Using Ultrasound for Electric Power Reliability
Unreliable electric systems not only costs millions of euros in downtime and repairs, they also have the potential to maim and kill.
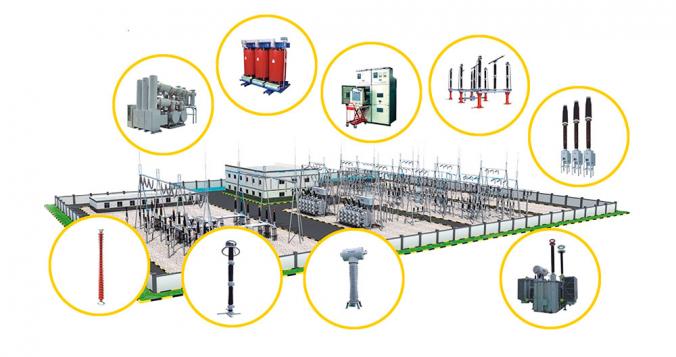
Reliability leaders must remain focused on preserving both physical and human assets. Employees have the right to work in a safe work environment and return home unharmed. Ultrasound technology helps detect fault conditions that can lead to dangerous outages at their earliest stage. It should be a part of every strategic electrical asset management plan.
What is Ultrasound?
There are three categories of sound. Infrasound, Audible sound, and Ultrasound. When we speak about ultrasound we refer to sound which is above the range of human hearing. By technical definition that’s above 20kHz.
The first characteristic is directionality. As we go higher in the frequency spectrum the energy and size of the sound pressure wave decreases. Its ability to travel through a medium over long distance diminishes. This helps us because the likelihood of two or more sound waves overlapping (competing) is less. It also helps us because high frequency sound waves cannot expand or spread through their medium.
There are certain characteristics of ultrasound that make it advantageous for industrial condition monitoring.
The second characteristic that makes ultrasound helpful is its stay at home mentality. It tends to stay where its created. This is great for us because we want a way to quickly identify and pinpoint its origin.
Ut Owns the Apex of the P-F Curve
Ultrasound is considered the first line of defense for finding defects that can lead to asset failure. The first signs of change in the operating condition of an asset are usually indicated in the ultrasound frequencies first. Only after the asset has progressed to a more severe stage of deterioration do other asset condition monitoring technologies begin to play a role. For planners and schedulers, having the largest window of opportunity possible to order parts, plan downtime and allocate labour represents a tremendous advantage.
Heterodyne Principle
Ultrasound instruments work on the principle of heterodyning. Ultrasound detectors detect high frequency sound pressure waves. Using a mixing filter, they translate those waves into representative signals that humans can comfortably hear. What is heard ultrasonically, is heard as a direct representation, audibly. Great detectors do so with crystal clear clarity and provide multiple indicators of condition.
Ultrasound is a FIT
Ultrasound can tell us how FIT our assets are. It is sensitive to defects that product Friction, Impacting, and Turbulence. This is the case for most every failure mode associated with any asset. So if you ever wonder where you can use ultrasound, ask yourself… does it produce Friction? Does it produce
Impacting? Does it produce turbulent flow? If the answer is “YES”, then ultrasound is a FIT to find that defect.
The Eight Application Pillars
Ultrasound is widely considered by most reliability leaders to be the most versatile asset condition management technology. At SDT we identified the primary areas where ultrasound makes your life better and we define these as the 8 Application Pillars. They include: Mechanical, Leaks, Lubrication, Electrical, Valves, Steam, Hydraulics and Tightness.
What is Partial Discharge (PD)?
Partial Discharge is a localized electrical discharge in an insulation system that does not completely bridge the electrodes.
Partial Discharge (PD) is an atomic reaction which, due to the movement of electrons ionizes the air molecules and locations of high stress. This ionization phenomenon splits the oxygen molecule to form ozone and nitrous oxide which in their normal states are generally harmless. But when mixed with water vapour in the air, become corrosive.
Where do we Find PD?
There are many components in your electrical asset portfolio. Substation components where we want to be particularly diligent for PD include transformers, overhead infrastructure also referred to as transmission and distribution systems any joints or termination points on cables, breakers, bus sections, insulators, and surge arrestors in switchgear, and more.
Why Test for Partial Discharge?
In a word: Reliability. Actually, two words, reliability and safety, but reliability leaders know that the two go hand in hand. Reliable facilities are safe facilities. Electrical assets can never be managed with a run to failure strategy.
Partial Discharge is an indication of a developing fault in medium and high voltage insulation and is widely regarded as the best early warning indicator of the deterioration of the insulation system. A weaker insulation system translates to a higher probability of failure.
Testing for the presence of PD must take place throughout the life of the asset. During the design phase, directly after manufacturing as a quality control. During the installation and commission phase, and throughout the serviceable life of the asset.
PD is Destructive
It directly destroys all organic insulation materials and produces by products that form aggressive chemicals which can attack both insulation and conductors. The end result of PD is a full discharge (complete failure) of the insulation system.
What are the Consequences?
Insulation in some electrical equipment is designed to be resistant to partial discharge, but… Switchgear is designed to be PD free so switchgear insulation is NOT PD resistant. When PD occurs in switchgear it is because of a defect. Early detection allows relatively quick and easy repair. But if it is not detected… and eliminated it will eventually bridge the insultation and result in an Arc Discharge. Arcing and in some instances partial arcing, is the flow of electricity through the air from one conductor to another object, which conducts electricity. It is a rapid expansion of gas, causes fires and explosions, is extremely violent, generates extreme temperatures, and therefore the rapid destruction of all equipment connected.
Human Safety
A report published in Industrial Safety and Hygiene News estimated that, on average, there are 30,000 arc flash incidents every year. The report went on to estimate that those incidents resulted in average annual totals of 7,000 burn injuries, 2,000 hospitalizations, and 400 fatalities per year. http://tyndaleusa.com/blog/2018/08/27/how-common-are-arc-flash-incidents/
How Does Ultrasound Help?
Ultrasound is a FIT for so many defects and electrical faults such as Partial Discharge are included because they produce Turbulence with peaks in the frequency range of 40kHz. Directional due to its high frequency, low energy
Allan Rienstra
CRL, Director
Business Development
SDT International