Using Spectrum Analysis of Recorded Ultrasounds
Airborne & Structure-borne ultrasound instruments have become a perfect complement to infrared and vibration analysis tools. Mechanical and electrical diagnosis can be done through ultrasound imaging.
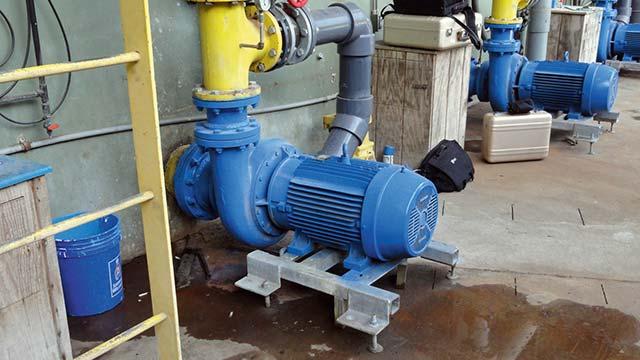
Ultrasound can no longer be considered just a leak detector, and most would consider ultrasound a must have technology for any maintenance & reliability programme. Advancements in instrumentation and software have allowed the users of these instruments the ability to accurately diagnose electrical conditions such as corona, tracking, and arcing.
Mechanical inspections include diagnostics such as bearing faults, pump cavitation, and valves. However, using the concept of ultrasound imaging, one can diagnose mechanical failures in rotating equipment, and electrical conditions such as corona, tracking, and arcing.
Traditional inspection of electrical components has been performed using an infrared camera. Users of this technology rely on images showing temperature changes that may represent electrical anomalies such as tracking and arcing. For mechanical inspection, vibration analysis has been the conventional method of inspection for condition monitoring of rotating equipment.
Vibration analysis produces a visual spectrum or time waveform that shows any fault harmonics. If the goal is to have a truly world class predictive maintenance programme, the use of multiple technologies is recommended for various inspections. Just as a physician uses multiple tools to take vitals and diagnostics to determine aches, pains, and abnormalities, maintenance professionals should take the same approach when it comes to the assets that we are responsible for in our facilities.
In addition to using infrared and vibration, ultrasound can be used to complement other PdM technologies. Airborne and structure-borne ultrasound can also give the user an image to analyse, diagnose and confirm mechanical and electrical conditions.
Ultrasound technology and instrumentation has evolved into a must have technology for both condition monitoring and electrical equipment reliability applications. The concept of ultrasound imaging is to record ultrasounds heard via the ultrasound instrument, and then play back those recorded sounds in spectrum analysis software.
This will provide the inspector with an audible sound heard in the field during the inspection and a visual image or spectrum of the recorded ultrasound. This method will help to reduce the subjectivity of only relying in changes in the decibel level and changes in the sound tone or quality heard by the inspector.
Gives Complementary Data in Mechanical Inspections
Reciprocating compressor valves are very noisy and produce a lot of extraneous vibration. By isolating the sound with the advantage of the short-wave nature of ultrasound, it is possible to listen to and view the sounds of these noisy valves in real time, and to determine when a valve is leaking.
How would you imagine the sound of a good compressor valve? As it opens and closes, there will be a definite pronounced clicking. What about a bad valve? The bad compressor valve has a much longer time period when it is open before closing.
Figure above shows a motor and pump combination. The motor was a 60hp powering a pump that was pumping water. The image below was taken while the data was collected. This will be a comparison between two of the eight total motors and pumps.
While collecting data, both decibel readings and sound files were recorded. The screen shots above show a comparison between the points “PUMP 3 MTROB 007” and the “PUMP 4 MTROB 010”. The images are FFT images from spectrum analysis software that plays back recorded ultrasound sound files. This software is available with ultrasound instruments that have onboard sound recording capability.
Notice the difference between the two points. Both motors are operating under the same conditions, but the Pump 4 MTR OB point has a much different spectrum. If you were listening through the headset of the ultrasound instrument, it would also have a much different sound. Another image of the Pump 4 MTROB point, captured from onboard the ultrasound instrument, can be seen below.
The spectrum analysis software used has a built-in bearing fault frequency calculator. By entering in the speed (rpm) and the number of balls (bearings), an outer race, inner race, ball pass, and cage frequency will be calculated. For this particular motor, the speed was 1750rpm and the type and number of bearings was confirmed and the number of bearings was 10.
The fault frequency calculated by the spectrum analysis software that was of interest was an inner race fault at 175Hz. This is the same fault harmonic detected on the ultrasound instrument.
Improves Safety in Electrical Inspections
One application for ultrasound that has seen the largest increase in usage over the last several years is for electrical inspection. Ultrasound can be used to listen for electrical conditions such as corona, tracking, and arcing. Each anomaly has a distinct sound, and can easily be identified and confirmed through the use of ultrasound imaging.
Ultrasound should be considered by anyone performing electrical inspections with infrared. Before opening any energized electrical panel, a pre-inspection with ultrasound should be performed. The ultrasound emissions can be heard through vent openings, cracks/seals around the door, or through the use of an ultrasound port. If a suspect sound is heard, the sound can be recorded and then analyzed to determine the condition (corona, tracking, or arcing).
Corona, the ionization of air surrounding an electrical connection above 1000 volts, is heard using the ultrasound instrument as a steady, uniform, static sound. When looking at the recorded ultrasound of corona in spectrum analysis software, very distinct and evenly spaced peaks or harmonics can be seen.
The harmonics appear every 60Hz. This would also be noted as 50Hz harmonics if you were in a country where 50Hz electrical current is used. You can also see frequency content, peaks within the peaks, between the 60Hz harmonics. These are signature features to look for when analyzing recorded ultrasounds of corona.
Being able to detect corona with ultrasound is particularly helpful because corona typically does not produce significant heat to be detected with infrared. It does however have a very distinct sound. If an inspector were relying solely on infrared, this condition would have gone undetected.
With electrical inspection, the well-defined 60Hz (or 50Hz) harmonics will diminish as the condition becomes more severe. The example below is from a recorded sound file of Tracking. Tracking, commonly referred to as destructive corona or baby arcing, has a different sound than that of corona. Tracking typically has a more distinct continuous frying and popping sound. Also, notice the increased amplitudes indicating a more intense sound versus the amplitudes of corona.
The analysis of arcing is even more evident of the loss of the uniform 60Hz harmonics. With arcing, the electrical discharge becomes more erratic and has sudden starts and stops of the discharge. This can be seen in the time series view of a recorded sound file of arcing.
As individuals responsible for the condition and reliability of the assets in our facilities, we should want to use as many tools as we can to inspect those assets. Through the proper use of multiple PdM tools, the data that we collect with those tools can give us better results, and more potential failures can be detected.
The concept of ultrasound imaging or recording and analyzing ultrasounds via an ultrasound instrument is fairly new when compared to other technologies. However, the use of ultrasound for both mechanical and electrical inspections is growing. The spectrum analysis of recorded ultrasounds can enhance diagnostic accuracy, and reduce the subjectivity of only comparing decibel readings and changes in the tone of the sound heard by the inspector.
A Heat Pump Plant Turns the Carbon Footprint of Textile Fibre Production Negative
Valmet launches intelligent fiber furnish control to secure better refiner operation
Valmet introduces the Valmet Fiber Furnish Control application package for board and papermakers to stabilize refiner operation for maximized production efficiency with ensured furnish quality. Based on real-time measurements of multiple fiber properties and freeness, the control features advanced feedback and feedforward solutions together with model predictive control.