Wireless Monitoring for Critical Oil and Gas Assets
One of the greatest challenges in the oil and gas industry is ensuring the reliability of tens of thousands of assets in remote locations around the world.
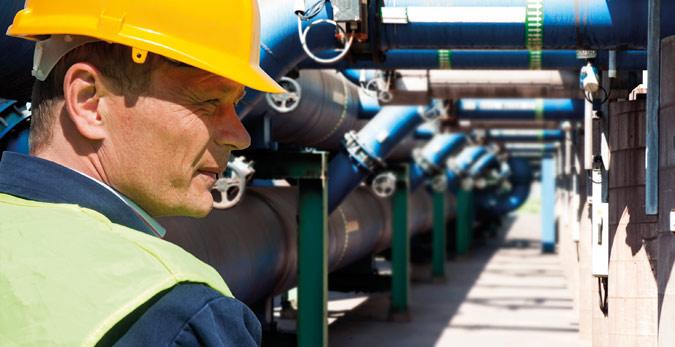
Most of the manufacturing companies build and operate their facilities in areas in or around cities that tend to have an abundance of skilled workers, technicians, engineers, and resources. The oil and gas industry can have assets hundreds of kilometres from civilization and hundreds of kilometres from shore.
Understanding the challenges of operating and maintaining assets in these remote locations requires a thorough understanding of the inherent designed reliability of your equipment and how the environment and context in which you operate the facility can have a direct adverse effect on its reliability and adherence to health, safety, and environmental standards. Add to this the issue of spare parts availability and that the cost to carry these parts must be kept to a minimum that most manufacturing facilities could never tolerate, and the result is a nightmare that oil and gas Operations and Maintenance Managers deal with on a daily basis.
So how does one address this perfect storm of operating and maintaining these assets far from the comforts of civilization in a way that ensures safety and reliability?
One partial solution has been to schedule planned outages or turnarounds where the equipment can be overhauled or replaced based on risk and failure history. While this strategy does an adequate job of addressing equipment impacted by wear-based failure modes, it falls short in addressing the far more likely random-based failure modes.
The reality here is that if you want to ensure the safety and reliability of assets operating in remote locations, you must develop a complete maintenance strategy that includes the use of some of the most advanced predictive technologies that will continuously monitor your equipment for all likely potential failure modes.
We recently worked with a group of oil and gas experts to perform a Reliability Centered Maintenance (RCM) analysis of two critical assets located on offshore platforms.
In analyzing the equipment and controls, the team identified over 250 failure modes, 92 percent of which were random-based.
While an RCM purist might find some comfort in these numbers, the average Maintenance and Operations Manager should pause and take note. The Preventive Maintenance (PM) you have been trying to complete will, at best, only resolve 8 percent of the failure modes associated with these assets.
Failure Mode Challenges in Remote Locations
Our client who was spending thousands of man-hours trying to complete PM inspections that had grown over a period of time in an attempt to mitigate random-based failure modes that result from a lack of well written job plans and precision maintenance techniques. If your company is at all like our client, then you may in fact be making matters worse by inducing infant mortality through human error. The fact of the matter is that a large percentage of offshore or remote equipment will be classified as critical assets; if you are looking to mitigate some of the more significant random-based failure modes, you need to look for high tech solutions.
While a large percentage of the assets we analysed had failure modes that were electronic in nature and can be greatly reduced and mitigated through eliminating the enemies of electricity and a sound consequence reduction strategy, it is the failures associated with the rotating components that result in extended periods of downtime with little more than a moment’s notice. One minute the compressor is working fine, and the next it shuts down due to high bearing temperature.
In an attempt to apply a condition-monitoring approach to the identification of issues within these critical pumps and compressors, facilities have tried to monitor vibration and lubrication at various intervals, often employing temperature monitoring as a trigger for needed corrective action. The challenge here is that they are looking at the result of the failure mode and not always focusing on early warning signals, which means they are looking at the tail end of the failure curve. This is basically a “Watch Out” warning and does not allow ample time to plan, schedule, correct, or eliminate the failure with a proactive maintenance approach.
