Operator Essential Care (OEC) Routes
It is said that, “Maintenance is Managed by Managing Backlog”. Truer words were never spoken. Improvement in the management of maintenance leads to lower maintenance costs, more operating hours, increased safety and higher equipment reliability. So, the question is, how do we generate backlog to improve the management of maintenance?
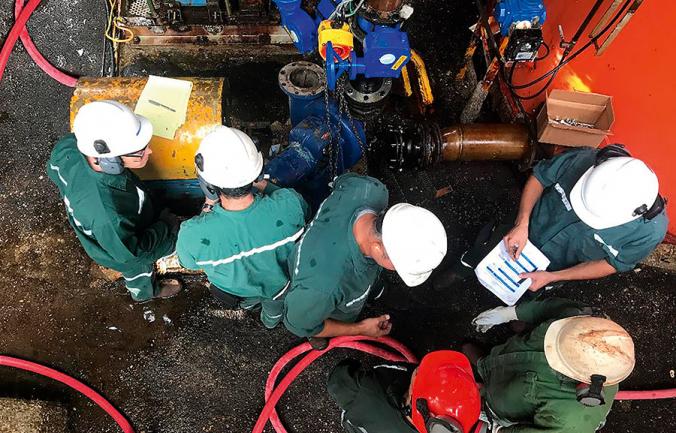
The simplest definition for Backlog is – work that needs to be done in the future. Often an organization does not have its “True Backlog” identified and documented. We usually know this because of the amount of Reactive Maintenance Work that is taking place. We also see this when the Open Work Order List contains very little work that would fall into the category of Backlog, that is, work (corrective) that needs to be done in the future. How can the organization address the problem?
We begin with the Preventive Maintenance (PM) program, where OEC can be an integral part. This is where the problem as to why there is little to no Backlog is addressed. The first point of contact for detecting problems early resides with the equipment operators. It should be no surprise as to why equipment operators are the first line of defense in early detection; they are tending to the equipment every hour it’s in operation. Detecting problems early and reporting them gives maintenance the opportunity to plan and scheduled the corrective repairs.
You may be wondering how to engage the operators to do OEC. There are 3 key steps to take:
- First, build (document) the Operator Essential Care (OEC) routes.
- Second, establish the training required for the operators to be able to detect these problems early.
- Third, determine the KPIs that should be used to measure the results of the OEC routes.
STEP 1 – Building the OEC Routes
A Best Practice PM program consists of these elements -
PM – Preventive Maintenance
EC – Essential Care
CM – Condition Monitoring
• Objective Measurements
• Subjective Measurements
Essential Care (EC) – For example; Lubrication, balancing, alignment, oil, filters, adjustments, cleaning, operating correctly – The things you do to Prevent Failures
Condition Monitoring (CM) – Objective methods such as Vibration, Thermography, Oil Analysis, together with subjective checks, meaning, look, listen, feel, smell, etc.- CM are all the things you do to Detect Failures
Although various disciplines (Mechanical, Electrical, instrumentation and operations) are accountable for the many tasks associated with a comprehensive PM program, it is with Operators that this list of tasks can begin.
Operators are responsible for operate the equipment correctly in order to avoid equipment failures. This element of OEC is often forgotten. This article focuses on the inspection routes, but keep in mind correct operation is often the most important factor operations can contribute towards equipment reliability.
Operators make routine rounds on the equipment in their area(s) of responsibility and it within these rounds where you can add certain PM tasks to the operator’s list of duties. These PM tasks are normally very simple, easy to do and require very little training. But what exactly are these tasks and how are task lists developed?
First – Pick an “area” for a route(s)
The “area” would be associated with an operator’s area of responsibility. Within the area are many assets consisting of different components. It is the components that you want the OEC tasks to focus on.
Example: For a Bleach Plant in a Pulp Mill consisting of many floors, the areas may be broken down by floor. In a Paper Mill, the areas may be broken down by function. A paper machine, may be broken down into the wet end, the dry end, and the winder.
Second – Break each asset in the “area” down into components.
This exercise is the equivalent of breaking the elephant down into bite-sized pieces. It is not the equipment that fails, it is a component that is a part of the equipment that fails and causes the equipment to stop.
For example: A conveyor belt will be part of an OEC route. To begin breaking it down into components, have a diagram of the entire conveyor and identify everything you want to include as part of the OEC route. One area would be the “drive (or head) pulley” this would include the motor, gearbox, couplings, pulley, pulley bearings and holdback. Another area would be the “conveyor structure” which might include the idlers, walkways, the structure itself, take-up, etc. Continue this exercise until all of the components are identified. The point is, to not miss anything in the “area” you have identified as being part of the OEC route. You might also refer to the Equipment Register or Functional Location and the hierarchy in your CMMS. And finally, confirm the list of components by visual verification.
Third –Build a spreadsheet where you can breakdown the assets into their various components.
After breaking each asset down into its components, list these on a spreadsheet. The list of assets should be in a logical order as the operators go from one asset to the next. There will be OEC tasks associated with each component. So, leave some lines on the spreadsheet for these OEC tasks. This is more fully explained in the next step.
Fourth - Populate the spreadsheet with the OEC tasks for the components
Now it’s time to decide the tasks operators will do as a part of their OEC routes. This is where a facilitator or an appointed “team leader” will assist leading what is best described as a very tedious exercise in populating the spreadsheet. Don’t underestimate how difficult this might be. Expect a great deal of discussion as you address each component.
