Wind Power and Maintenance Leveraging the OPC UA Technology
The business value proposition for open standards in the world of renewable energy; data and information drive efficiency in the world of the maintenance and asset management for modern wind turbines.
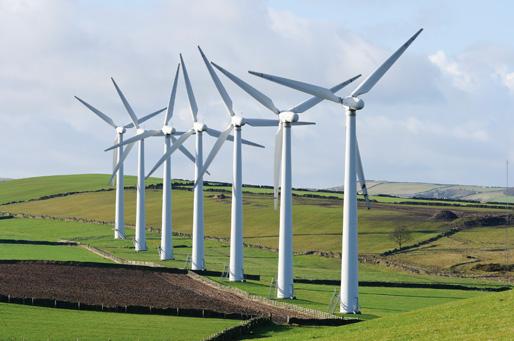
The global demand for renewable energy combined with government legislation is driving the world to have wind turbines and wind farms. Wind power generation requires things like integrated safety, control, motion and vibration monitoring solutions to maximize uptime and reliability while protecting capital investment. OPC Foundation vendors are rapidly deploying products (many already released) to address the special requirements for the automation of wind turbines.
The value proposition is to have the right data and to be able to transform that into useful information. In the world of renewable energy and specifically in wind power farms it is not uncommon to see upwards of 5,000 wind turbines in remote locations. The importance of gathering data from every single wind turbine and keeping and analysing all of this data into information is very important in order to keep the wind power farms operating very efficiently in a sustainable world.
Build to Run 20 Years
Modern wind turbines are designed to work approximately 120,000 hours to route their estimate life span of 20 years. This is under the assumption that the wind turbine is operating approximately 66 percent of the time over the two decades.
The operational and maintenance costs associated with a new wind turbine are generally very low. As a wind turbine ages the expectation is that the costs increase. Studies have shown that wind turbines have the annual maintenance cost of an average of 5 percent of the original cost of the wind turbine.
The management of the operational maintenance can bring cost reductions to wind farms, but they are typically located in isolated remote locations. The monitoring of the assets and gathering of data is required for the adaptive and predictive maintenance of the wind turbines.
Many of the components within a wind turbine are subject to more wear and tear than others. Moving parts typically wear out faster than none moving parts and exposed components wear out faster than those that are not exposed. Simply said the parts that wear out fastest are the rotor blades and gearboxes.
By the time a wind turbine comes to the end of its life, the technology has probably changed significantly. Instead of refitting and repairing the turbine it can be more cost effective to just replace the whole thing. The tower itself can usually be saved.
Industry experts tell us that the typical price of the replacement components excluding the rotor blades, the gearbox and the generator is approximately 20 percent of the cost of a new turbine assuming the other existing components must be intact with not in need of repair.
Open Standards, Data and Information
What does all this talk about wind farms and maintenance of wind turbines have to do with open standards, data and information?
Wind farms must have remote monitoring capability due to their isolated location. Many automation components are needed in order to monitor all moving parts and to do the proper level of predictive analysis based on the data gathered. That information helps to perform cost effective and timely maintenance of the components.
How do we make all this work from an automation perspective? We must be able to acquire all the data and make intelligent decisions converting the data into information. The owners of the wind farms can use this information to do proper maintenance and manage all of their assets with all of the wind turbines and other associated equipment on the wind farms.
We need uniform, standard ways to allow acquisition of data and interpretation of that data into information from numerous vendors on a variety of devices and operating system platforms. Vendors building the components for the turbines need to instrument the various moving parts (which are the parts that we said fail after repetitive use and wear and tear), and then provide the small, embedded computers to hook up to these sensors throughout the wind turbine. The sensors provide both analogue and digital data about the operational characteristics of the movable parts!
The OPC Foundation collaborates with many organizations to standardize on their data and information models, and in some cases actually helps to develop data models for components. IEC 61400 is one of the standards specifically targeted towards the wind power turbines and wind farms. This specification identifies many things including the standardization of syntax and the semantics of data from wind turbines.
So now we are talking about open standards! OPC Foundation is working with representatives from power generation companies to have their data models mapped into the OPC UA architecture with specifications based on IEC 61850 and IEC 61400.
OPC UA Helps to Transfer Data
OPC UA stands for the OPC Unified Architecture. OPC UA is all about multiplatform multivendor secure reliable interoperability for moving data and information from the embedded world to the enterprise. It is all about connectivity, industrial automation and all the related domains.
