnish Control application package for board and papermakers to stabilize refiner operation for maximized production efficiency with ensured furnish quality. Based on real-time measurements of multiple fiber properties and freeness, the control features advanced feedback and feedforward solutions together with model predictive control.