The Modern Air Filtration of Gas Turbines Improve Efficiency
This is based on a field report on utility value enhancement of high efficiency particle filtration. The three-stage EPA filter system brings real benefits in the combined cycle power plant.
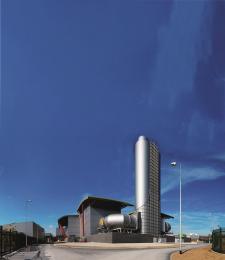
EFFICIENT AIR filtration and its contribution towards the cost-effective operation of gas turbines offer an extensive field for continual design enhancements. The utility value of high-efficiency particle arrestance (EPA) filter installations for gas-turbine air intake systems is becoming increasingly paramount in today’s energy market
Feedback from multi-stage systems installed in the field validates the applicability to these operated filter systems currently in use, against the background of the stipulations posed for particle arrestance, coalescence characteristics and pressure-loss behaviour. Though multi-stage systems can have the disadvantage of an initially higher pressure drop, they do in fact – thanks to almost complete avoidance of fouling and to increased system availability – provide their users with significant, verifiable cost savings.
Responsible deployment of the fossil resources at our disposal demands their maximum efficient and eco-neutral use while simultaneously factoring in their cost-efficient utilization. To reconcile both these aspects is the paramount goal governing the development efforts of turbine manufacturers, system development engineers and system operators alike.
From a system operator’s viewpoint, it is primarily downtimes that are rated as lost profit, and must therefore be avoided. High levels of availability and long running times for the systems concerned are the declared goals. In particular, downtimes required for washing the compressor stages inevitably cause non-productive periods, which need to be minimized or altogether avoided. The aim of the washing routines is to remove any coatings and deposits on the blades. The cause for any such deposits will usually be inadequate intake air filtration.
Basic principles of particle filtration
The demand for efficient air filtration for internal gas turbines entails sophisticated challenges in terms of adequate design for and implementation of the air intake systems being used.
An air filter system is required to significantly reduce the penetration of solid and liquid particles into the turbo-machinery, while coping with temporally fluctuating environmental conditions.
Arrestance of air-borne particles (which may be dust particles or droplets) depends most particularly on the transport mechanisms effective at the location concerned. Electrostatic, diffusion-, inertia-, and gravity-related effects are responsible for particle transport to the filter media, which are usually made of fibres. The adhesion forces operating between particles and fibres in their turn are determined by the interaction of Van der Waals forces, and electrostatic and liquid-related effects, and enable dirt particles to be permanently arrested. When developing filter elements then, both these mechanisms, the transport and the adhesion mechanism, must be given due consideration in the optimization process.
The concentration of air-borne dust particles is of crucial importance for the design of intake air filtration systems. Over the past few years, measurements of dust concentrations have been continuously expanded, so now there is a broad database available. The temporal fluctuation band of the PM10 dust mass found here ranged from approx. 5 – 40 μg/m3 in Germany during 2007, and depends largely on the season of the year, on the surrounding landscape and the degree of industrialization at the place where the measurements are taken. In this context, PM10 denotes the dust fraction whose mean particle size (aerodynamic equivalent diameter) is 10 μm, with 50% of it being arrested. This dust fraction exhibits a particle size distribution that may well contain particles of up to 20 – 30 μm in diameter.
The fact that a very high and nonetheless limited proportion of the dust fraction is being retained also means that there will always be particles penetrating the filter. As a consequence of particles passing through a filter stage, deposits are formed on the compressor blades, which results in output losses at the gas turbine. In regions close to the coast, additional corrosion effects may be encountered, due to air-borne salt particles. The aim of development work on filter systems is accordingly to minimize precisely that proportion of the dust fraction that passes through the filter. Filtration quality is rated in terms of collection efficiencies for individual particle sizes or for the entire dust quantity in question.
Filtration concepts for GT applications
The temporal dust mass carried in determines the choice of a suitable intake air filter system. The size of the particles of relevance for intake air filtration is typically to be found in a bandwidth of around 0.01 μm to about 3 mm, and at locations exposed to high industrial emissions an average mass concentration of up to 200 μg/m3 can occur.
It is only in a few regions (exposed to temporarily extra-high dust concentrations) that regenerative operated systems are actually necessary, which, following the principle of surface filtration, form a compact dust cake on the filter medium involved. Using the pulse-jet cleaning method, the dust cake can subsequently be blown off by compressed air at predefined intervals. Filter systems of this kind are mostly in single-stage design and require precise harmonization with properly functioning cleaning systems. The drawback with these is a relatively high degree of particle penetration during and shortly after the cleaning phase, since it is precisely then that the filtration-supporting effect of the dust cake is absent; it will only be built up again over the course of the cycle now commencing.
In most of the Earth’s regions, low to moderate dust masses are encountered, which can be very successfully stored and lastingly retained in the element’s filter medium using the principle of deep-bed filtration. If the dust-retention capacity is exhausted, the filters concerned are replaced by new, non-loaded elements during the system’s overhaul and standstill times.