A time saver is to address common components ahead of time. So, if the component is an AC motor, the tasks that an operator would do is decided early on and a list of those tasks are used each time that common component comes up on the list. Here is a short list of common components in a pulp mill that could be addressed early, and “templates” made for these and their associated OEC tasks –
- AC Motors
- Centrifugal Pumps
- Couplings
- Gear Boxes
- Agitators
The OEC tasks are often executed more frequently, non-intrusive and take a very short period of time to execute. But what is documented for the tasks are very important because these become the actual task descriptions that the operators will see. For example –
- “Check Motor” is a poor task description
- “Check the temperature of the motor at the mid-point (Black Target) of the housing” is a much more descriptive task.
It is vital tasks are written descriptively so the operators will know exactly what to do. Many checklists contain brief and inadequate descriptions for the tasks that need to be executed. The example below shows a few inadequate task descriptions from a PM checklist.
The task descriptions must be written in such a way that no matter whom the operator is, no matter what they know or don’t know, the task description is detailed enough so there no reason for the operators to not do an adequate job on each respective task. These tasks are usually done on-the-run while the equipment is operating. That is, no shutdown of the equipment is required to execute the OEC tasks.
The most difficult part in building the list of tasks for the operators is deciding where to draw the line on what is included in the OEC routes and what tasks others will do as a part of the overall PM program. These other tasks would be executed by the mechanics, electricians, instrument techs and contractors. These tasks are usually more technical in nature and/or require that the equipment is shutdown or deenergized in order to complete the tasks.
- Frequency – How often you want to execute each particular task
- Frequency Unit – This is normally Date-Based such as daily, weekly, monthly, quarterly, annually. For OEC tasks, daily and weekly are the most often used frequency units.
- Resource – Simply the Craft type and skill set required to do the task. For OEC tasks, this would always be the Operator.
- Route – Answers the question, can the task be listed as a part of a Routine Route to be executed on a regular basis? It serves as a check and balance for the execution of the task.
- Shutdown – Is it a requirement that the asset be shutdown to execute the task?
- Existing PM – Does the task currently reside on any existing PM, for example in mechanical, electrical or instrumentation PM’s. If so, it needs to be decided whom does what task to balance the PM program.
- Spare Strategy – Is there a strategy in place that allows for the replacement of the part/component should it be necessary? If the answer is no, ask the question, should there be? This would not normally be required for any OEC task.
- Reference Document – This field is to show the location of any reference documents that may be in a Technical Database. IDCONs Condition Monitoring Standards are often referenced here. An example is shown below –
Fifth – Produce the PM routes and checklists
The spreadsheet makes it very simple to build the actual routes and corresponding checklists. The data can be filtered so that it is sorted as desired and then the routes are created with all of the tasks for the assets.
Sorting may be by the operating floor, the area, the equipment, the frequency, etc. It can be sorted any way that is desired to see the inspection points in a list. This can be a very long list of tasks for the OEC routes, so it requires a strategy for deploying those tasks.
For example: The OEC spreadsheet for Weekly on-the-run tasks has 210 inspection tasks. If this was given to the operators all at once they might be overwhelmed. But a strategy to break it down by day and shift, assuming 3 shifts per day, makes this only 10 tasks per shift.
Next, address how the tasks will be communicated to the operators and how they respond when they have information to report back. This may be communicated on a hard copy form or it may be addressed with a data-logger. Either system works but it is a big decision.
For hard copy formats, a “Template” needs to be created for the checklists. For a data-logger type system there are several options. But whichever system is used, they both need to have a good way to handle the feedback from the operators. It is the early detection and reporting of a problem that is critical.
STEP 2 – Training Operators for OEC Routes
Training operators to execute OEC routes is usually very simple. The main point of the training is operators understand the importance of detecting problems early. And once a problem is detected, then it must be reported ASAP.
First – Inspection Tools
Depending on where the line was drawn on what the operators will do on an OEC route, you might have some inspection tools involved the need to be procured and that the end-users, in this case the operators, are trained how to use them. The inspection tools normally used in OEC are a vibration pen and a thermal recording device. The training on how to use these devices is usually very simple and is often provided free from the OEM when they are purchased. For a more in-depth Essential Care and Basic Inspection training, IDCON has training designed for Operators.
Second – Running the Routes
Running the routes is one-on-one training delivered by the trainer walking the route with the trainee. It is not only about how to execute each task listed but it is more about having an awareness of everything going on around the person while running the route. This training can’t be effectively done in a classroom environment.
Third – Report on Findings
Detecting problems early is the real pay-off for doing OEC routes. When a problem is discovered then it must be reported. There must be a clear line of communication for getting these problems in the backlog and in the most efficient manner possible. The criticality of this step cannot be overstated.
STEP 3 – Measuring & Managing the OEC Route Results
The single most important measurement of how well the OEC routes are being executed is measuring the number of work requests or work notifications written as a result of the execution of the OEC routes. And this is not just when a problem is found that is tied to one of the OEC tasks. It is the early detection of any problem reported as a result of executing an OEC route. Most CMMS systems have a code that is put on the work request or work notification when it is created that signifies that it was created as a result of an OEC or PM route.
The other KPI that should be measured is the OEC Route Compliance. It simply measures if the scheduled routes are being executed. Some CMMS systems can measure this for you and in other systems it may be a manual calculation.
Operations management needs a workflow in how to manage and measure OEC. This typically includes a manager’s meeting where the workflow is agreed upon followed by on-the-job coaching to ensure that the practices are followed in the field.
IDCON INC is a consulting company specializing in the field of reliability and maintenance management. IDCON has been an On-the-Job trainer, coach and facilitator of the assessment, development and implementation of PM programs (Including OEC) for over 40 years worldwide in manufacturing and processing organizations.
When you are ready to build your OEC Program and need a partner to help you focus on the development and implementation of your program contact IDCON INC.