Avoid Unplanned Machinery Failure on Cooling Towers
Varying loads and large rotating fan blades are just two of the reasons that mechanical components in cooling towers experience stress and performance degradation. Wireless vibration technology helps to identify potential problems, schedule maintenance and prevent unplanned downtime.
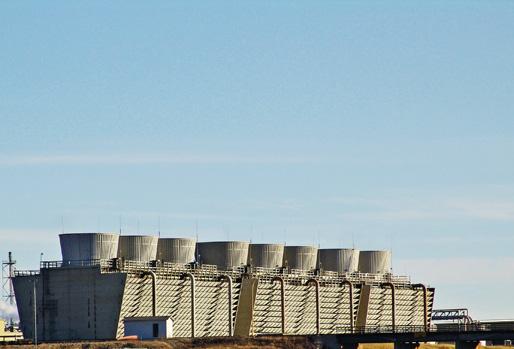
Cooling towers and fin fans are widely used to cool process water for reuse within power stations, refineries and petrochemical plants and these are often critical assets. A cooling tower utilises the evaporation of the cooling liquid to dissipate heat. The liquid is released at the top of the tower, cascading down across a series of ventilated shelves. A fan draws fresh air through the shelves and across the falling water. The air cools the liquid which is collected, filtered and returned to the delivery system to gather more heat.
Typically cooling towers have an AC motor with a long shaft connected to a right angle gearbox that drives a fan. The fan and its drive parts experience more wear and tear than any other parts in the cooling tower. They operate under different load conditions, often only running at peak load for short periods and with differing stresses over a prolonged period. Because of this, the mechanical components can develop degraded performance, which leads to failure. Also, as with any rotating equipment, bearing and gear failures, misaligned drive shafts, and excessive vibration are common.
Just as common is the lack of predictive information on the performance and condition of machinery in the towers. Vibration monitoring is one of the key ways to `listen’ for developing problems and the most commonly used method to monitor vibration is manual measurements on a periodic basis. With a trained analyst to review the data, these periodic checks can be used to detect many faults in advance; even then, however, they still leave the plant vulnerable to unplanned outages in between measurements – often with serious consequences to availability and profitability.
Typically, when the cooling tower is in production, because of its design maintenance staff cannot gain access and therefore do not have means to collect health information from the gearbox. This means impending failures can go unnoticed during extended periods of operation.
With access to the gearbox difficult whilst the cooling tower is operating, vibration data analysis typically only addresses the motor. This limits the usable information on the entire machine and does not provide an accurate picture of equipment condition. Having limited diagnostic data makes root cause analysis difficult and incomplete data makes it hard to plan maintenance, especially when you have to take into account production schedules, budgeting, approval and ordering of spare parts.
Because maintenance can only be performed when the tower has been shut down, being given advanced notice of impending failures is critical. Having this data allows maintenance work to be scheduled and unplanned shut downs, which have a significant impact on production, can be avoided.
Online Monitoring
Online monitoring can report vibration levels on a continuous basis, thereby removing the opportunity for problems to go unnoticed between periodic checks. This information can be historicised and made available to the maintenance department as well as operators in the control room.
Despite the availability of online monitoring solutions to determine the health of cooling tower machinery, many still remain unmonitored. This is primarily due to the high cost of retro-fitting installed equipment to add a monitoring system. This is where wireless technology becomes a more cost-effective solution to implement.
Wireless monitoring reduces or eliminates the costs of engineering, trenching, and cabling that discouraged more continuous monitoring in the past. It also enables measurements to be obtained from places where supporting cable infrastructure is not present. A well-designed wireless infrastructure provides a cost-effective, expandable and easy-toconfigure solution that can be integrated seamlessly into an existing control and asset management network.
Continuous Machinery Health Information
Access to continuous information on machinery condition allows for detection of problems before they lead to failure. As part of Emerson’s Smart Wireless solution, the CSI 9420 Wireless Vibration Transmitter provides insight into the health of cooling tower gearboxes and motors. The CSI 9420 can be installed without additional cabling and delivers real-time predictive diagnostics on the performance of the mechanical components. Vibration data is communicated over a self-organising Smart Wireless network, removing the additional costs associated with installing cables.
