The Key Elements of a Successful Lubrication Program
It is said that lubricant is the lifeblood of our equipment. Good lubrication practice includes several key elements.
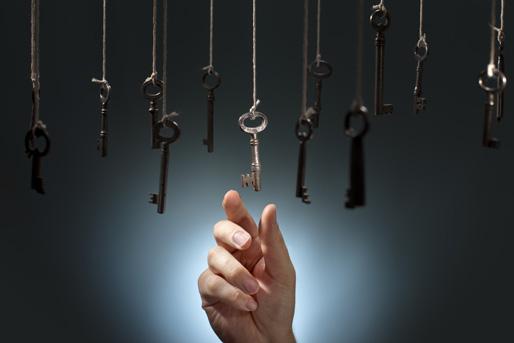
A general rule of thumb within the lubrication community is that over 60 percent of all mechanical failures are directly related to poor or improper lubrication practices (1). In a study by the Massachusetts Institute of Technology (MIT), it was estimated that approximately $240 billion is lost annually (across US industries) due to downtime and repairs to manufacturing equipment damaged by poor lubrication (2).
Every day in plants around the world lubricant is added to machinery for the purpose of preventing failure and preserving its function. Very simply put, the purpose of lubrication is to overcome friction. If friction is the enemy to reliability and ultimately lower operating costs then an effective lubrication program is absolutely essential.
One reoccurring theme Marshall Institute has noticed when conducting maintenance assessments at process and manufacturing plants is the lack of best in class lubrication programs. Even with companies that are considered top performers we notice critical gaps in their lubrication programs.
So what does an effective lubrication program look like? Let’s go through the key elements that we believe to be essential to establishing a successful program.
Plant Wide Maintenance Philosophy
The maintenance philosophy should be endorsed by senior leaders and supported by all the key stakeholders including engineering, production and maintenance. Everyone is responsible for the reliability of the machinery.
The maintenance philosophy should outline the importance of maintenance to the organisation and included in that should be a reference to significance of the lubrication program to plant reliability and cost optimisation. The maintenance philosophy should describe the goals for the lubrication program. The goals can be reviewed annually to ensure continued alignment with plant goals.
Lubricant Selection
The Original Equipment Manufacturer (OEM) manual is always the first place to go to identify lubricant selection requirements. Second, engaging the vendor lubricant representative is absolutely crucial.
The vendor you choose should be able to cross-reference the manufacturer recommendations (OEM) with his available lubricants, oil, and greases and select the appropriate one for your machinery. When an organization lacks lubrication expertise the vendor can be an excellent source of support.
Lubricant Storage and Handling
The first step toward achieving proactive maintenance of your lubricants, and ultimately your equipment, begins with proper in-plant storage and handling. Many facilities are unaware of the danger improper lubricant storage and handling practices create and what inevitable fate it can lead to in terms of equipment reliability and lifecycles.
Proper lubrication is not only about the right amount-at the right time-at the right place, it is also about keeping lubricants clean, cool and properly identified. This is one area that even the best companies fail to focus on. Here are some tips for proper lubrication storage and handling:
- Design the lubrication storage areas: The purpose is to ensure ease of use and limit handling mistakes. The storage areas should be well lit and organized and also include provisions for bulk storage. An area should also be set aside for top-off containers and grease guns.
- Quality control program: This is to ensure the correct oils and lubricants are being delivered and the cleanliness of the delivered lubricants is up to current target particle and moisture cleanliness levels. Checks should also be made to ensure oils haven’t exceeded their recommended shelf life. Finally the quality control program should routinely sample and test oils for contamination.
- Labelling and identification: The labelling system can efficiently ensure the right lubricant is used at the right location and prevent cross contamination. The labelling system should be simple and easy to implement.
Lubricant Dispensers and Grease Gun Storage
Storage for dispensing containers, grease guns and rags is another important step to ensure contaminants are not introduced to the lubricants as a result of poor housekeeping. These tools should have their own dedicated fireproof storage cabinets for easy access and organization.
Grease guns should be stored in a clean, dry and controlled environment. They are precision tools that must be taken care of accordingly. Regular cleaning and inspection of proper function is a must!
Oil dispensers should be of the sealed type and special care should be taken when transferring oil from a bulk container to top-off dispensers to avoid contamination. The use of portable lubricant dispensing carts is the preferred method for transferring large amounts of oil to machines with large gearboxes and reservoirs.
