5 Ways to Break Out of the Reactive Maintenance Cycle of Doom
Improving reliability will help the bottom line of any organization – and much more. However, if that organization is experiencing any level of reactive maintenance, then improved reliability may seem like a pipe dream. Until you can break out of the “reactive maintenance cycle of doom”, it is not possible to make any real inroads into your reliability improvement initiative.
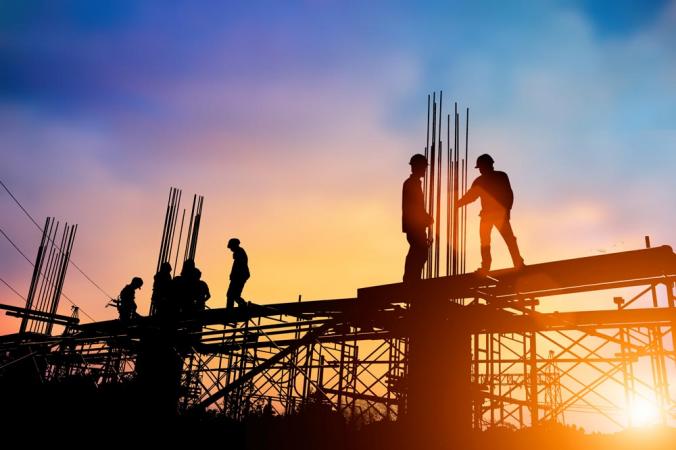
If you were to look at the failures you are experiencing today, would you agree that most of them are preventable? Are those failures consuming your resources, manpower and budget? As a result of having to deal with those failures, are repairs performed poorly, or are you performing temporary repairs that you plan to correct later (but never do)? And as a result, are you experiencing more repeat work? Do you ever perform root cause failure analysis so that you can eliminate those failures? And what happens when suggestions are made for improvement? Are they ignored?
And what is management’s response? Do they reduce the headcount and try to squeeze the budget in order to deal with the high costs of downtime and reactive maintenance? What happens then? Does morale decline? Do standards drop further? And as a result do you experience even more preventable failures that consume resources and results in temporary repairs being performed? We could continue to go through this list, around and around and around.
Well, if you answer “yes” to the majority of the questions above, then you are trapped in the reactive maintenance cycle of doom… You have to get out!
But How Do You Get Out?
We have to get out of the reactive maintenance cycle of doom. If everyone is dragged back to perform reactive work, then none of the proactive tasks that will ultimately lead to improved reliability can ever be performed. Well, you may believe that management could hire additional people so that you have the resources to perform those proactive tasks. That is about as likely as management hiring unicorns to maintain the grass.
The basic answer is that we have to do much more with the people and budget that we have right now. We have to stop performing tasks that waste our money, waste our time, and induce failures in our equipment. This may sound like a push for higher productivity. In a sense, it is. But that is not our focus.
So, how do we break out of this vicious cycle so that we can make real improvements in reliability?
1. First We Have to Change the Culture
The first step is to change people’s attitudes, which will change people’s behaviour. Everyone has to believe that they will be better off in a reliable plant. They also have to believe that they can contribute to the reliability improvement process.
There are a number of ways to go about doing this, and it is a topic worthy of its own article (or even its own book) but there are a few things we can do to improve the culture:
- Ensure that senior management is 100 percent behind reliability improvement and ensure that they are vocal in their support
- Educate people so that they truly understand the benefits of working in a reliable plant
- Educate people so that they understand why failure occurs
- Involve people, ideally in a “brown paper process”, in order to get their suggestions for improvements and get their assistance in making the improvements
That last point needs a brief explanation.
As intelligent managers or maintenance/reliability engineers, we can come up with a lot of ways to improve reliability. We can devise a strategy via the Reliability Centred Maintenance (RCM) analysis process. And then we could implement that plan and ensure that we do what is necessary to change people’s behaviour.
But people do not like to be changed. They will change when they are a contributor to change.
