Clean Components Decrease Unexpected Maintenance Work
In theory, it is widely understood that if fluid systems are assembled with clean components and filled with clean oil, there are fewer oil contaminant related disturbances during start-ups and during the life cycle of machines using fluid systems.
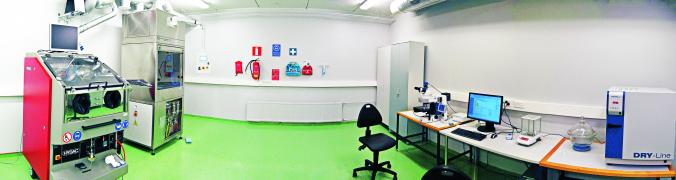
THE CLEANLINESS of the system is the sum of the particulate contaminants in components, added to the particulate contaminants in the filling oil. The cleanliness of oil has been measured since the early 1960s. But not until recent years it has been possible to measure the initial cleanliness from the parts of components or from the assembled components.
The component cleanliness research was successfully carried out in Germany within the Automotive Industry during the first decade of 2000, and resulted in the standard ISO 16232 in 2007. The component cleanliness code, presented in ISO 16232, is presented briefly as well as the necessary laboratory equipment required. The differences between oil cleanliness and component cleanliness definitions and codes are presented. The work phases in component cleanliness measurements, as well as the set of different results within fluid power components, are presented. Finally, the component cleanliness services done in TUT/IHA are presented.
The main equipment in component cleanliness laboratory
A semi-clean room for the component cleanliness equipment was constructed in TUT/IHA. The room is kept at 12 Pa overpressure and the incoming air is filtered. Inside the room are two commercial component cleanliness test cabinets (Figure 1).
The particle extraction from the studied component is done inside the component cleanliness cabinets to membrane filters. The main extraction method in both test cabinets is “pressure rinsing” with a pen but both are also used for “flushing”. In addition, HydacCTU 1200 have an “ultrasonic bath”. The method of analysis for both is a membrane filter that is studied with an automatic microscope (Figure 2) using application-oriented software.
Fig. 1. Automatic microscope (Carl Zeiss
AxioImager M2.m) with PC
The contrast methods in the microscope are: brightfield, darkfield, polarisation, and DIC. The objectives are: 2.5x, 5x, 10x and 20x. The reprogrammed standards are: ISO 16232, ISO 4406, and SAE AS4059.
Regardless of how the particles are extracted from the studied item on the membrane, they must all be photographed, measured, classified, and calculated to formulate the certain component cleanliness code (CCC-code) that is the result of the cleanliness analysis. The microscope takes 200–6400 pictures from one membrane depending on the magnification used. In addition, each particle picture is saved separately. This hard routine work is mainly done by an automatic microscope with appropriate software and a very effective
PC. However, a qualified researcher is needed to take care of this close inquiry to ensure that the whole analysis is executed according to the standardized rules.
The component cleanliness standard ISO 16232
The component cleanliness code (CCC code) is described with a number of particles with respect to the wetted surface area (A), or the wetted volume (V) or straight with respect to the component itself (N). After this, different particle size ranges are presented in parenthesis separated with “/”.
Table 1 presents the used particle size ranges (size classes B – K) and Table 2 the number of particles (cleanliness levels 00 – 24). If the result is announced with respect to the component itself, the number of measured particles of each size range is written after the size range letter.
The component cleanliness code (CCC code) may include for example:
• CCC = N (B585600 /C58200 / D18500/ E3600/ F2800/ G700/H190/ I4 / J0)
• CCC = A (C16 / D18/ E12/ F8/ J0)
• CCC = V (B20 / C16 /D18 / E12/ F12/ G12/ H8 /I1 / J1 /K00)
The cleanliness of components are allowed to be compared to each other only when they are weighted with the same kind of wetted area (A) or wetted volume (V) of the component.
These measurements are normally carried out using a suitable solvent or low viscosity oil as an extraction liquid. The extracted particles can be calculated using the inline-method. The choices are an optical particle counter or an automated microscope using an appropriate computer programme.
Comparing oil cleanliness and component cleanliness
Figures 3 and 4 point out the fact that the particles ≥ 14 μm is shown as a sum in oil cleanliness standard (ISO 4406) whereas they are divided to nine different size classes (C-K) in component cleanliness standard (ISO 16232). So, decreasing the number of big particles is the main interest in component cleanliness studies.
For the sake of comparison the oil cleanliness requirement ISO 4406 for proportional valves is given 17/15/12 (140 bar), which is even better than the example in Figure 3.
Fig 3. The cleanliness of a 100 ml oil sample. Fig 4. The cleanliness of a hydraulic pipe flushed with 100 ml solvent.
Table 1. The size classes of particles in standard ISO 16232:2007 Part 10. Table 2. Cleanliness levels of particles in standard ISO 16232:2007 Part 10.
Test bench for cleanliness measurements of assembled components /Rinkinen 2013a/
The commercial test cabinets are not suitable for cleanliness measurements of assembled hydraulic components. That is why a test bench had to be designed according to standard ISO 16232 Part 5: Method extraction of contaminants on functional test bench. The test bench (Figure 5) is designed for the measurements of assembled hydraulic components (e.g. cylinder) and hollow components (e.g. hose).