Condition-Monitoring Challenges in Remote Locations
While those of us who specialise in the various disciplines of condition-monitoring (vibration analysis, airborne ultrasound, lubrication analysis, and thermographic imaging, to name a few) have had tremendous success with detecting potential failures for rotating equipment, the challenge created by equipment in remote locations is that the technologies, in most cases, still give only a point-in-time sample of the condition of the equipment.
Collecting Predictive Maintenance (PdM) data of offshore assets at regular intervals is a challenge on its own; environmental conditions and operating schedules can make it difficult to achieve even 70 percent route compliance. Combine that with the safety issues of being anywhere near some of these massive rotating assets as they operate, and applying traditional vibration analysis techniques is difficult, if not impossible. The equipment is loud, often surrounded by guarding and squeezed into tight locations to conserve space; its bearings and gears are encased in housings that sink heat away; and thermographic imaging is sometimes no longer a viable option. With all of this taken into consideration, some oil and gas companies have begun to question the effectiveness of traditional route-based PdM.
Considering all of the above listed issues, one might attempt to install one of the listed technologies permanently with the hopes that a continuous signal might detect enough vibration, noise, or heat to indicate potential failures, but this requires a large investment to install all the necessary hardware and wiring, adding as well another sizable group of potential failure modes.
High Tech Assets Require High Tech Solutions
One of the things we have learned in more than three decades in this business is to never tell a group of dedicated CBM Analysts that it is impossible to detect potential failures on any piece of rotating equipment because they will figure out a way to make it happen.
From the first RCM analysis we performed on offshore assets in 1998 to the latest analysis less than a few months ago, we heard the standard answer:
– While it would be nice to apply continuous monitoring of one or more of the technologies, we struggle with just how well this would work with our equipment.
In 2014, we can now say think again!
Assembling a team of CBM experts, we took a very detailed look at the technologies we thought were best suited for detecting potential failures of remote rotating assets. We also knew we could permanently install sensors in a way that would allow us to monitor the equipment on a near continuous basis and not interfere at all with equipment performance. The equipment would have to work with a wireless transmitter that would be capable of sending information from multiple sensors on as many assets as the customer wanted to monitor.
The result is a system that uses data from two proven condition-monitoring technologies and allows the customer to set up asset-specific analysis parameters and alarm bands based on vibration and contact ultrasound emissions. Also add in the ability to tie in process monitoring information such as temperature, pressure, levels, and speed, which lets us quantify mechanical condition and operating context to gain a true understanding of asset health. Couple this with simultaneous multi-channel data acquisition, speed, amplitude, and process triggers and you get consistent repeatable data for trending and analysis.
Utilizing the comprehensive data available with this monitoring solution allows for the earliest possible notification of issues developing, which will allow ample time for proactive initiatives and focuses on root cause problem identification.
In testing the system on live equipment last year, the data thus far indicates we now have an on-line solution to detect nearly all of the failure modes associated with the rotating assets. Even more encouraging, the system is easy to install. One can be up and running in a matter of hours, sending signals that give a clear indication of asset health.
About the Authors
Doug Plucknette is a Principal and the RCM Discipline Leader for Allied Reliability Group, creator of the RCM Blitz® Methodology, author of Reliability Centered Maintenance using… RCM Blitz, and co-author of Clean, Green & Reliable. Doug has been a featured speaker at conferences around the world and enjoys training and mentoring people in reliability tools and methods. www.rcmblitz.com
John Trulli is one of Allied Reliability Group’s technical experts in both the Reliability Engineering and Predictive Maintenance fields. He is a Subject Matter Expert in CBM program development and application, and as such, he is a frequent speaker and author on the topics of condition-monitoring programme optimization and the blending of different technologies. Throughout his career, he has performed all facets in the development, application, operation, and consulting of Best Practice failure mode-based maintenance and reliability program applications. Learn more about the services Allied Reliability Group provides by visiting www.alliedreliabilitygroup.com