Machine learning is not the gold-plated silver-bullet solution to operational woes you may think
There is a lot of hope and hype associated with machine learning, data analytics, and the IIoT. To understand why your business is not achieving peak potential we need to consider all the sources of waste, including the reliability of the equipment, and the reason why that waste exists.
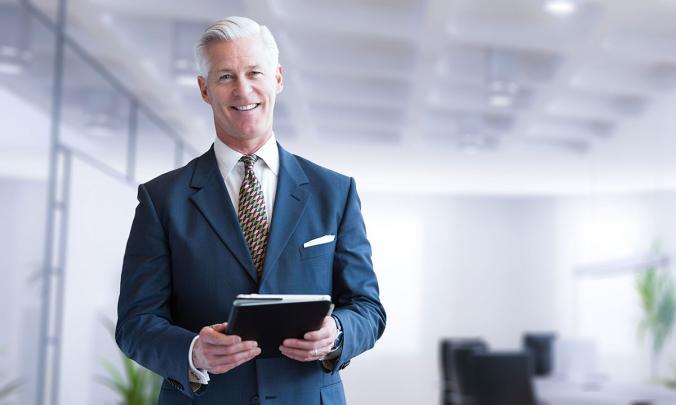
Every day, decisions are taken (and opportunities missed) that ultimately result in waste, poor equipment availability, sub-par utilization, poor quality and production throughput, and ultimately, safety/environmental incidences. If you think of your plant as a person, we shoot ourselves in the left foot during the design and acquisition phase, and in the right foot during the maintenance phase. We operate in silos, so the left hand does know what the right hand is doing, and we thus make poor decisions. The brain does not know where the opportunities exist, and the heart does not really care. The result; we limp along in frustration.
We could replace the brain with the latest intelligent software, thus making better operational decisions. But ultimately all we can do is optimize our limping, uncoordinated, largely uncaring body that continues to make many of the same mistakes.
So, what is the answer?
We need an approach that resolves the root cause of all these issues. At the heart is the leadership and culture of everyone from the senior executive to the operator and maintainer. With a focus on business performance, and a culture of mutual benefit and contribution, everything is possible.
Crystal clear understanding of our goals
We must start with a clear focus on what the business is trying to achieve. Every future action must be aligned with those goals.
Assess the business case
Next, we must assess the current and desired state whilst recognizing where we have existing strengths, and conversely, opportunities for improvement. It is that gap that forms the business case for this initiative.
Fix the heart
After developing a strategy that is aligned with those goals, we must begin the process of changing the culture. People make decisions every day that affect the costs, efficiency, and performance of the organization. They need the desire, skills, and mandate to change their behaviours.
Stop shooting ourselves in the left foot
Future purchases and use of service providers must seek to achieve the lowest lifecycle costs and peak performance; we must prioritize reliability, operability, maintainability, and safety over the up-front cost. And we need a gatekeeper to keep problems out of the plant.
Stop shooting ourselves in the right foot
We must develop a disciplined approach to everything we do. All maintenance tasks must be performed as if lives depend on it. Just one way to do everything.
Care for the equipment
Our precious assets must be started, operated, maintained, and shut-down so as cause minimal stress, whilst also achieving peak output.
Data driven decisions
Now we apply data-driven intelligence to our process. By monitoring asset health, process performance, and key operational metrics, we can optimize our maintenance and operational decisions and eliminate waste. Continual operational improvement enables continual performance improvement.
Leadership, value, and culture
And now we circle back around to the core element that makes or breaks our process. With a constant focus on mutual benefit, peak performance will be sustained. If not, you will be back to the limping, uncoordinated, uncaring plant you have right now…
Much more can be said about the proposed approach, but the key is to broaden your scope. Data intelligence will enable optimal performance, but only if the other elements are also
addressed.