Automation and digitalized asset management increase safety and productivity
Autonomous systems are revolutionizing many industries, resulting in safer and more efficient processes. New technologies, services and data are generating new business opportunities while the mobile machinery industry is currently driven by increasing customer needs for automatization, electrification and digitalization.
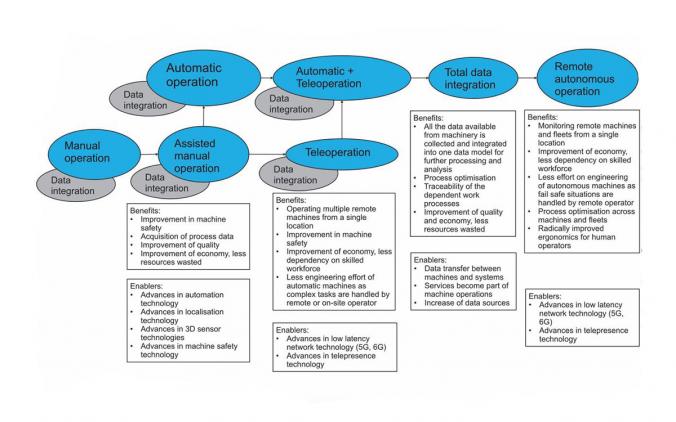
Another rising issue is improving safety in hazardous areas. There is a market for remotely-operated and/or automated work machines. While the current sources of sensory data are not sufficiently reliable in harsh conditions, technology is continuously evolving and the opportunities are increasing daily.
Towards autonomous mobile machines
Safety, quality, cost-efficiency and traceability of work processes can be improved by automation and remote operation. Figure 1 introduces a roadmap towards autonomous mobile machines where the development phases from manually operated machines towards autonomous operation are presented.
As the level of automation of manually-operated machines increases, the next development phase is typically a machine with enhanced manual operation. Assisted manual operation requires the operator on site to control the machine, or speed and position is under control without specific operator actions for each actuator.
The next step up from enhanced manual operation is to develop automatic features or to extend the machine with a teleoperation interface. The chronological order of introducing automatic and teleoperation features depends on the machine type, business environment and machine builders’ strategic choices. In the mining industry, teleoperation of machines improves ergonomics and safety, as operators do not need to enter or stay for long periods in hazardous areas. When the automatic machine is extended with a teleoperation interface, the remote operator can connect to the machine via a low latency network and monitor the machine via a real-time video stream. Machines with automatic or teleoperation features, or both, currently exist.
Total data integration is a prerequisite for remote autonomous mobile machines. In total data integration, all available data from the machinery is collected and integrated into a single data model for further processing and analysis. The final development phase of the roadmap is remote autonomously operating machines that are connected via a low latency network. In the future, autonomous machines will be capable of accomplishing more complex tasks than their automatic predecessors. Furthermore, autonomous machines are able to react to unexpected events. Due to robust automation, remote autonomous machines are capable of operating long periods without direct user intervention. However, remote autonomous machines also include a fail-safe mode in case of unexpected breakdowns or failures, which can be conveniently handled by the remote operator via a teleoperation system.
Safety strategies and concepts for autonomous and semi-autonomous mobile work machines
Strategy for improving the safety of autonomous mobile machine systems is essential. The three strategies described here are:
Rules for automated area and supporting technology, like traffic lights, warnings, guidelines and augmented reality. Economical, but additional means are often needed to ensure safety.
Isolated area. Access control for isolated area(s).
Safe separation distance. Tracking and distance sensors.
Each strategy can be associated to several safety concepts, which are applied to achieve adequate safety. Figure 2 shows some examples on how to apply the strategies in autonomous areas.
With current technology, isolation is the best-understood means of ensuring the safety of an autonomous mobile machine system. For relatively small systems, machine area isolation is a practical way of achieving adequate safety. In large open systems, however, barriers become unfeasible due to the length of barrier required. Isolation is therefore not a sufficiently scalable strategy and can become expensive.
