Towards Predictive Maintenance
It is critical in the fields of maintenance and reliability, to have the proper tools in order to aid better decision making regarding the health of the facility’s assets. Ultrasound technology continues to enhance predictive maintenance, equipment reliability, and energy conservation applications.
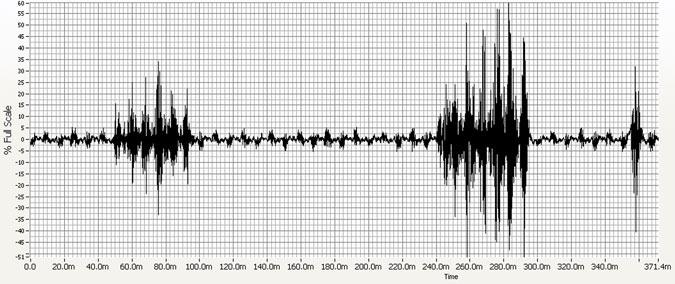
Today’s maintenance departments are continually being asked to do more. Unfortunately, in most cases, they are being asked to do more with less. Maintenance is all about getting the most life out of an asset as efficiently as possible. It is also imperative that we begin to move away from reactive maintenance to performing more predictive or condition-based maintenance tasks. Airborne and structure-borne ultrasound is a great place to start.
In the early days of airborne and structure-borne instrumentation, most users simply kept an instrument around for when they needed something to use to look for leaks. The first instruments in use were simple analogue instruments that were used for “search and locate” applications such as leak detection. Through the advancement in ultrasound instrumentation and software, there were more users of the technology and new applications were discovered. Ultrasound is now considered the perfect complimentary tool for other predictive maintenance technologies such as vibration analysis and infrared thermography. There is also an increase in the number of individuals who are using ultrasound as a first line of defence to predict faults and failures in rotating equipment and electrical inspections.
Simply put, the instruments are listening devices. Airborne and Structure-borne ultrasound instruments detect sounds that cannot be heard by the human ear. Average human hearing detects sound in the 16 to 17 kHz range. Ultrasound instruments listen for and detect sounds that are in the range of 20 kHz and above. The instruments actually listen for sounds that are above the threshold of normal human hearing. Ultrasonic sound waves are high frequency, low energy waves that are received by the instrument. The instruments then change or heterodyne the high frequency sound wave into an audible sound that is heard by the user through the headset, which is plugged into the instrument. Since ultrasonic waves are high frequency and low energy, sources of ultrasound can easily be located amidst all of the ambient noise in a typical industrial facility.
The advancements that have been made in ultrasound instrumentation have been groundbreaking. UE Systems’ latest model, the Ultraprobe 15000, is a good measure for just how far the instruments have come. This instrument has a large, colour, touch screen display, onboard spectral analysis, onboard sound recording, built in digital camera, and spot radiometer for taking temperature. The available data management software is used for creating predetermined locations to download readings for trending. Detailed reports can be generated through the software such as a compressed air/gas spreadsheet that will show potential cost savings and volumetric flow loss from an air or gas leak survey. Spectral analysis software is also available. This allows the inspector to play back sound files that have been recorded directly onboard the ultrasonic instrument. Views include both the FFT and Time Wave Form.
Proven Technology
There are two main sources of ultrasound. The first is turbulence. Turbulence is created from something that is under high pressure that is trying to get to lower pressure (Figure 1). An example of turbulent flow is when a compressed air or gas leak that is under higher pressure is trying to exit through a small crack or orifice to atmosphere, or lower pressure. Turbulence is also created where there is a vacuum (Figure 2). The sound that is created where there are vacuum leaks will be less though, since the sound is being pulled into the low-pressure side.
Turbulence is also created when there are electrical disturbances such as corona, tracking, and arcing. Corona for instance has a steady “buzzing” sound that is produced from the air ionizing around a connection of 1000 volts and greater. At 1000 volts and up, air actually becomes a conductor. Therefore, corona will only be detected in electrical components of 1000 volts and greater. During the ionization process the molecules are vibrating and bumping into each other, thus creating turbulence.
The second source of ultrasound is friction. There may be either too much, or too little friction. An example of too much friction is in an over lubricated bearing. As more grease goes into the bearing housing, there is an increase in pressure, and the bearings are working harder to turn through the increase in lubricant. The increase in friction creates a roaring sound heard through the headset.
There would also be an increase in the decibel level indicated on the instrument. An increase in friction creates more sound. “Rough” or “Scratchy” sounds may be an indication of impacts or a rolling element failure where the rolling element is sliding against the housing instead of rotating. “Cracking” or “Clicking” sounds are usually the result of bearing failure. An actual determination of a bearing fault can be determined by actually recording the sound with an ultrasonic instrument that has on-board sound recording, and then playing the recorded sound on spectral analysis software.
Typical Applications
There are two main application groups for ultrasound. Airborne ultrasound applications include compressed air & gas leak detection, steam leaks to atmosphere, and vacuum leaks. Airborne ultrasound has also been used for specialty applications such as wind noise and water leak detection in the automotive and aircraft industry, and for quality checks in vessels such as fuel tanks, propane tanks, and autoclaves.
