Thermal Imaging Cameras Support the Safety of Italian Gasification Plants
Gasification is a promising technology for generating energy. At ISAB Energy, located in the vicinity of Priolo, Sicily, gasifiers are used to convert residual oil fuel into energy under high temperatures. To make sure this process runs smoothly and safely, thermal cameras are continuously monitoring the skin temperature of gasification vessels.
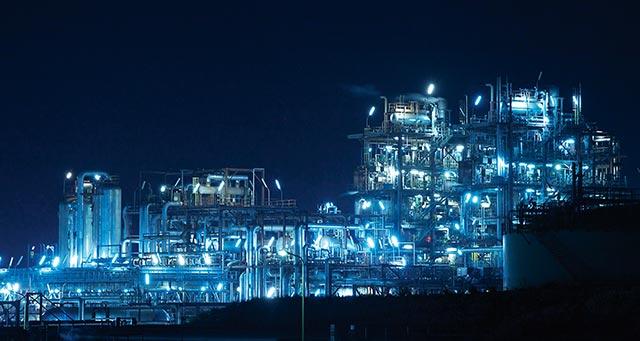
The ISAB complex comprises two refineries connected by a pipeline system and integrated into a single engineering complex with a total capacity of 16 million tons a year, a tank battery with a capacity of 3,700 thousand cubic meters and three marine terminals. At the ISAB Energy power plant, electricity is being produced from gasification of oil process waste.
Gasification is gaining interest again as a valuable solution for energy production. Today, the output from gasification is used directly in electric generation, biofuel production, and production of other consumable liquids or gases, like methane and hydrogen. Through a process that occurs at extremely high temperatures, the gasifiers of Isab Energy srl convert the tar, oil processing waste, into a synthesis gas, called syngas, which is reused as fuel for producing electric energy. Thus this process allows the production of energy making use of a by-product, which otherwise would not be used.
Monitoring Temperature
Residual oil is fed into the gasifier vessels and mixed with oxygen and steam. This gasification process generates temperatures of more than 500°C in high pressure. The critical temperatures reached during this process must be kept under control in order to ensure the stability and the safety of the plant. Explosion hazards are a real threat to the safety of the gasification plant. When temperatures of the gasifier skin exceed a certain value, the skin iron can become ductile.
Combine that with the continuous high pressure inside the gasifier and you have a highly explosive situation. That is why it is extremely important to monitor the gasifier’s skin temperature.
To ensure plant safety, ISAB Energy relied on the expertise of IMC Service, a specialist in the field of thermal monitoring and professional inspections. The company has been working with the main petrochemical and chemical groups in Italy for over 20 years. Since 2004 they also work in thermography for industrial inspections (standard and furnaces) and they design and develop integrated hardware and software solutions for continuous thermal monitoring of production processes.
IR-SyM Control Module
To continuously monitor the gasifiers’ skin temperature, IMC Service developed a dedicated, centralized control and monitoring system, called IR-SyM. The system makes use of 24 A310 thermal imaging cameras from FLIR (12 cameras each for two gasifier vessels). The system also allows continuous and simultaneous management of these 24 cameras.
The IR-SyM system performs a continuous and accurate control of the gasifiers’ skin temperature. The system has been configured to automatically respond to excess heat, by reporting alarms that are set with different times of response depending on the heating curve. The application provides a complete overview of acquired data: the graph of temperature changes, real time updated thermograms and temperature history in radiometric format and in absolute value. IR-SyM stores thermograms every 60 seconds in absence of alarms, while in case of an exceeded threshold, an alarm is generated within 5 seconds.
The system management interface is accessible via the local network or remotely via VPN and does not require the installation of any software. This allows technicians to monitor the process at any time and from anywhere there is a network connection. The thermal imaging cameras can also be configured via the web interface.
Reliable Temperature Measurement
– In the past, the gasification plant has been using other temperature measurement methods, like thermocouples, but none of them were very efficient, explains Giovanni Distefano, director at IMC Service.
– Then we discovered thermal imaging cameras. After having evaluated and used several camera brands, none of them proved to be as reliable as the FLIR A310. We have been working with FLIR Systems on other environmental monitoring projects and there we had the chance to test and evaluate different FLIR cameras. That’s how we knew that the FLIR A310 would be just the camera we needed for this project.
All installed equipment is certified to operate in hazardous areas with potentially explosive atmospheres. Therefore, the whole equipment has been designed with the proper Ex certification for safety purposes. In proximity of the gasifier and during the summer season, temperatures exceed 60°C, which made it necessary for IMC Service to design a cooling system and enclosure for the thermal imaging camera, which ensures their correct operation even in critical environmental conditions.
The Thermal Imaging Camera
The FLIR A310 thermal imaging cameras that are included in the gasifier monitoring system contain an uncooled microbolometer detector that produces thermal imaging with a resolution of 320 × 240 pixels at a thermal sensitivity of 50 mK (0.05 °C). These cameras target safety and automation applications where networking capabilities and compliance with networking protocols is of essence. The infrared cameras can be installed discretely almost anywhere and are ideal for any industry where fire prevention, critical vessel monitoring and fixed-mounted predictive maintenance are important.
– The big advantage of thermal imaging cameras for this application is that, unlike thermocouples for example, they can accurately monitor wide surface areas, comments Giovanni Distefano.
– This allows us to identify overheating geometrically and more precisely and also to evaluate and plan maintenance activities that have to be performed immediately.
– Next to being an economical solution, we have also found this one to be a very reliable camera, Giovanni Distefano continues.
– This is especially critical in the high-temperature and possibly explosive environment the gasifiers are operating in.
A Heat Pump Plant Turns the Carbon Footprint of Textile Fibre Production Negative
Valmet launches intelligent fiber furnish control to secure better refiner operation
Valmet introduces the Valmet Fiber Furnish Control application package for board and papermakers to stabilize refiner operation for maximized production efficiency with ensured furnish quality. Based on real-time measurements of multiple fiber properties and freeness, the control features advanced feedback and feedforward solutions together with model predictive control.