Lubrication Reliability – Start with a Revolution
Here is the reality. If you are looking to improve equipment reliability across your entire site, you might wait for Big Data, IioT or I4.0 to break through, or to do it for you, but I would recommend that you start a lubrication revolution.
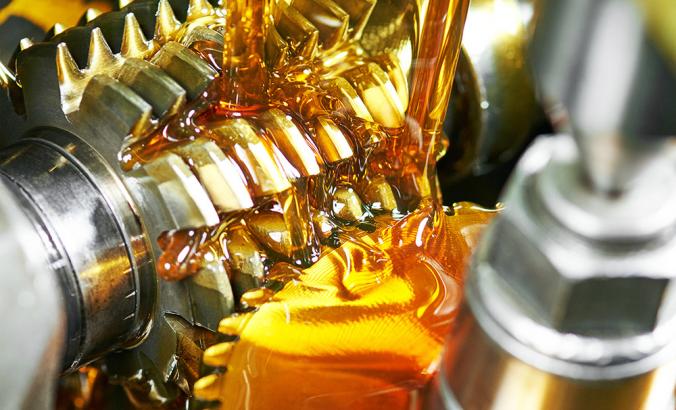
Why a revolution? Well, it appears that despite the efforts in awareness over the past decade, many plants still ignore, disbelieve, overlook or just struggle to define and comprehend the requirements of a disciplined lubrication program that promotes defect free operation. Furthermore, most actual lubrication programs are antiquated or rely on gut feeling, guess work and old habits nor has it been given the proper attention it deserves. So just by improving the actual program, in the long run you will revert to old ways again, neglecting the effective sustainability that comes with a holistic approach. A holistic view enhances equipment reliability and cuts out all manner of unnecessary losses that results in major bottom-line savings from lower maintenance costs, maximized production levels, improving risk-safety, higher energy efficiency, best utilization of all staff and reduce the carbon footprint to mention a few. In other words: the revolution means reinventing how lubrication is done at your plant instead of going blindly through the same old tasks of lubricating your equipment and jeopardize its reliability.
“The power of the Plus Factor is potential, but it is not self-activating. It is latent in human beings and will remain latent until it is activated “
Tom Peters
Lubrication has multiple ties to reliability being the lifeblood of plant equipment and is fundamental to keeping it working correctly. Its most important role is coating sliding or rolling surfaces and carrying away friction-generated heat, thus eliminating wear and corrosion. Lubrication determines reliability not only through how a particular lubricant is designed for use in specific machinery, but also in the way it is applied, or misapplied, in the field.
Successful implementation of a Lubrication Reliability Program considers several technical, organizational and ~the utmost important~ human factor. No single program works for everyone. Lubrication is a continuous evolving process that requires a combination of technical improvements and employee engagement to yield successful results.
Technical
There is no such thing as a one-size-for-all lubricant. Industrial lubricants evolved over time into highly specialised and carefully designed products. They possess a collection of physical and chemical properties that ultimately define the lubricant’s performance properties. Depending upon its electromechanical design, each piece of equipment has certain lubrication reliability requirements that are a function of the forces, stresses, and strains placed on the lubricant. Thus the correct lubricant is always application-driven. The Lubrication Reliability Program applies engineering analysis to match the lubricant’s performance propertiesto the equipment’s lubricant reliability requirements. Procedures for lubrication at design and engineering processing make it sustainable to stay updated on industry standard as new technologies and innovations are continuously introduced.
Organizational
A Lubrication Reliability Program has to be a business decision. Leadership and leadership support is paramount in Lubrication Reliability; it is not something the maintenance department can do on its own. It requires support from the highest levels of the organization as resources and potentially line time will be required. Countless studies indicate that when communicating the business need for change, the most effective communicator in an organization is the CEO, as no one will intentionally stand in the way of any of his or her words.
Having the seeds planted for a behavioural change in Lubrication Reliability, leadership support will consist of measurements systems and feedback loops so behaviours become self-perpetuating. The rewards of successes will seek that the Lubrication Reliability Program will not be suffering from a slow implementation pace or incomplete implementation or even return to old practices but becomes self-reinforcing. In fact, the more we cultivate the behaviours required to support Lubrication Processes, the more we understand Lubrication Reliability as a visionary belief that is tied to the business strategic objective to drive inefficiency, risk and defects from the system.
Human Factor
Performing lubrication seems elementary and has been approached the same way for many decades. While lube tasks are considered routine and often assigned to low skilled workers at the plant, it is critical to get the right lubricant in the right place at the right time using the right procedure or technique, every time, to ensure machine condition and equipment reliability.
In a Lubrication Reliability Program, lube techs are knowledgeable workers with highly specialized skills. They have a fundamental understanding about machinery engineering - how machines operate and what makes them fail, lubrication fundamentals, chemistry to understand the lubricants themselves, reliability engineering, maintenance engineering, and all the technologies, software, gadgets and services required to make lubrication work in the plant. They are engaged, dedicated and continually evolve the lubrication processthat proactive lubrication strategies prevent damage or excess wear before it starts.
END
The key to Lubrication Reliability is finding a company that not only can recommend the right high-performance lubricants for vast applications but also can recommend and implement sustainable reliability solutions. Deciding to start with your lubrication revolution can be easily done with the help of a professional. I-care has knowledgeable lubrication consultants helping you to shift your business-as-usual lubrication to adopt, implement, sustain and continuously evolve into reliability best practices.
Text: Pedro Viña, Senior Consultant Reliability Engineering for Maintenance, I-care