Are you in the “Circle of Despair”?
If you work in a highly reactive maintenance organization, you will be trapped in a “circle of despair” and you are wasting too much time on doing the wrong things. A circle of despair starts when you have to react to a problem, or a perceived problem, on a short notice. You then try to correct the problem as fast as possible; the quality of the correction will then be less than perfect. This leads to that the equipment soon has to be repaired again and the circle of despair will repeat itself and absorb all time you could have used to do the right things.
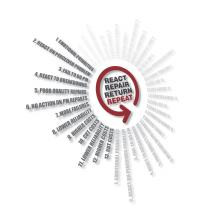
The reasons why most maintenance organizations are using more total maintenance hours than necessary is that they waste too much time on doing the wrong things, because they work in a system that does not allow people to be as efficient as they can be. To correct the system is the responsibility of leadership. It is the most important thing a leader can do. I use the term leader, because too many managers are just managing status quo.
Some examples on doing the wrong things include:
Maintenance is driven by cost instead of the actions that drive cost. Maintenance managers become more focused on the budget constraints then on delivering reliability. The focus must be to improve total reliability. It is well proven that a long-term focus on improving reliability will produce more quality production and lower costs.
Reacting to Equipment breakdowns. Our studies show that between 50 percent and 70 percent of all maintenance work is avoidable. The basics of maintenance prevention, the right operating practices, and correct installation will reduce the amount of maintenance work needed. The corrective work remaining can be done more efficiently through good inspections together with better planning and scheduling.
Reacting on emotional priorities. Most maintenance organizations are viewed as service providers and not providers of equipment reliability in an equal partnership with operations. Operations are still viewed as the customer ordering work from the maintenance organization. This leads to a mindset to please the customer by responding to their requests immediately instead of delivering what is best for the business.
Top Management oxymoron.
Top management typically agrees to all of the above but often responds that “Reliability is top priority, but we must cut costs first”.
I call this statement an oxymoron because the fact is that better reliability will drive down costs while a focus on lower costs drives down reliability. It is a very difficult predicament to solve. The solution to achieve consistently and sustainable lower costs is long term, but as a manager you are working in a system that forces you to make short-term decisions.
The focus on cutting costs is in most organizations done by deferring maintenance work. But, a valid maintenance job can never be eliminated – it can only be postponed and you will then often end up paying much more later on.
Cutting costs by elimination of people without any improvements in people productivity will result in increased total maintenance hours. You might have fewer employees, but there will be more overtime and contractor hours. This will result in short-term savings and long-term loss.
If the focus is to improve total reliability, you will see short-term cost and long-term, continuously improved production throughput and lower costs.
If you are in the circle of despair and plan to break out of it, the first step is that the mill leadership team has to come together and focus on what drives costs down long-term and get away from short-term cost cutting. The lead team has to believe that reliability will drive down cost and understand that short term cost cutting drives down reliability. Unless this agreement is in place, the mill will continue as a reactive organization and have a high maintenance cost per ton.
Torbjörn Idhammar,
President of IDCON IN