Ultrasonic leak detection continues to be the most widely used application for airborne ultrasound instruments. This is mainly because of its ease of use and a very quick payback when leaks are found and then repaired. Usually, enough leaks can be found during an initial survey that the potential savings will more than pay for the instrument. The cost is based on the pressure where the leak is located, the decibel level indicated on the instrument once the leak is located, and the cost per kilowatt-hour of electricity.
As an example, a 60dB leak at 100psi, at a cost per kilowatt-hour of 0.06 cents results in a cost of approximately $450 per year for just one air leak. A compressed air and gas spreadsheet is available for easy reporting and trending of air leak surveys. This spreadsheet can also be generated through UE Systems’ Ultratrend DMS software. Leak survey data is stored on board to a digital Ultraprobe, downloaded into the software, and then the compressed air survey spreadsheet is generated.
An airborne ultrasound application that has seen a tremendous increase in usage over the last few years is for electrical inspection. Corona, tracking, and arcing can easily be detected with ultrasound instruments. Airborne ultrasound can be used for low, medium, and high voltage inspections. Corona, however, will only be detected in components that are at least 1000 volts.
Corona is heard in the headset as a steady buzzing sound. Tracking can be described as having a more intense “Bubbling”, “Frying”, and “Popping” sound. Tracking would commonly be found in cracked insulators, loose connections, and where there has been a breakdown of the insulating material. Arcing has very distinct sudden starts and stops of energy and erratic bursts of electrical discharge. Actual confirmation of these conditions is best carried out through spectral analysis and not just based on what the inspector hears in the headset. The left screen shot is of corona seen in the FFT (Figure 3). The right is of arcing as seen in the time wave form.
The second application group is structure-borne ultrasound. Structure-borne ultrasound applications include rotating equipment such as bearings, motors, and gearboxes. Premature faults can be detected early when using structure-borne ultrasound on rotating equipment. The P-F Curve (Figure 4) shows where equipment is running, but there is an instance of failure. The first line of defence in detecting the fault/failure is ultrasound technology. As you move farther down the curve you have audible noise, hot to the touch, and finally catastrophic failure.
Ultrasound is used to detect faults and failures in rotating equipment before they can be heard audibly with normal human hearing. Obviously, if I have a piece of equipment that I can hear “Roaring” or “Grinding” it is already in a failure mode. So, using ultrasound we can detect faults before they become catastrophic.
A good piece of rotating equipment will have a much lower decibel level than one that is either in a fault/failure mode, or even over lubricated. Predetermined points can be created in the data management software, and data can then be stored onboard the instrument and then downloaded back into the software. This allows the inspector to trend the decibel level over time. Any increase in the noise level will indicate either a lack of lubrication or a more severe fault or failure depending on the amount of increase in the decibel level over a predetermined baseline.
Actual diagnosis of conditions can be done through spectral analysis. The screen shots are of two identical bearings of similar size, type, and speed. The left FFT screen shot shows a tight, narrow band with no harmonics or peaks (Figure 5). The right FFT screen shot shows that there are harmonics or peaks. This would be indicative of impacts, ball pass frequency, or rolling element failures.
Another use of structure-borne ultrasound is for steam trap testing. Steam traps are similar to valves. They regulate the flow of steam and condensate through the system and help to maintain a consistent temperature. Failed steam traps result in decreased energy efficiency of the boilers, irregular temperatures in the system that can affect product quality and loss of heat.
One of the most important factors to test steam traps is trap identification. The inspector must be able to recognize the type of trap that is to be tested. Once the trap has been identified, it will have one of two sound characteristics. The trap will either have an “On & Off” sound, or a continuous flow sound. On and off, or hold/discharge/hold traps are most commonly inverted bucket, disc, thermostatic, and thermodynamic traps. When listening to these traps the inspector should hear a very distinct cycling of the trap.
A leak by condition will be heard when the trap is in the closed position, but steam intermittently bypasses the seat of the trap. The second sound characteristic is a continuous flow sound. This sound would be heard when listening to a float and thermostatic trap. There is a continuous flow of steam and condensate through the trap, but there is a float inside the trap that regulates or modulates the flow. A faulty float or a float that has collapsed due to water hammer will result in a failed open trap. This would be heard as a continuous rushing sound that has no modulation. This trap would be blowing steam straight through the trap, or in the failed open position.
Preventative Solution
Airborne and structure-borne ultrasound is a versatile tool that can be used in any environment. There are many applications where ultrasound can be greatly utilized. One way that facilities can have a big impact on saving energy is through finding and repairing compressed air & gas leaks, and repairing or replacing failed steam traps.
Also, being able to extend the life of an asset without having catastrophic failure can increase uptime and reduce unscheduled downtime. Being able to predict failures in equipment, and then plan accordingly, leads to less interruption in operations and production. For a minimal investment in predictive technologies such as ultrasound, vibration analysis, infrared thermography, laser alignment, and motor circuit analysis, the payback can be tremendous. In today’s business environment, it’s all about remaining competitive in your respective industry. One way to do that is through an increased emphasis on predictive and condition-based maintenance.