The salient features of static filtration systems are these: arrestance of large particles in a pre-filter stage and storage of small particles in the fine-filter stage. Static air filter systems of this kind can be supplied in multi-stage design, which offers scope for optimizing the filter technology involved.
The task of a state-of-the-art design for intake air filters is to affordably reconcile the paramount requirements posed for optimum system operation:
• Maximized system protection = filtration with maximum efficiency and at a consistently high level.
• High system availability = downtimes for replacing the filters are rare and short.
• High system efficiency = low pressure drop in the filter system.
• Reduction in unplanned downtimes of the filter system = failsafe product quality.
Fig. 2: Two-stage filter system comprising pocket and cassette filters. Fig. 3: Three-stage filter system.
An example of the two-stage and three-stage filtration
Fig. 2 illustrates the basic set-up of a two-stage filter system, in which the final cassette filter stage is protected by an upstream pocket filter stage. The core for top-quality filtration of a three-stage filter system as depicted in Fig. 3 is the efficiency particulate air (EPA) filter (Filter Class E11 as defined in EN1822) installed in the third filter stage. The upstream filter stages serve primarily to protect the EPA filter in the final filter stage. The task of pre-filtration is frequently handled by a pocket filter of Filter Class F6 (as defined in EN 779), which in its turn is installed upstream of the intermediate stage comprising F8 or F9 cassette filters. Which filters to choose for these two stages depends crucially on the environmental conditions concerned and the building constraints encountered.
A reduction in the number of pre-filter stages or of the Filter Class will directly affect the dust volume passing through the filter stages concerned, and thus the useful lifetime achievable for the EPA filter in the final filter stage. Moreover, possible effects exerted by the ambient air’s humidity in conjunction with the dust arrested in the filter stages must be given due consideration, particularly when they may increase in size (due to moisture) or sticky dust constituents are involved. These might be responsible for an unforeseeable rise in the pressure drop as a consequence of weather-related factors.
Fig. 2: Two-stage filter system comprising pocket and cassette filters.
Fig. 3: Three-stage filter system.
The principal focus of the parameters:
1. The advantage offered by upgraded EPA filtration is less fouling on the compressor section of the gas turbine.
In this context, the values compiled in Table 1 illustrate the improvement in arrestance achieved by the three-stage EPA filter system as compared to a conventional two-stage fine-filter system. When an EPA filter system is used, the number of particles responsible for compressor fouling in sizes ranging from 0.3 to 0.5 μm can be reduced by a further factor of about 30 and the somewhat larger fraction of 0.5 to 1.0 μm in size by a factor of roughly 200.
The result of the empirical feedback so far obtained from the markets confirms these basic considerations. By using upgraded filtration technology featuring EPA filters, the fouling customarily encountered on the compressor blades is avoided almost entirely. Feedback likewise confirms that online and offline washing can be completely dispensed with, creating the concomitant benefit that there is no longer any reduction in performance between one washing routine and the next (otherwise an accepted fact), which in turn shows up immediately as enhanced performance figures at the machine itself. What is more, non-productive times, reduced output levels and fouling entrainment as side-effects of the washing routines are a thing of the past.
From the theoretical deliberations shown in table 1 this has concurred with actual users reporting lower output loss when a three-stage system is used (Example in Fig. 4) as no deposits on the turbine blades were recorded.
Table 1: Comparison of arrestances achieved by two and three stage filter systems.
Fig. 4: The endoscopic image of the compressor blades surface in a Taurus 65 GT compressor.
Fig. 4 shows the endoscopic image of the compressor blades surface in a Taurus 65 GT. After having been in operation for approx. 9,000 hours without any washing routine at all, no deposits whatsoever adhering to the blades are visible. This is an unequivocal success for the three-stage EPA filter system featuring the combination F6-F9-E11.
A cost comparison must be performed individually for each system in question to ensure the benefits are economically correct to upgrade but in all upgrades that have occurred the results have been positive and improved the overall result, such that is no longer being necessary to add to the running time equivalent operating hours for the start-up procedures required after washing and the increase in the gas turbine’s availability levels are a cost benefit.
The innovative filter concept with upgraded filtration quality have been undergoing applications-engineering trials since 2003 and now currently comprise of more than 200 intake air systems from all front-ranking gas turbine manufacturers. One representative example each for a three-stage filter system and the continuation of a two-stage high-performance system with a final EPA filter stage are adduced here to demonstrate the expectations posed for the relevant performance capabilities.
Note that modular filter systems or similar can be installed upstream without any structural modifications and substantially increase filtration quality while only requiring very little additional outlay and have proved their worth in actual operation.
A Heat Pump Plant Turns the Carbon Footprint of Textile Fibre Production Negative
Valmet launches intelligent fiber furnish control to secure better refiner operation
Valmet introduces the Valmet Fiber Furnish Control application package for board and papermakers to stabilize refiner operation for maximized production efficiency with ensured furnish quality. Based on real-time measurements of multiple fiber properties and freeness, the control features advanced feedback and feedforward solutions together with model predictive control.