The Skills Gap and the Covid 19 Impact
For years, especially in the United States, we have seen a widening gap between the need for skilled trades and the inflow of young candidates to fill the positions. We have seen a general bias in our education system, away from technical training and skilled trades, leaning strongly toward 4 to 6-year degree paths.
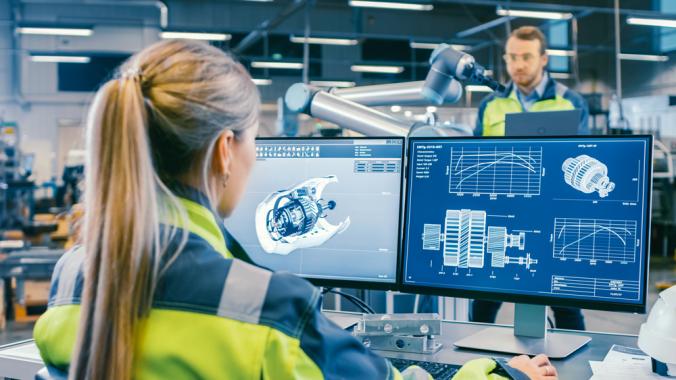
While the 4 to 6-year degree is clearly the correct choice for many, for some unexplainable reason, technical training has been treated as a lesser alternative path, if you can’t cut it in the college degree program. It is a strongly-held belief that if you wish to succeed in a real career, you need a Bachelor’s degree or higher. We need only to look to European countries, like Germany, to see examples of skills development paths that are highly respected as craftsman and essential for society.
When you consider the role of skilled trades in society, skilled workers are responsible for many essential activities, on which society is dependent to function. How would a surgeon perform amazing surgery without an operating room built by skilled construction workers, HVAC technicians and electricians, being maintained by facilities maintenance? The backup generators, oxygen generators, filters, elevators, and all other key equipment are maintained by skilled trades. The stark reality is that the highly educated surgeon is required for the surgery, but all of the infrastructure around the surgeon is required as well.
According to NCTAP’s website ( https://nctap.org ), a partnership between local businesses and local community colleges for skilled trades apprenticeship:
“In most cases, apprentices, due to their superior education, assume managerial responsibility early in their careers. Not surprisingly, most NCTAP partner businesses were founded by former apprentices; some are world leaders in their field...
DESIGN 85%
MACHINE LEARNING 90%
ELECTRICAL 78%
FABRICATION 93%
ENGINEERING 85%
AUTOMATION 94%”
It turns out that many Plant Managers, Plant Engineers, Maintenance Managers, Supervisors, and small business owners began their careers as skilled trades, even further expanding their career opportunities and income potential.
While the college experience is a developmental experience in many ways, and we do need accountants, business leaders, legal counsel, etc. there are other career choices (skilled trades) that can lead to equal, if not higher pay, with less incurred debt. Imagine an opportunity, whereby your employer pays for your college degree (associate) instead of you incurring student loan debt, taking the same 4 years to complete, earning $15-$18 per hour during your hands-on training, resulting in a $40k-$100k year job, debt-free. I just described an apprenticeship program.
You would think that students from high school would be flocking to such a programs, to the skilled trades, but you would be wrong. In the Raleigh, N.C. area there is a program called NCTAP, with similar programs in Charlotte, N.C. and Franklin County N.C. But the number of students that consider this a valid career choice is relatively small. I attended a large pharmaceutical plant tour with potential apprentices on a Saturday, and all senior leadership was present and pitching their apprenticeship program. This shows how important this is to the plant. The inflow of potential skilled trades candidates is insufficient to maintain the workforce required.
If we look at the other end of the spectrum, many current skilled trades are either eligible for retirement or soon to be eligible. According to the labour department, the average age of skilled trades is 56*. With looming retirement possible for these skilled trades, the need for a pool of apprentices to understudy, and ultimately replace, the retirees is large.
In addition, while this discussion has been ongoing for several years, Covid-19 has introduced some new twists and turns to the discussion. First, it is likely we will see increased retirement from the aging skilled trades group, due to Covid-19 exposure risk. If a skilled trades employee is at higher risk due to age, underlying health conditions, or increased exposure at work, this could accelerate the consideration of an earlier retirement. Second, Covid-19 has accentuated the digital skills gap.
Very quickly, almost overnight, large groups of our society have had to adapt to digital interaction; working, meeting, learning, and teaching. This exposes the gaps in digital literacy. It reveals the fact that many of us have “fragmented” understanding of our digital tools. We might be familiar with our phone or Facebook, but have no proficiency in Word, Excel, Zoom, Teams, remote network access, or security, and lack a comprehensive knowledge of integrated computer systems. A phone is no longer just a phone! This lack of knowledge and the social distancing currently required increases the frustration of the daily work routine and exposes a new, important, skills gap, potentially leading to accelerated retirement.
What can we do to help close the gap? How can we make a difference? First, we have a marketing problem. Manufacturing and skilled trades are not viewed by our youth as premium career opportunities. This starts at home, with your children or grandchildren. We must view trades as noble, sought after, high paying professions. Thanks to Covid, we know that “essential workers” include electricians, mechanics, plumbers, machinists, auto technicians… skilled trades!
Next, schools must adopt a positive message around the skilled trades. High schools and Community Colleges must educate teachers and counsellors around the value of skilled trades. Recently I was introduced to an apprentice that was involved in a similar program to NCTAP. He was apprenticed at work, learning a trade, and was sent to a local community college by his employer, working on his associate degree. His college guidance counsellor challenged him one day “I know this machinist trade thing is ok for now, but what are you going to do for your “real” career?” This is exactly the wrong message.
Finally, there are opportunities to engage local and federal governments to support change. There are currently (in the U.S.) grants available to help with training and skills development. While much focus has been on Covid-19 funding as of late, there are several acts in congress to help support skilled worker development. Due to my involvement with The Society for Maintenance & Reliability Professionals (SMRP) I recently attended a Business Leaders United (BLU) virtual fly-in to Washington D.C. The two-day meeting was focused on discussing, with state representatives, the need for skilled worker development. We met with representatives of
Senators around the country to represent how businesses need this support. I was especially struck by Senator Virginia Foxx, of western N.C. She has her doctorate in education, but has strong passion around supporting skills development in the U.S. She shared a story about her brother’s success, starting as a carpenter. She shared that he has incredible skill, creativity, and intelligence, humbly claiming it was greater than her own intelligence. It was inspiring to hear a woman of such amazing accomplishment support skills, not just in word, but action. Although Covid-19 issues have been the focus of legislation in early 2020, there is pending legislation designed to help skilled trades, that if approved would increase funding for skills development.
Proposed changes to the Pell Grant would allocate funds not only to higher education, but to skilled worker development. The College Transparency Act would increase visibility of a specific school’s data on completion and post-college outcomes of degree programs.
Finally, I would share that one of the key “aha” moments for me was a discussion with Senator Burr’s office on automation, robotics, and artificial intelligence. We were talking about how people have feared for years that technology would eliminate jobs.
We were discussing the increased need for skilled trades with increased automation. I was struck with the thought that for all of our fears regarding automation/industry 4.0 changing our workplace, IT WAS A VIRUS that caused the most significant, rapid change to manufacturing in the last 100 years.
These are certainly challenging times, but I am confident that we will adapt to our changing environment, find creative ways to close the skills gap, and face whatever challenges lie ahead.
Gregory L. Folts,
President/ CEO,
Marshall Institute,Inc.