Nuclear power plant maintenance benefits from participatory development of work and safety
How can work in nuclear power plants be developed so that human activity is a stronger part of safety work? The solution can be found in modeling and inclusive work development.
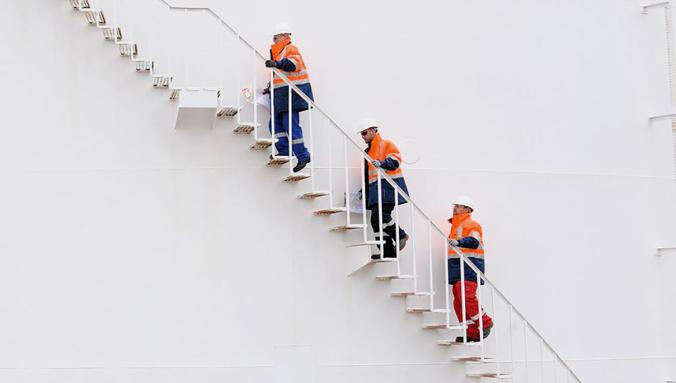
The safe, smooth operation of nuclear power plants requires competent maintenance. Maintenance provides situational awareness; it enables the personnel responsible for the operation of the plant to see the “big picture” of the plant’s technical status. Maintenance ensures that the plant's numerous electrical, automation and mechanical systems and its components and equipment work as planned. It repairs faults, performs servicing tasks in accordance with the annual plan and larger tasks during annual outages. Maintenance also compiles the lessons learnt from previous maintenance shutdowns.
Nuclear power operations apply strict, systematic safety practices and methods and adhere to guidelines, all of which are the result of decades of work and lessons learnt. The functionality of safety management systems is regularly assessed, and safety culture evaluated. The nuclear power operations are highly technology oriented. In recent decades, the safety work in nuclear power plants has increasingly focused on the role of people in safety, too. The nuclear sector is facing changes such as aging personnel and technology, the modernization of equipment, and new ways of organizing work in its power plants. The technology-oriented, regulatory environment sets conditions for the development of work and safety. It also creates challenges for developing systematic ways of evaluating and developing work so that personnel can be considered part of safety improvement.
Safety research and the experience of different industries has taught us that many decision-making situations are so complex that they cannot be solved by only one person. To resolve problematic situations, the views of many different entities and a wide range of experts are needed.
Especially in large organizations, it is often the case that the ideas or plans of the neighboring unit are not known, or that views or operating methods differ. There may be challenges in terms of coordination and the flow of information, also between different levels of organization. Operational staff may feel that the middle or senior management do not understand their everyday activities, or top management may wonder why changes are not taken on. Views cannot always be verified in everyday situations, or procedures are not always sufficiently collaboratively refined.
New ways of engaging and motivating staff and of developing skills and working practices are needed. Systematic practices and skills to develop work and safety in an inclusive manner are important. Participatory development is already used in the nuclear sector to jointly process the results of safety culture or job satisfaction surveys or to plan changes in work. However, sometimes the cooperation between different departments or hierarchical levels needs more in-depth development. It is particularly useful to access tacit knowledge, in-depth knowledge of processes brought about by experience, the various factors affecting operational events, and ways in which to solve disruptions or faults. Tacit knowledge is knowledge that is difficult to put into words. In decision-making situations, it is highly beneficial to exemplify this kind of information and make it more concrete and visible through joint discussions.
The Finnish Institute of Occupational Health has examined whether modeling work processes is an effective way of improving maintenance work in a nuclear power plant in an inclusive manner. Its research project modeled three work processes: repairing faults, planning modifications, and component and system health reporting. This process involved people from different maintenance units and organizational levels. Operational personnel (assemblers), engineers, line management representatives, and occupational safety and health staff participated in a total of six workshops in 2019–2021. The workshops provided coaching in the method, and the groups were facilitated in using it. This joint work produced many development proposals, which were passed on for the organization to implement. They concerned increasing the common understanding through, for example, functioning guidelines, the physical work environment, and clarifying meeting practices.
The results were positive. Modeling the work processes strengthened the personnel's shared understanding of the everyday work tasks and what areas require improvement. People were able to voice their own intuitions and even weak doubts about the goals or arrangements of work. For example, it emerged that the objectives or importance of some key work processes had been obscured. It was important for the actors that the objectives were discussed openly. Addressing the strengths and successes of cooperation was particularly useful, which also made it easier to raise more controversial issues.
The development of safety requires openness, joint resolution of challenges, and clarification of complex or vague issues. The results show that participatory development methods can be a means of moving the culture of action in a more positive and solution-based direction. Participatory development methods can complement traditional safety practices and support the recognition and handling of weak signals to promote more proactive safety management.
It is advisable to use participatory methods to reduce disruption, improve the quality and fluency of work, or promote cooperation and the flow of information. Especially in safety-critical areas, it is important to ensure that staff have a common understanding of work processes and their impacts on each other. This need is emphasized in change situations: for example, in organizational reforms /re-organization or when a new technical device is introduced.
Joint development can be experienced as laborious and time-consuming, but its value is reflected in reduced friction in cooperation, and in being able to raise issues more constructively.
Human Factors is embedded in nuclear industry safety management
Participatory development is a key approach in the science and practice of human factors (HF). The application of HF in safety practices is mandatory in the nuclear power industry. It is required by both the International Atomic Energy Association (IAEA) and national authorities. HF strives to improve the performance and safety of the systems and the well-being of the personnel. The starting point is to understand people's capacity and limitations, the variety in human performance, and to utilize this knowledge in the design and development of work, equipment, and work environments, as well as in leadership and organizational development.
The awareness of HF’s impact on safety has increased, and the use of the term has become clearer and more common. It is important to understand the topic in a holistic and solution-oriented manner. HF is a broader issue than mere individual performance or human activity under special observation or control. The goal is that organizational factors and technology create the conditions for people to succeed in their work. For this to be possible, we must first understand the characteristics associated with human activity, then find the best practices to support human activity at the workplace.
An essential aim of HF is to understand the background factors that influence the realization of safety:
- How is work best organized, led, and managed?
- How is safety assured during changes? How are everyday operations understood?
- What helps people succeed in daily work? Are there specific concerns about work ability or safety?
- What hinders people from succeeding in everyday work tasks?
Text: Anna-Maria Teperi, Arja Ala-Laurinaho,
Ilkka Asikainen, Vuokko Puro
Images: Finnish Institute of Occupational Health