Remote Monitoring for Corrosion Prevention
Corrosion is the unseen enemy of heating and chilled water systems resulting in premature failure of components, loss of efficiency and huge costs. All too often building owners and maintenance companies rely on ad-hoc water sampling to check for signs of corrosion or, worse still, only react once the system has started to leak.
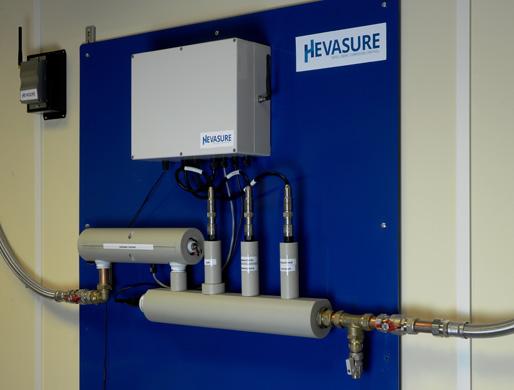
Corrosion of pipework and components in water-based heating and cooling systems nearly always results in costly repairs and unwelcome disruption, especially where district heating schemes, large office blocks, or hospitals are concerned. Not only does corrosion lead to premature failure of components and pipework, but the resultant debris causes significant loss of efficiency due to reduced heat transfer and circulation problems.
In addition, the lack of real data usually means that root causes of any problems remain unknown (risking a repeat of the damage previously caused) and different parties involved all blaming each other. Litigation in such cases is not uncommon with the only winner being the lawyers.
One of the basic problems has been that maintenance/facilities management companies have relied on periodic water sampling to check on the health of the systems. This not only gives a partial picture (water composition is only one aspect that needs to be considered), but is also only a snap-shot view taken at best once per month.
The industry has been slow to seize on the opportunity that continuous monitoring presents; measuring and recording of all key parameters that influence corrosion. Developments in sensors, data loggers and communication technology now make it possible to remotely monitor a range of parameters continuously in real time and provide electronic alerts if critical levels are exceeded. Not only can this prevent potentially very expensive and disruptive problems, but systems can be maintained at optimum efficiency throughout their lifetimes, saving costs and helping meet sustainability targets.
Parameters That Need to Be Monitored
The health of a closed heating and chilled water system is dependent on a combination of engineering integrity and water chemistry. In fact, it could be argued that engineering integrity is the most important consideration and that throwing chemicals at a badly maintained system is both ineffective and wasteful. Table 1 below looks at the system parameters that we would need to monitor to ensure system integrity.
As well as ensuring that the system is operating properly from an engineering perspective, it is necessary to check that the characteristics of the water (chemically and biologically) are not going to lead to corrosion problems. Water treatment products, although not essential, can act as a second line of defence and significantly reduce corrosion rates for all metals in the system providing they are correctly selected and dosed. The parameters that can be monitored are discussed in Table 2 below.
Finally, a monitoring system would not be complete if it did not include some means of measuring corrosion rates. Not only should this include a sensor to measure general corrosion but, if possible, a means of monitoring localised corrosion within crevices and under debris (where corrosion usually starts) should be incorporated. In large systems, measurements of localised corrosion should be made at a number of locations, especially in areas of low flow (see Table 3).
Benefits of Continuous Monitoring
Eliminating corrosion in heating and chilled water systems has enormous benefits for everyone concerned. In a new build, the responsibility for the system passes between a number of parties (installer, commissioning company, maintenance company etc.). By monitoring key parameters, the health of the system can be established throughout the various phases. On hand-over, key data will be available to prove that the system had been properly commissioned and operated up until that point. For existing builds, a monitoring system can be installed to check on the condition of the heating or chilled water system before a maintenance company decides to take over the maintenance contract. This would prevent them from inadvertently taking over the management of a ‘nightmare’ system and incurring large financial losses.
The benefits of continuous corrosion monitoring are clear and protection of some of the most expensive assets in a building (or district heating system) is in everyone’s interest. However, there are undoubted specific benefits to all the stakeholders involved as outlined in Table 4.
Continuous Corrosion Monitoring in Action
The theory and benefits of monitoring have been discussed in detail above. The good news is that continuous corrosion monitoring systems not only now exist, but have been proven in extended field trials. Figure 1 shows such a system developed and tested over several years by Midland Corrosion Services Ltd. This fully integrated system incorporates a web-enabled view of the data in real time with a graphical view of trends over any selected time period. All data is relayed over a mobile phone network to a central database and web server. Interpretation is made by experts in corrosion and alerts sent out if parameters exceed critical levels. Monthly reports are also provided informing management on the overall health of the system and providing recommendations to keep the system operating in tip-top condition.
With the availability of monitoring equipment, maintenance and protection of valuable assets such as heating and chilled water systems are now possible in line with the asset management standard ISO 55000. By ensuring systems are operating at or near peak efficiencies also helps organisation meet environmental and sustainability targets while keeping energy costs to a minimum.
A Heat Pump Plant Turns the Carbon Footprint of Textile Fibre Production Negative
Valmet launches intelligent fiber furnish control to secure better refiner operation
Valmet introduces the Valmet Fiber Furnish Control application package for board and papermakers to stabilize refiner operation for maximized production efficiency with ensured furnish quality. Based on real-time measurements of multiple fiber properties and freeness, the control features advanced feedback and feedforward solutions together with model predictive control.