Rotating Equipment Services: A comprehensive, worry-free package for pumps, turbines, compressors, etc.
Many processing plants include rotating equipment that is in continual use and contributes significantly to the enterprise’s productivity. This equipment must be operated in a cost-effective manner and must not break down. To ensure this, Bilfinger offers rotating equipment services covering the entire lifecycle of the systems involved. A project currently underway at the fertilizer producer Yara Porsgrunn in Norway shows how this works in practice.
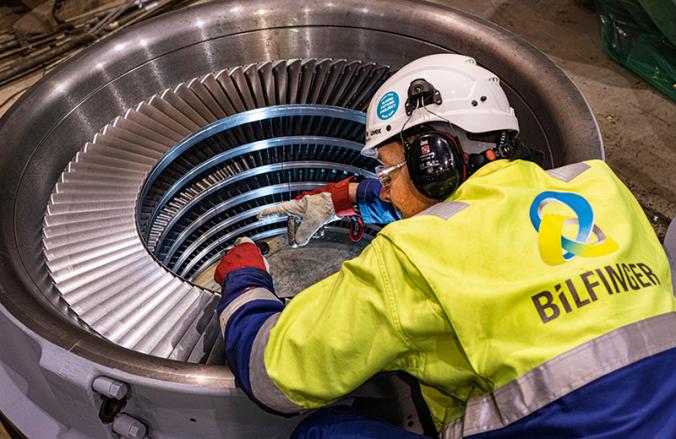
BILFINGER’S NETWORK for the provision of rotating equipment services covers all of Europe and consists of several centers of competence; the intention is to further expand this network in future. It comprises a large number of technical specialists like engineers and technicians and allows Bilfinger’s national companies to share their expertise along with the experiences they have gained with regional particularities.
Customers benefit from having a service provider on call who can offer all the required services from under one roof, across national boundaries and regardless of the type of machinery involved. Bilfinger aims to position itself as a complementary service provider alongside OEMs (original equipment manufacturers).
The target industries in this context are chemical & petrochemical, oil & gas, as well as energy & utilities. Obviously, every plant features different types of equipment. Bilfinger has classified rotating equipment into two categories and has set up a center of competence for each one. The first is “heavy rotating equipment,” which includes turbomachinery, piston compressors as well as multistage high-pressure pumps and gear units. The second is “small rotating equipment,” which comprises standard pumps and drive motors.
In all cases, Bilfinger provides end-to-end support specifically tailored to its customers’ needs, including manufacturer-independent consulting, installation and commissioning of new equipment; maintenance, repair and ongoing optimization during operation; as well as the final decommissioning. Investment phase, installation and commissioning
The lifecycle of a piece of machinery essentially consists of four phases: Its initial acquisition in the investment phase, its installation and commissioning, the operating phase, and the final decommissioning. Each of these lifecycle phases is fully covered by Bilfinger’s rotating equipment services.
During the investment phase, Bilfinger advises its customers as to which equipment will best suit their needs, while offering feasibility and engineering studies along with the planning to be submitted along with the building permit application. If so requested, Bilfinger can also provide the full range of asset management services for small rotating equipment. In this case, Bilfinger offers its customer an equipment-rental pool from which roughly 20,000 devices such as pumps, electric motors or frequency converters, etc. can be leased at reasonable cost.
This ensures the highest possible level of availability, as do comprehensive support services for the repair or replacement of faulty devices – which can be provided in a matter of hours, depending on location.
The arrangement offered by Bilfinger known as the “Value Performance Contract” is unique on the market. It offers customers a guarantee for a respective pump’s availability in return for machines and to alert the competent maintenance team should the monitored parameters deviate from their target range. This allows the maintenance team to intervene promptly and head off any impending damage. One service Bilfinger Industrial Services Norway offers its customers is the evaluation of the vibration signals emitted by compressors and turbines. On that basis, irregular running noises are analyzed and attributed to a specific cause, so that appropriate action can be taken immediately if required. This type of status monitoring protects the machinery involved from unexpected breakdowns.
In Germany, Bilfinger distributes a vibration sensor specifically developed for the monitoring of pumps, and also provides supervision and evaluation services. The optimization and modification of rotating equipment is another field that Bilfinger looks after. Here, the main objective is to realize potential energy-savings – a significant aspect given that energy consumption accounts for about 80 percent a fixed price, along with contractually assured, progressive reductions of the maintenance costs. Bilfinger delivers the desired rotating equipment and provides support services to ensure it continues to be functional over a longer term.
