Advancements in Vibration Monitoring of Reciprocating Compressors
Over the last twenty years, stand-alone vibration sensors for reciprocating compressors have evolved from ineffective RMS vibration transmitters to first-generation shock monitoring technology. That technology provided valuable data by shifting from VAC-to-VDC RMS signal processing to impact counting, but had its own set of disadvantages. Second generation shock-monitoring technology has built upon the existing technology to create a solution that is best tailored for reciprocating compressor monitoring.
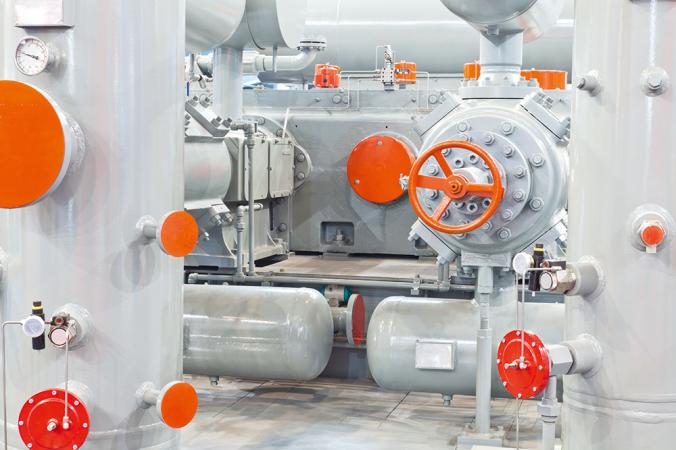
Reciprocating compressors are employed to compress a wide range of industrial and medical gases (ex. helium, hydrogen, oxygen) in order to provide high-pressure, low-volume delivery. They are also highly prone to catastrophic damage when developing faults go undetected and unresolved.
Faults creating errant vibration in reciprocating compressors can generally be classified as mechanical looseness and can include loose, broken or cracked bolts & rod nuts, excessive crosshead clearance, cracked rods and cylinder debris or scoring. The faults typically create metal-to-metal impacts that manifest in vibration data as high-frequency, high-amplitude peaks.
Because faults develop quickly, continuous 24/7 process monitoring has been and continues to be preferred because data can be constantly recorded, trended and analyzed by a PLC (programmable logic controller), DSC (distributed control systems), SCADA (supervisory control and data acquisition) or other online monitoring system. The above-referenced systems can all seamlessly accept a current input signal so a vibration transmitter is ideal.
Ineffective Use of the RMS Vibration Transmitter for Reciprocating Compressor Monitoring
Initially, reciprocating compressor operators selected RMS vibration transmitters as their vibration sensor of choice. These sensors would output a current signal scaled to a specific measurement range (typically measured in velocity). The signal-processing scheme in these sensors was as follows:
- Sensing element producing a high-impedance charge output after being acted upon by a force.
- High-impedance signal is converted into a low-impedance voltage signal.
- AC voltage signal is decoupled from the DC bias voltage.
- C voltage signal is converted into DC voltage signal via RMS (root mean square) methodology.
- DC voltage signal is then subsequently converted to a 4-20 mA current signal.
The conversion of the AC voltage signal to a DC voltage signal is not as simple as averaging the individual AC voltage signal values because, for sine waves with equal positive and negative half cycles, this averaging would result in a non-valuable measurement of zero. Alternatively, the RMS methodology consists of the following four calculation steps:
Divide one cycle (ie. one positive and one negative half cycle) of the AC waveform into many slices, each small enough to represent a constant voltage during the time period.
Square each of those individual constant voltages. This squaring of each individual voltage converts all voltages, regardless of whether originally positive or negative, to positive values.
Calculate the mean (average) of the squared values.
Calculate the square root of the mean. (The result is the RMS DC voltage value.)
For reciprocating compressor-monitoring applications, the RMS process masks the exact high-frequency, high amplitude peaks in the vibration data that are crucial to identify by averaging the area (energy) under the curve. While metal-to-metal impacts create high amplitude peaks in the data, they are simultaneously very narrow curves. As a result, the curves have very little energy and the peaks have very little effect on the averaged RMS DC voltage value. Because of this shortcoming, reciprocating compressor operators moved from typical vibration transmitters to first-generation shock monitoring technology as a more effective monitoring methodology.
First Generation Shock Monitoring Technology
First generation shock monitoring technology shifted the signal processing focus from the existing RMS methodology to impact counting. Impact transmitters based on the technology would measure vibration, apply a band pass filter to isolate frequencies of interest and count the number of impacts occurring above a pre-set threshold level every 2-3 seconds. For each counted impact, the current output would increase by a pre-set 1mA increment from the 4mA baseline to create a building current output.
The technology fundamentally moved away from allowing the direct correlation of the current output to a specific amplitude. Instead, impact transmitters focused on identifying the high-frequency, high-amplitude peaks in vibration data that are caused by the metal-to-metal impacts that are common indicators of developing faults. Operators would set the threshold at the amplitude level that was the boundary between acceptable and unacceptable amplitudes. The output subsequently let them focus solely on the number of impacts occurring at unacceptable amplitudes and build a current output accordingly.
While the technology provided a substantial improvement in effective vibration monitoring for reciprocating compressors, it still did not provide operators all of the data and flexibility that they required. The sensors had three major shortcomings:
- Provided a flat, unchanging 4mA output when no impacting was occurring.
- Compared actual vibration amplitudes to only a single threshold.
- Provided no flexibility to the increment added to the total current output when an impact was identified, regardless of the impact’s amplitude.
Second Generation Shock Monitoring Technology
Second generation shock-monitoring technology, which was patented in 2007, has built upon the first-generation technology by addressing the three major shortcomings. Reciprocating machinery protection sensors based on the technology still measure vibration and apply a band pass filter to isolate frequencies of interest like their first generation counterparts. After that point, the signal processing scheme between impact transmitters and reciprocating machinery protection sensors diverges.
No impacts above the threshold are present: Impact transmitters provide a flat 4mA signal when no impacts above the threshold are present. Reciprocating machinery protection sensors provide a continuous, meaningful current output scaled to peak acceleration. This signal provides valuable trending data as well as confirmation of proper sensor operation to the reciprocating compressor operator.
Comparison of actual vibration amplitudes to benchmark(s): While impact transmitters only compared the amplitudes of the actual vibration to a single threshold, reciprocating machinery protection sensors compare the amplitudes of the actual vibration to two, independently-set thresholds every 2-3 seconds.
Weighting of each impact with an amplitude greater than the threshold(s): Impact transmitters weighted each impact in excess of the threshold at an unchangeable increment of 1mA. Reciprocating machinery protection sensors provide an independent weighting increment for each threshold. Each weighting increment can be field-altered to a value between 0.2-16 mA. Peaks with amplitudes that exceed both thresholds are double-counted in that both the weighting factor for a peak exceeding the first threshold and the weighting factor for a peak exceeding the second threshold are both added to the total current output when such a peak occurs. This allows the sensor to build the current output faster as peaks increase in amplitude. This is essential so that the sensor’s signal can stay ahead of the developing fault and allow the technician time to shut down the compressor prior to a catastrophic failure.
Conclusion
Those stand alone vibration sensors for reciprocating compressors have evolved over the last twenty years as the oil & gas and petrochemical industries place greater emphasis on vibration monitoring as a valuable predictive maintenance technique.
Meredith Christman Product Marketing Manager, IMI Sensors, Division of PCB Piezotronics, Inc.