10 basics to improve MAINTENANCE in your organisation
What are the 10 fundamentals to improve maintenance in your organisation? The question seems trivial, but when you stop to think about it more closely, you will quickly end up with a list that is much longer than anticipated.
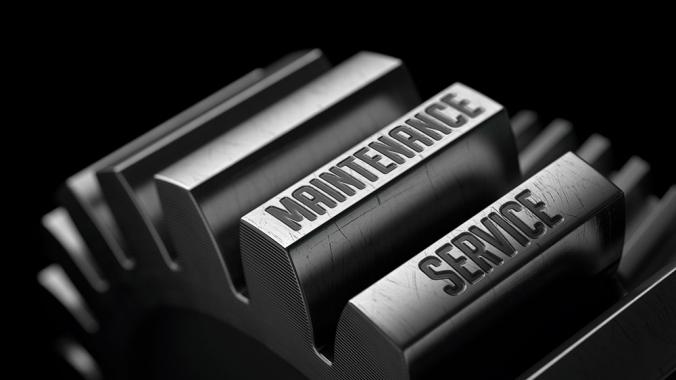
Netherlands-based consultancy consulting group Mainnovation wanted to find an answer to the question. In the beginning of July 2019, the Belgium Maintenance Association BEMAS organised three afternoon study sessions about the 10 basics for the technical department. At the event, Mainnovation together with more than 60 other professionals from the field of Maintenance & Asset Management discussed and ranked the themes marking three out of ten propositions with a high amount of interest.
The themes were assessed by indicating if they were: Totally agreeing – Agreeing – Neutral – Not agreeing – Totally disagreeing with the 10 propositions around the 10 basics.
So, what were the 10 basics for the Technical Department?
Here they are listed and briefly explained:
1.We speak the language of the boardroom
The maintenance manager or the head of the technical department communicates with the direction about Maintenance & Asset Management by explaining everything in terms of value. Here is a clear picture of what the “dominant value driver” is and we keep maintenance from being seen in terms of pure cost.
2.We close the PDCA loops in all processes
(PDCA: Plan – Do – Act – Check)
We are used to looking at everything through the “continuous improvement lens”. We are critical and constantly ask ourselves, how we can do business better in the future. We do this for technical as well as organisational challenges. We also put in place improvements in a structured manner.
3.We adjust on the basis of maintenance indicators
We use available data from our Enterprise Asset Management (EAM) system. Based on this, we develop several maintenance indicators and use them to make adjustments in a structured way. With these indicators, we adjust the content of the maintenance plans and processes, we amend the organisation and we optimise the supporting IT tools.
4.We have agreements on urgencies: all urgencies are real “Urgencies”
When can we talk of a malfunction, or an actual “urgency”? Is it always clear for the applicant whether direct intervention is required or not? Who is well placed to make an assessment? Or do we leave it as is over the issue of the day?
5.We have good Gatekeeping for work requests
There are different types of work requests within maintenance. Plannable activities often result in a considerable workload. These activities, such as inspections, improvement proposals, and work for third parties are assessed in a gatekeeping discussion. On top of controlling the comprehensiveness of the question, we determine the priority and the corresponding execution date together with the applicant and the operator.
6. The work preparation & planning is elaborated down to the last detail
A good work preparation & planning is the driving force of an efficient working technical department. All plannable work is prepared in detail (the correct spare parts are ready; the special tools are reserved; instructions are written up; the permit is ready; there are clear agreements regarding the sequence, the required time, the team, the testing and the release of the installation; the required external suppliers are provided; etc.). That way, the technician can focus 100 percent on the execution of his or her tasks.
7.We adjust maintenance plans based on feedback
Maintenance plans must be addressed dynamically based on the changing situation (market, dominant value driver, etc.). But past performances are also an important source of data to adjust things. Based on the number of failures, the length of the failures and the cost that we spend on each installation, we improve the maintenance plans in a structured way.
8.We bring order to the Technical Department (TD) and divide the LT – MT – ST activities (long term – medium term – short term)
A lot of maintenance organisations live by the issue of the day. As a result, a lot of people are busy with short-term problems and little attention is paid on long-term goals. A clear structure with roles and functions that work on the long- and medium-term smooths things over in the organisation as well as ensures that we work towards a better future in a structured manner.
9.We excel in lubrication-technical-maintenance
Lubrication maintenance is perhaps a strange theme to bring up in this list. On the other hand, this theme is a good indicator of the maturity in a maintenance. Lubrication is probably the oldest maintenance operation, however, it is still an area that can be improved drastically. Do we lubricate correctly, with the right frequency, with the right product? Do we stock the lubricants in the right way, etc.?
10.We keep an eye on the change process in the
technical department “Focus + Change” is the key to success. With “Focus”, we develop the right analysis and determine the points of improvement. On top of that, we also need “Change” to transform things in practice. If we want to manage actively the resistance to change, then we must work on acceptance and the corresponding project of change from day one. It is, therefore, an art to avoid the common pitfalls in change management.
Out of the 10 fundamentals maintenance professionals were the most in agreement with the following themes, giving the highest scores to the following three topics:
- We have clear agreements on urgencies
- We speak the language of the boardroom
- We keep an eye on the change process in the technical department
The themes with the lowest scores and, therefore, with a great potential for improvement were the following:
- We bring order to the TD and divide the LT – MT – ST activities
- The work preparation & Planning is elaborated down to the last detail
- We adjust maintenance plans based on feedback
TOP PRIORITIES
At the end of the afternoon study session, Mainnovation also asked the participants to indicate, which themes they would like to work on in their own organisation. Out of the 10 themes, eight were put on the improvement agenda by more than half of the participants, with the three following top priorities:
- We want to give more attention to the change process in the technical department
- We want to close the PDCA loops in all processes in a structured way
- We want to improve Gatekeeping for work requests
CONCLUSIONS:
The theme “We want to give more attention to the change process in the technical department” and the additional change aspect was the theme with the highest score. Eighty-one percent of the participants see potential improvement here and would like to pay extra attention to this. Although maintenance professionals gave themselves a high score in terms of attention given to change process within the technical department at the beginning of the session, this subject received the highest priority to work on and to further improve. We also see this for our own customers at Mainnovation. “Keeping an eye on change” is a crucial theme in change processes. It is important here that all people in the organisation understand the need for change, that there is a shared vision of the future, and that we work with viable intermediate steps.
Closing the “Plan – Do – Check – Act” loop is viewed as the second priority for the participants. In a lot of cases, the improvement circle is not closed today. There are a lot of ideas and good initiatives but measuring and adjusting is not always done.
The third priority is gatekeeping, which is the assessment of plannable work requests. It is a crucial process to manage incoming workflow. Without a good gatekeeping, there is a high chance that the influx of work requests will influence the operational workflow so much that it will be difficult to keep a clear view of the important and priority works.
With these 10 basics, everyone can make their own analysis of whether the themes are relevant to their organisation. Perhaps the Top 3 will help you to work on the foundation of a modern and proactive technical organisation
PETER DECAIGNY
Partner of Mainnovation
www.mainnovation.com