Operating phase and decommissioning
During the operating phase, Bilfinger’s task is to provide detailed maintenance services and regular repairs for the customer’s rotating equipment. Since these services are performed on a continual basis, any long or unexpected downtimes are prevented that potentially could result in huge losses of production.
Upkeep and repair measures of a more extensive nature are planned far in advance and in constant coordination with the customer.
This ensures that any protracted downtimes can be kept to a minimum. Likewise, the developments in the field of industrial automation (“Industry 4.0”) are highly relevant to rotating equipment services, specifically when it comes to prescriptive maintenance. For example, vibration sensors can be used to monitor the status of rotating machines and to alert the competent maintenance team should the monitored parameters deviate from their target range. This allows the maintenance team to intervene promptly and head off any impending damage.
One service Bilfinger Industrial Services Norway offers its customers is the evaluation of the vibration signals emitted by compressors and turbines. On that basis, irregular running noises are analyzed and attributed to a specific cause, so that appropriate action can be taken immediately if required. This type of status monitoring protects the machinery involved from unexpected breakdowns. In Germany, Bilfinger distributes a vibration sensor specifically developed for the monitoring of pumps, and also provides supervision and evaluation services. The optimization and modification of rotating equipment is another field that Bilfinger looks after. Here, the main objective is to realize potential energy-savings – a significant aspect given that energy consumption accounts for about 80 percent of the lifecycle costs of many pumps. Up to 60 percent of these costs potentially could be saved by adjusting the respective pump to run at its optimal operating point.
Technicians from the Bilfinger network analyze the relevant systems and draw on their decades of experience to prepare and implement proposals for technical improvement.
A case in practice: Yara Porsgrunn in Norway
Depending on a customer’s requirements, each service will be provided by a specific team drawn from the network. In Norway, Bilfinger is in a unique position since the center of competence for heavy rotating equipment located there constitutes the largest rove of experience in both onshore and offshore services. One example is Yara Porsgrunn, a Norwegian fertilizer producer running four nitric acid plants, a key input material for fertilizer. These facilities are among the biggest of their kind in the world, with a total output capacity of 1.8 million tons per annum. Bilfinger’s task was to recondition a compressor train during a scheduled downtime, while concomitantly performing a chemical cleaning and oil-flush of the lubricating/ hydraulic system. The compressor train consists of a steam turbine, a centrifugal compressor, a gear unit, an axial compressor and an expander, all of which were coupled to a drive shaft.
The biggest challenge in this case was to carry all out the activities simultaneously in order to keep the stop time as brief as possible. The work was performed by roughly 3 engineers and 50 technicians supplied by Bilfinger, who worked as a team with Yara Porsgrunn with added assistance from MAN Energy Solutions as the OEM. A local Bilfinger workshop manufactured a number of replacement parts and was able to perform repairs on site. This was a significant advantage, since the delivery timesof the OEM were too long.
Thanks to Bilfinger’s seasoned experts, the project ran smoothly. Despite the unexpected discovery of worn-out parts, the cheduled downtime of three weeks was only slightly exceeded as a consequence of the flexible approach taken by Bilfinger and its technical expertise.
Rotating equipment services in the future
The end-to-end package offered by Bilfinger bundles all the required services under one roof, while leaving them customizable to each customer’s needs. The advantage this service delivers over OEMs is that it allows customers to obtain independent advice and to tap into expertise transcending that of any one manufacturer.
Compared to its competitors in the field of rotating equipment, Bilfinger also is able to deliver a greater amount of qualified manpower. Roughly 200 technical specialists for heavy rotating equipment currently belong to the network.
In other words, Bilfinger is in an excellent position to handle upcoming developments on the market, particularly in view of the fact that cooperation models will become increasingly important in future: Global customers are looking for providers who are able to offer services of consistently high quality across the globe, while ensuring that these services are steered centrally. The demand for the rotating equipment services offered by Bilfinger as a leading international industrial services provider is certain to grow steadily in the years to come – also because customers need to fill the prevailing shortfall in skilled personnel with the required expertise in rotating equipment.
Bernardo Sequeira, Business Development Rotating Equipment, Bilfinger SE;
Øystein Haldorsen, Department Manager, Rotating Machinery, Bilfinger Industrial Services Norway AS.