One of the first collaborations that OPC engaged in was OpenO&M, which was a partnership between MIMOSA, ISA-95, WBF, OAGIS and OPC. It was based on the initial work between OPC & MIMOSA focusing on asset management, doing preventative maintenance and improving reliability. MIMOSA provides the deep repository of information, and OPC became the mechanism for transporting the information between various applications.
OPC UA is a service-orientated architecture that extends the OPC classic architecture (which was based on Microsoft technology) to provide seamless integration across multiple platforms for moving data and information.
OPC Foundation provided its own information model for its various classic OPC specifications. Then the OPC Foundation started to look at the opportunity to be able to model information from other vendors in a generic way, as well as from other consortiums.
The best way to explain the information model is with a picture that shows the separation between the OPC UA-based services and the OPC information model and the specifications of information model(s) from other collaborative organizations.
Vendors and end users are able to use and develop interoperable products by simply programming to the OPC UA based services (which is the service-oriented architecture). The OPC classic specifications including data access (DA), alarms and conditions (AC), and historical data access (HDA) are actually being modelled as information inside of the OPC namespace (the OPC Information model in the diagram).
OPC UA has taken the classic OPC specifications and separated the services from the information. This has enabled us to identify the key services of reading, writing, browsing, subscription and security and keep them generic from the information that they are operating on. We are also able to provide complete structures of information behind the data, which I typically talk about as the data and the metadata behind the data.
Now the whole thing comes together. Vendors and end users develop and use products that allow you to read and write the data from an embedded computer that is connected to all the various components (mostly moving components) on the wind turbine. It tracks all the important things necessary to do predictive maintenance operations.
There are so many different vendors that are engaged in industrial automation that are also engaged in developing products for wind turbines. They are all building what is known as OPC servers, which are able to describe the data and the information from the device. They are seamlessly communicating data via the OPC UA service-oriented architecture to generic client applications that can do visualization and historical analysis.
Information Helps to Make Intelligent Decisions
With the information the wind farm operators are gathering they can actually watch the operation and be able to detect and use knowledge-based adaptive learning. That helps to effectively schedule the maintenance operations on the various wind turbines that are spread across the farm. They can actually control the maintenance and service schedule by changing the operational characteristics of the wind turbines. The remote locations service schedule can be synchronized in time.
Numerous wind farms have seen significant decreases in maintenance cost by being able to gather data and information by closely monitoring and tuning the wind turbines. The wind turbines are able to have connectivity to the outside world using open standards. Specifically OPC UA helps to seamlessly push the information including wind turbine diagnostics.
Companies developing the wind turbines know it is in their best interest to make as much diagnostic information as possible and be able to remotely configure all of their components on the wind turbine to achieve the lowest cost of ownership. Companies deploying wind farms want to make sure their annual maintenance costs associated with the wind turbines can be managed effectively.
There will always be cost associated with having to maintain and replace moving parts. Being able to predict and fine-tune the operation is a real advantage as you can analyse this information across a multitude of wind turbines. Thanks to open standards wind farms can pick and choose from different vendors and use the products that are best suited to their needs and still provide seamless interoperability.
This is all about the Internet of Things and connectivity between devices. The next big thing will be to have individual turbines sharing information between themselves. That allows them to adapt to the environment and the characteristics of their own components, effectively increasing operational efficiency across all wind turbines in a single wind farm!
Since 1996, the OPC Foundation has facilitated the development and adoption of the OPC information exchange standards. As both advocate and custodian of these specifications, the Foundation’s mission is to help industry vendors, end-users, and software developers maintain interoperability in their manufacturing and automation assets. The OPC Foundation is dedicated to providing the best specifications, technology, process and certification to achieve multivendor, multiplatform, secure, reliable interoperability in industrial automation and related domains. The organization serves over 440 members worldwide in the Industrial Automation, IT, IoT, Building Automation, Oil & Gas and Smart Energy sectors. For more information about the OPC Foundation, please visit https://opcfoundation.org
A Heat Pump Plant Turns the Carbon Footprint of Textile Fibre Production Negative
Valmet launches intelligent fiber furnish control to secure better refiner operation
Valmet introduces the Valmet Fiber Furnish Control application package for board and papermakers to stabilize refiner operation for maximized production efficiency with ensured furnish quality. Based on real-time measurements of multiple fiber properties and freeness, the control features advanced feedback and feedforward solutions together with model predictive control.