The Power of Reliability Engineering
Reliability Engineering brings together the required asset utilization and the task setting maintenance budget. It also has to fulfill the SHE-requirements as the capital investments for life-time extension.
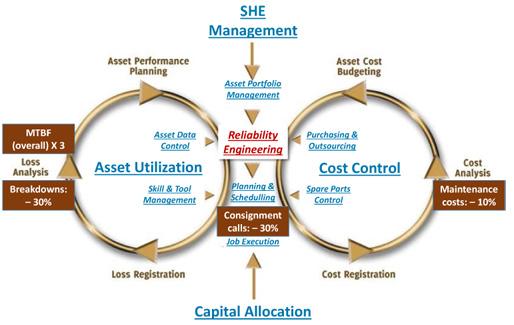
A criticality ranking, supported by a management validated risk matrix focuses the activities of Reliability Engineering on the most critical equipments to pursue the highest added value.
Rendac in Denderleeuw and Sonac in Ghent (Belgium) are both part of the Darling Ingredients International Group. Both companies collect animal residues and process these to grease and meal. The end-products of Rendac are being used as safe and sustainable biofuels, whilst the products of Sonac are being reused within various other markets such as animal nutrition.
Reliability Engineering powered the performance of Rendac and Sonac: the overall Mean Time Between Failure (MTBF) increased threefold; breakdowns and consignment calls reduced by 30 percent and maintenance cost reduced by 10 percent. In particularly the performance of the Technical Department became transparent by using a standard set of KPIs. These KPIs are reviewed periodically by the various company stakeholders and used to steer the maintenance performance. In addition there are several KPIs available for Reliability Engineering, which are used as input for analysis.
To achieve the above mentioned results there was a need to change the company culture and organization. These changes were supported by implementing the VDM Process Map. The VDM Process Map describes all maintenance competences (including process workflows), explains the agreed upon (new) processes in detail and defines roles and responsibilities accordingly. One of the outcomes was to assign a Reliability Engineer to take responsibility for executing the Reliability Engineering process.
The Reliability Engineering process is based on the VDM Reliability Engineering Roadmap. An important aspect of the roadmap is the continuous improvement loop that is integrated into the process. For the most critical equipment, Failure Mode & Effects Analysis (FMEA) have been performed to define the maintenance concepts, plans, tasks and the essential critical spare parts and their stock levels.
Asset Data Control and the support of IT-system were equally important for the success at Rendac and Sonac. In order to enable Reliability Engineering Analysis, correct asset based data is needed such as an asset breakdown structure, breakdown data and asset specific failure modes.
An IT-tool is indispensable to register for example the asset breakdown structure, maintenance plans, task lists and spare parts as well as to capture all data from executing the maintenance work using work orders, registration of losses and registration of costs. Within Rendac Denderleeuw the EAM-tool (JD-Edwards) was optimized. Within Sonac Ghent a new implementation of JD-Edwards was performed.
To realize sustainability a periodical self-assessment supports Rendac and Sonac. It compares the current way of working with the agreed on best practice processes as described by the VDM Process Map.
We can conclude that Reliability Engineering proved to be a sound basis for bringing together asset utilization requirements and task setting maintenance costs by focusing on risk-based analysis of critical equipment. Supported by well described maintenance competences, IT-tools and asset data, sustainable performance improvements and cultural changes are realized.
● MTBF (overall) x 3
● Breakdowns -30 percent
● Consignment Calls -30 percent
● Maintenance Cost -10 percent