Building the Lubrication PM Program
The key questions to ask are what kind, how much, and how often? Answering these questions will start your lubrication preventive maintenance program. Some basic steps can be followed to achieve PM program success:
- The OEM manual is an important source of information for building your preventive maintenance schedules. The lubrication section of the manual should describe the locations on each machine that should be lubricated, the type of lubricant to use at each location, the quantity of lubricant to be applied and how often to apply the lubricants.
- The lubrication routines should be scheduled preferably in a CMMS. Regardless of the system used, the maintenance department’s daily lubrication activities should be organized. Responsibility should be assigned for each lubrication function.
- Verify that the lubricants being used meet the OEM recommendations for fluid type and viscosity. Never deviate from these recommendations.
- Use only clean containers to transfer lubricants. If possible, pre-filter the lubricant as it is being added to the system.
- Maintain recommended system temperatures. Generally, industrial systems are designed to run most efficiently with bulk fluid temperatures of 110–130 °F (43–55 °C).
- Test fluid periodically (at least every two months) to determine its physical and chemical condition. If a change in appearance is noted, check the fluid immediately. Water content and pH of water-based fluids should be checked frequently. If a major failure occurs, test the fluid before the system is restarted. Residual contamination from a breakdown may prompt another failure.
- Change filters when indicating devices denote plugging of the element, or when fluid analysis reveals a change is needed.
- Keep maintenance records on each system as an aid in determining good preventive maintenance techniques. Records should be audited occasionally to ensure accuracy and thoroughness.
- Colour-code and symbol-code all lubricants and lubrication points. This will minimize mistakes when delivering the PM routines.
Training and Education
Educating the work force is a key first step in launching your lubrication program. The operators and mechanics that are directly responsible for lubrication must be suitably trained, and individuals that are indirectly involved in the lubrication program should also have at least a basic awareness of the program’s goals, primary benefits, and its procedural requirements.
Create Role of Lubrication technician
A best practice is to create the role of Lubrication Technician. The Lubrication Technician should be an intelligent, experienced, conscientious, highly trained member of the maintenance work force.
Once trained, have your Lubrication Technicians validate their knowledge by becoming certified through a credible machinery lubrication certification program.
Performance Measurements
To be assured that our lubrication program is effective requires the measuring of selected parameters and the continuous trending of the data over a period of time. One of the parameters may be as simple as the number of failures due to poor lubrication or a ratio of the number of lubrication-related failures per total failures.
Another good measurement comes from planning and scheduling the lubrication activities. Calculate and record the schedule compliance ratio. This is the number of lubrication work orders completed as scheduled. This tells us not only that the work is getting done, but also it provides some history to monitor frequencies of application. It is suggested that you use all of this information to get started and then back off it if all goes well.
Continuous Improvement
In the quest for reliability the lubrication program should be reviewed and improved on an ongoing basis. This can be done as an annual review led by the maintenance engineer and the lubrication technician. A thorough review of each lubrication schedule can made every three years or some other predefined review cycle. Selected schedules can be staggered so a third of the PM schedules are reviewed annually. Equipment history for the equipment reviewed should be evaluated. Failures occurring as a result of poor lubrication should be examined to determine the root cause.
In addition to annual reviews event based reviews can be made when equipment fails and lubrication is suspect. The intent would be to examine lubrication frequency and methods to identify ways to optimize the lubrication routine.
Finally the lubrication program should be audited regularly to ensure the program is adhered to and goals are being achieved. By using an appropriate audit or self-assessment process, an organisation will have a roadmap to address and evaluate where it presently stands, and where its focus needs to be.
In conclusion, increasing equipment reliability should be the goal of any plant lubrication program. Whether you are developing a new program or reviewing an existing one these nine steps should assist you in evaluating and improving your program. Remember lubrication is the lifeblood of your machinery and your lubrication program should be treated as a critical piece in your overall reliability process.
Paying attention to detail and following your program are keys to success and achieving program goals. Achieving program goals should ultimately lead to higher uptime, greater throughput and lower operating costs resulting in greater profitability.
References:
1. Kenneth Bannister, Lubrication for Industry, 1st Ed. (Industrial Press Inc. 1995)
2. azom.com/new.asp?newsID=11342.
A Heat Pump Plant Turns the Carbon Footprint of Textile Fibre Production Negative
Valmet launches intelligent fiber furnish control to secure better refiner operation
Valmet introduces the Valmet Fiber Furnish Control application package for board and papermakers to stabilize refiner operation for maximized production efficiency with ensured furnish quality. Based on real-time measurements of multiple fiber properties and freeness, the control features advanced feedback and feedforward solutions together with model predictive control.