The comparison of vibration data to an alert level provides an alarm notification when the asset condition is deteriorating, as well as information about the underlying cause of the problem. Trend values can be compared against appropriate alert levels, informing operators of deteriorating gearbox or motor condition and aiding with root cause analysis. More detailed information can be accessed through high-resolution spectra and waveform data.
Poor bearing quality is often a contributor to equipment faults in cooling tower gearboxes and motors. Because of the force applied to bearings in a cooling tower, defects often progress quickly and lead to friction, damage, and failure.
Emerson’s PeakVue technology uses overall vibration and temperature measurements to identify developing bearing faults early, often preventing additional damage to the equipment. Using PeakVue technology, users can separate stress waves from overall vibration data for accurate early identification of wear on bearings and gearboxes.
Essential Asset Monitoring
Wireless also makes it feasible to gather multiple types of data that can help understand the health of a cooling tower. For example, the concentration of impurities increases as cooling water is lost through evaporation. Higher levels of impurities allow the build-up of scale.
Wireless conductivity transmitters provide an indication of impurity concentration, so that adjustments to blowdown rate can be made. High performance flow measurements provide valuable insight into cooling tower operation. Cooling water supply and return flows are indications of cooling tower performance and can indicate a problem with an associated pump.
Wireless DP flowmeters are available to support the need for additional flow measurements. Accurate, reliable temperature measurements are critical to determine the efficiency of heat transfer in cooling towers and fin fans. Wireless temperature transmitters are ideal for this high performance application to enable optimisation of the cooling tower at a low installed cost.
With Emerson’s pre-engineered cooling tower health monitoring solutions, readings for vibration, pH, flow and temperature can all be broadcast over the same wireless network.
Case Study: Chemical Plant Cooling Tower Monitoring
Wireless vibration monitoring is helping a Portuguese petrochemical plant to identify potential problems with cooling tower fans and pumps. The plant’s cooling tower unit has nine cells, all of which incorporate motors, fans and gearboxes, and eight water pumps. This unit is very important for both the production processes and auxiliary systems and is very flexible, with the number of cells in operation determined by demand.
Pumps and fans within the cooling tower unit were not connected to an online monitoring system. To obtain vibration data, manual readings were taken using portable handheld devices every two weeks, with data analysed offline. Monitoring the fans was particularly difficult, with maintenance teams unable to enter the cells when they were operating.
The company decided to install an automated condition monitoring system that would overcome these constraints. Data would be collected within predefined time intervals and provide full spectrum, overall and peak vibration values to help identify potential failures. Wired and wireless monitoring solutions, and a hybrid of both were all considered, but the cost and time required to install new wiring was found to be high.
Having compared the different systems available, the company selected Emerson’s wireless vibration monitoring solution. During a scheduled shut down, three vibration sensors were installed on each of the unit’s eight fans and nine pumps (51 in total) and 34 of Emerson’s CSI 9420 wireless vibration transmitters (two per fan/pump) were connected to the sensors.
Data from the wireless transmitters is sent, via a gateway, to the existing DCS, enabling operators in the control room to view overall vibration and PeakVue values from the equipment. Set-point alarms enable operators to be alerted to potential equipment health issues from which they can action the maintenance team to perform inspections and necessary repairs. Operators are also provided with wireless system health data, alarms for communication and general system failures, and also low battery life alerts.
The company now has much more data available and importantly has greater visibility of the health of the cooling tower equipment from within the control room.
A Heat Pump Plant Turns the Carbon Footprint of Textile Fibre Production Negative
Valmet launches intelligent fiber furnish control to secure better refiner operation
Valmet introduces the Valmet Fiber Furnish Control application package for board and papermakers to stabilize refiner operation for maximized production efficiency with ensured furnish quality. Based on real-time measurements of multiple fiber properties and freeness, the control features advanced feedback and feedforward solutions together with model predictive control.