Applying rules to an autonomous system is a scalable and economical strategy, but the safety of rules-based solutions is considered relatively low. The strategy entails some investment costs in the form of traffic lights, traffic signs and road markings, as needed, as well as personnel training.
The safe separation distance strategy has a clear technological orientation, as the distance between personnel and moving machines must be measured. Currently, all sensors have certain weaknesses depending on the operating conditions or environment; however, sensor technologies are improving constantly and prices are coming down. Sensor fusion can also tackle some weaknesses of individual sensors. Indoor safety can be usually addressed by applying low speed limits and appropriate safety sensors. Outdoor safety is more problematic as sensors are less reliable in rain, fog or muddy conditions and longer driving distances require relatively high speeds (manual driving vs. automated driving speed). The separation distance strategy is to some extent scalable, but each object in the area requires technology, which raises the costs. Outdoor safety strategies are thus much more exposed to demanding operating and environmental conditions.
In all of the three strategies, the challenge is how to deal with uncertainty. In the ‘rules’ strategy it is uncertain whether all personnel will obey the rules. In the ‘separation distance’ strategy sensor performance in outdoor applications is unreliable and highly dependent on environmental conditions. In the ‘isolation’ strategy the means of isolation may vary. Locked doors and high fences guarantee good isolation, but there are situations when people need to enter the area. Complete isolation is not practical. Keys or rules for entering the system can be applied, but then uncertainty also increases. Designers of autonomous mobile machine systems need to accept some degree of uncertainty, but the risks must be carefully controlled. Currently, there are very few good examples of safe and practical autonomous mobile machine systems. More examples are needed, and the standards also need to evolve in order to define more clearly the acceptable levels of uncertainty and risk.
Services for asset management
Increased automation and also the increased amount of data have enabled and increased the significance of data-based services for ensuring the cost-effective and productive management of the industrial assets. Increasing demand for efficiency, quality, capacity and availability performance of the systems call for new technologies and implementations of the asset management standards (e.g. ISO 55000) that utilize the opportunity to utilize data, learn from wide machine and component fleets and to integrate expertise of OEM’s and process experts.
The use and value of predictive analytics need to be understood in a wider value context, as depicted in Figure 3 (adapted from Ahonen 2019). Three focal topics of asset management are addressed, namely maintenance, operations and investment decision-making. Furthermore, for equipment manufacturers, one of the main drivers of data-based solutions is the feedback loop to R&D and product development. This is particularly important in the transition to new business models with performance-based contracting. Thus, since equipment manufacturers may have new incentives for stressing different ‘design for X’ aspects in product development and gathering experience from the field is of increasing significance.
ISO 55000 defines asset management as activities that support the realization of value while balancing financial, environmental and social costs, risks, quality of service, and performance related to assets. Analysis of these tasks from the viewpoint of more effective use of data for supporting key decision-making situations may open up new opportunities and support the quick technology experiments carried out by a number of companies related to development of digital services.
Conclusions
The demand for automated and remotely-operated machines arises from the need to improve the safety, quality, cost-efficiency and traceability of work processes. Ecological issues and sustainable development require minimizing resource losses while maintaining or even improving quality standards. However, the level of automation affects the safety requirements. The more automated system, the more requirements there are for the system, and the more the manufacturer needs to take responsibility. Thus, one needs to thoroughly understand the optional strategies and related concepts for different operational environments. At the same time, there is an identified need for a transition from transaction and sub-contracting based collaboration models towards more integrated practices in company ecosystems. Customers are expecting more holistic service offerings and, as the complexity increases, companies are not able to hold all the required expertise and knowledge in-house.
Information on recent developments in the technology and discussion on the current trends and how to answer them is provided in more detail in the research report “Advanced technologies for productivity-driven lifecycle services and partnerships in a business network” available at:
www.vtt.fi/sites/tecnetwork/.
Text: Toni Ahonen, Jari Ahola, Timo Malm, Pekka Isto and Aki Aapaoja, VTT Technical Research Centre of Finland