Static Maintenance Plans Will Not Survive in the 21st Century
Some maintenance managers are convinced that maintenance plans are created only when the machinery has been installed. That time is gone. Now Preventive Maintenance Optimisation (PMO) is an effective way to optimise the maintenance plan.
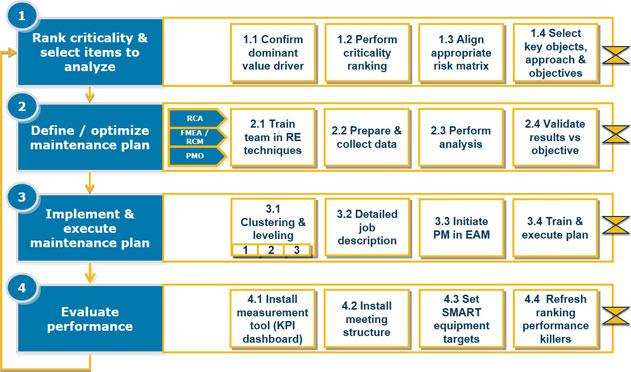
The macro-economic situation of the last decade has been characterised by high fluctuations. The positive economic situation in the beginning of the 21st century has been countered by an economic crisis in the period 2009 – 2013. In 2014, some companies are still in recovery mode. In other branches, financial analysts report new growth. Periods of growth and periods of economic crisis seem to alternate with a higher frequency and amplitude than ever before.
When we execute maintenance audits, we still meet maintenance managers who are convinced that maintenance plans are created only when the installation has been installed. This plan is then executed during the life cycle of the asset. This means companies often encounter problems surviving the actual economic situation.
The creation of a maintenance plan is not a “one time shot”. A maintenance plan needs to be dynamic and tuned depending on the dominant value driver for the company or even for a certain production line. The Reliability Engineering process is part of a closed improvement loop and consequently maintenance plans should be routinely reviewed and improved.
The dominant value driver
If a maintenance plan is created for a plant that has to work at full capacity (dominant value driver: Asset Utilisation), it might not be the ideal plan in economic downtime or when the plant has to focus on cost control. The opposite is also valid. An example from the chemical industry in the Netherlands in the period 2001 – 2007: the focus for a lot of companies was uptime (asset utilisation). In 2008 and 2009, the economic situation changed and many companies had to focus on cost control. On January 5th 2011, there was a big fire in a chemical company close to the Moerdijk in the Netherlands. The Dutch government introduced some strict rules and some new legislation. This resulted in a higher focus on Safety, Health and Environment. In 2014, the economic situation has improved. Some chemical companies are now operating at full capacity, whilst others still have to focus on costs. Companies that haven’t changed their maintenance plan (content and frequencies) during these years are out of business. Thus, Reliability engineers have to modify the maintenance plans. Maintenance plans are not static.
Reliability Engineering has to work with a closed loop
When a maintenance plan has to be set up for a new installation, tools like FMEA and RCM are often used. These tools form the basis of a structured maintenance plan. By executing the maintenance plan, the companies build up a huge amount of information (up-time date, disturbance database, costs, etc.). When a significant disturbance occurs, a structured Root Cause Analyses is the tool to define some countermeasures (and to update the maintenance plan). Some companies forget to use the historical data to aid improvement. Based on this data, Reliability Engineers can conduct a PMO (Preventive Maintenance Optimisation). This is an effective way to optimise the maintenance plan. It is also called an “Inverse RCM”. To execute the PMO sessions in an effective way, it is important to have good maintenance KPI’s. One of these KPI’s makes a relationship between the downtime and the maintenance costs for all your assets (see picture). For those assets where the downtime is high and the maintenance cost is high, it might be necessary to review the maintenance plan.
Mainnovation has developed a “4 x 4” Reliability Engineering matrix. This matrix is a good guideline to turn a static plan into a dynamic maintenance plan. The most important point is that the process is a closed loop. At the beginning of the loop, we evaluate the dominant value driver. At the end of the loop we evaluate the effectiveness of the maintenance plan and, if needed, we start again. All maintenance plans should be reviewed with a certain frequency. In this way the companies can guarantee that they have dynamic maintenance plans.