Besides, who knows more about the reasons why equipment fails (and why we experience production slowdowns) than the operators of the equipment and the front-line people who maintain it? But do we normally ask those people for their opinion or assistance? No, we don’t… And then we wonder why we don’t enjoy the success we hope for.
So that is something that we are going to do differently in the future. The “brown-paper” process will gather together the “front line” people in small groups and learn from them what needs to change. And then we will ask them to lead the mini-projects that correct the problems that are identified – in that way they take ownership and free up your time. An activity like this is key to your success.
2. Implement a Work Management Programme
Well, we really just need basic (but effective) planning and scheduling for now. Wait a minute. Doesn’t that mean you need an extra person? No, you will take one of your most effective trades people and put them in the role of planner/scheduler. But surely that must mean that you have even fewer people to perform the corrective (and hopefully proactive) maintenance work. That is true, but the fact is that we will make the remaining trades people far more effective.
Planned and scheduled work is 20 percent more efficient than unmanaged work. And it is safer. And the work will be done right the first time and thus not lead to future failures. That improvement in efficiency means that your 40-person crew can now do what a 48-person crew can do. It is just like gaining an extra eight people.
3. Work on Communication to Foster Cooperation
The chances are that the relationship between maintenance and operations/production is not great… That relationship has to improve. The maintenance team needs the cooperation of operations so that the equipment is ready when work must be performed. Operations needs to work closely with the maintenance team to ensure that their equipment can perform with minimal downtime, minimal slowdown, and the highest level of quality.
In addition, the operators of the equipment can contribute to reliability improvement by changing the way they operate the equipment, and performing basic inspections and maintenance tasks that will free up the time of the skilled maintenance craftspeople.
As part of this process there must be regular morning meetings where maintenance and operations can coordinate their activities and provide feedback on the jobs performed on the previous day.
4. Eliminate the Root Causes of Failures
It is not possible to break out of the reactive maintenance cycle of doom unless we eliminate the root causes of those failures. Having the right attitude, improving communication, and implementing planning and scheduling will eliminate some of the root causes of failure, but we need to do more.
We could use root cause failure analysis, but we can also go through a fairly simple checklist of the most common causes of failure and address those first, including improved lubrication (and eliminating contamination), and precision installation/shaft alignment/balancing/tightening. We can also work on the tasks identified via the “brown-paper” process.
But I assume you don’t have the resources for that. Or do you?
Step one is to recognize that planning and scheduling and involving operators in basic maintenance tasks will free up resources.
Step two is to take a close look at the PMs you are performing now and remove all of the tasks that waste your resources. You may be surprised to find that you do a substantial amount of work that is either unnecessary or it contributes to future failures (or both). This optimization process will reduce your workload and thus free up time for trades people to do the job correctly the first time and to perform proactive tasks.
Step three is to take one of your best trades people and dedicate them fully to proactive jobs. It has to be an A-grade emergency before they are allowed to respond to reactive maintenance jobs. Yes, that means that two of your best people are now working on planning and scheduling and proactive jobs. They are best qualified to define the jobs and perform the jobs.
You should also take a look at your spares management programme (which spares you keep, how accessible are they, and whether the condition of the spares degraded in storage), develop standard maintenance procedures, and execute a basic 5S programme, so that the work area is clean and organized.
The proactive jobs eliminate tomorrow’s problems. Eliminating tomorrow’s problems saves money, saves time, and improves morale.
5. Finally You Need to be Warned about Tomorrow’s Problems
Condition monitoring warns you about pending equipment failures; the nature of the problem and the severity of the problem.
You may need to keep it simple internally by utilizing simple vibration meters, basic ultrasound tools, inexpensive infrared measurement systems, and targeted inspections. You can then use outside consultants to perform the more sophisticated testing, such as detailed vibration analysis, oil and wear particle analysis, tests on electric motors, and more.
Once you have broken free of the reactive maintenance cycle of doom you can begin to bring the more sophisticated condition monitoring technologies in-house (if the circumstances are appropriate).