The flow of a test liquid is achieved by a hydraulic gear pump. Oil (VG 10) is used as an extraction liquid in the test bench. Tested components are delivered back to customers after the measurement process has been carried out. Because of this, solvents cannot be used as extraction liquids because they cause rusting.
Extracted contaminants of test components are analyzed by microscope (≥15 μm) and an inline automatic particle counter (8-800 μm(c)).
The main limitations of the designed test bench are a maximum pressure of 50 bar, and a maximum flow of 60 l/min. So, the maximum dimensions for a hydraulic cylinder are 80/40-300 and for the hose ¾”.
Other suitable test components according to ISO 18413:2002 are: pumps, motors, hydraulic accumulators, valves, valve blocks, manifolds, filter housings, and pipes.
Component cleanliness results
The following examples show three different ways of presenting component cleanliness results: histogram, microscope picture of membrane and CCC-code.
INFLUENCE OF TRANSPORTATION /RINKINEN 2013B/
In modern manufacturing systems with several washing phases it is possible to reach a good level of component cleanliness. But there are also several possibilities to destroy the reached cleanliness result of the component e.g. in logistics or at the assembly stage.
One test was done for a normal size hydraulic valve block. The subcontractor had washed the valve blocks normally at the end of manufacturing phase and one of them was studied before transporting (Figure 6 left). The transporting was normal and typical to the customer and another block was studied after transportation. (Figure 6 right).
The concerning CCC codes are pointing the same data as follows:
• Before transportation ”CCC = N (C13 /D12 /E10 /F7 /G5 /H4 /I0 /J0 /K00)”
• After transportation ”CCC = N (C14 /D14 /E12 /F9 /G8 /H8 /I5 /J4 /K2)”
The inverted commas (“ “) around CCC code tells that this is not a standard way to sh ow CCC code with respect to component (N) where, however, cleanliness classes are used to tell the maximum number of particles in each particle range.
The large particles were mainly wood fibre, which is very understandable because the transportation was done in a wooden box covered with normal packing plastic.
CLEANLINESS OF HYDRAULIC PIPE
Developing the washing process of a hydraulic pipe can result in remarkable improvement (Figure 7).
The upper CCC-code (Figure 7) belongs to the unwashed pipe and the lower to the washed one. The washed pipe included on average 26 times (= 64 times) smaller number of particles than the unwashed pipe. The size classes ≥100 μm (F-K) are written in red font because they are considered most important in component cleanliness studies.
COMPONENT CLEANLINESS CODES IN FLUID POWER
Table 3 shows the range of cleanliness results for several types of fluid power components measured in TUT/IHA during the years 2011-2012.
Table 3 shows that the cleanliness of fluid power components varies widely. The results also show that there is a lot of work needed to improve the component cleanliness in fluid power. In addition, it is logical that the cleanliness of cylinder tubes and pistons is better than the cleanliness in assembled cylinders.
General cleanliness drawbacks in production
After several cleanliness analyses of production process the following drawbacks are found to be quite general:
Fig 6. The measured effect of transporting to the cleanliness of hydraulic valve block.
- Washing machines of components are located in exactly the same area as machine tools. Dirty air affects washed components when they are left on an open transport box beside the washing machine
- The washing machines are accidentally misused when the dirty components, not included in normal production, are washed in them.
- Unfiltered compressed air is used for the drying of components after washing
- Unprotected nipples, couplings, hoses or pipes are waiting for assembling
Component cleanliness services
In TUT/IHA (Tampere University of Technology, Department of Intelligent Hydraulics and Automation) is prepared several component cleanliness services to study and develop both the quality of production itself and the control of quality of components (Table 4).
REFERENCES:
ISO 16232-5. (2007), International Organization for Standardization. Road vehicles -- Cleanliness of components of fluid circuits – Part 5: Method of extraction of contaminants on functional test bench. 18 p.ISO 16232-10. (2007). International Organization for Standardization. Road vehicles -- Cleanliness of components of fluid circuits – Part 10: Expression of results. 19 p., ISO 18413. (2002). International Organization for Standardization. Hydraulic fluid power -- Cleanliness of parts and components -- Inspection document and principles related to contaminant collection, analysis and data reporting. 28 p., ISO 4406. (1999). Hydraulic fluid power – Fluids – Method for coding the level of contamination by solid particle. International Organization of Standardization. Switzerland. 7 p., SAE AS4059E, (2005). Society of Automotive Engineering. Aerospace fluid power – Cleanliness classification for hydraulic fluids. 14 p., Rinkinen, Jari; Elo, Lauri; Kuosku, Mika; Pekkonen, Juuso (2013a). ”Experimental results in Component Cleanliness of Fluid Power”. The 26th International Congress of Condition Monitoring and Diagnostic Engineering Management, COMADEM 2013, 11-13 June, Helsinki, Finland, Rinkinen, Jari; Elo, Lauri; Kuosku, Mika; Pekkonen, Juuso (2013b). ”Current research in component cleanliness of fluid power”. The Tenth International Conference on Condition Monitoring and Machinery Failure Prevention Technologies, CM2013/MFPT2013, 18-20 June 2013, Kraków, Poland