The Industrial IoT Maturity Model
A new model is helping to guide decision makers along a successful path in the manufacturing space.
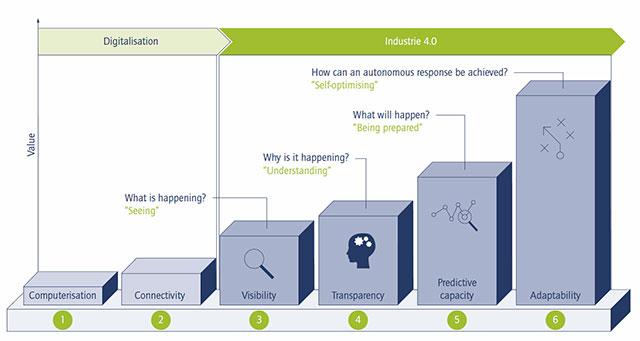
Text: Stefan Hoppe, Global Vice President of OPC Foundation
Many manufacturing and industrial companies have realised that digital transformation will require changes in the way they do business. Experts will tell you that digital transformation is not about making energy discrete, and process manufacturing more efficient, but is about establishing new business models while continuing to make money from their old business models.
These changes are so substantial that many talk about a revolution, namely the 4th industrial revolution. The Industrial Internet of Things – abbreviated to IIoT and known in Germany as Industrie 4.0 – is a technology trend that is the enabler of this revolution, and is bringing about a transformation in the way we do business.
So, how do you know you are on the right path? It’s a question that many company executives are asking themselves these days. Experts have therefore established a ‘maturity model’ that aims to guide decision makers along a path that leads to success. We call it the Industrial IoT Maturity Model. Acatech in Germany has released a study on the subject, named the Industrie 4.0 Maturity Index.
This is one of the most important insights. Many companies think that all they have to do is connect their machines to the internet and they are ‘done’. But as always, this is just the beginning. In their study, Acatech built a great model, which is pictured alongside this article.
When it comes to the Industrial IoT Maturity Model, the age of computerisation has helped make production processes more efficient. Many call this the ‘mechatronic’ age or ‘Industrie 3.0’. This is the first stage of the Maturity Model.
Connecting machines to one another and to the internet is then the second stage. For this connectivity to be efficient, a single data model for information exchange is required to format the data consistently. The protocol used for transporting the data on the other hand, is irrelevant, although many people tend to focus on this in error. This is where the power of open-source industrial interoperability standards like Open Platform Communication Unified Architecture (OPC UA) becomes critical. OPC UA has an extensible information model, allowing the easy mapping of many of the standards used in the industrial sector today, and allowing for the creation of a single data model.
These two stages are the “table stakes” – no more. Where the digital transformation journey really begins is in the next stage, namely the visibility stage. This stage requires the use of visualisations, either on-premise or on a website that can be accessed from anywhere in the world. This allows stakeholders to see what is happening at any given time by looking at the stream of telemetry data from the machines – usually referred to as time-series data. If a database is additionally connected, historic time-series data may also be viewed.
The next stage in the maturity model is the transparency stage and analytics software can be used to understand what is happening or has happened. The analytics software usually comes with a set of rules created by experts – essentially people who understand the workings of the individual machines deeply. These can be applied to the time-series data, either as it is streamed through the analytics software (hot path analytics) or applied later to the time-series data in the database (cold path analytics). Once the data has been evaluated using the rules provided, conclusions about why something has happened can be deducted.
It gets really interesting when predictive models are applied to the data stored in the database. This is the fifth stage. Machine learning algorithms are used in this stage to predict the future, given the historic data collected. Sometimes it is useful just to be able to predict a few seconds into the future to prevent damage or accidents. Other times, it is useful to predict days or weeks into the future to allow for the maintenance of a machine before it breaks down.
The final stage is where the largest change within an organisation is required. Once the previous stages are implemented, a company can start making guarantees regarding the reliability of the machines it sells. This leads to new business models, where the cost of the machine can be offset with a guaranteed service instead. If done right, the cost of the machine may even be able to be waived and a ‘pay per use’ model introduced. For example, a barcode scanner manufacturer can slowly migrate from selling scanners to selling scans. In addition, maintenance of the machine can be fully automated, creating ‘self-healing’ machines and processes.
The tools used in stages three to six are readily available from internet of things (IoT) platform providers. To make these tools available worldwide and keep them scalable requires multi-billion dollar investments. Machine builders and factory owners should therefore not try to build these tools themselves, but focus on their machine and manufacturing process expertise and add value where they can differentiate.
Author of this text Stefan Hoppe is Global Vice President of OPC Foundation
A Heat Pump Plant Turns the Carbon Footprint of Textile Fibre Production Negative
Valmet launches intelligent fiber furnish control to secure better refiner operation
Valmet introduces the Valmet Fiber Furnish Control application package for board and papermakers to stabilize refiner operation for maximized production efficiency with ensured furnish quality. Based on real-time measurements of multiple fiber properties and freeness, the control features advanced feedback and feedforward solutions together with model predictive control.