Fitted with Low-speed Bearings
Bearings are key components of rotating machines. The condition of bearings operated at high speeds can be monitored effectively using a number of techniques such as vibration detection. The condition monitoring of low-speed bearings requires a very different solution.
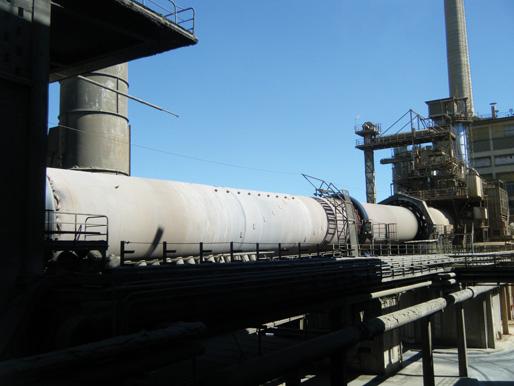
Polysius , a subsidiary of ThyssenKrupp, and a market-leading engineering company in France in the cement plants and facilities sector, recently trialled the use of the latest technology for the early detection of bearing failure in the context of a maintenance contract it provides for anaerobic digestion tubes.
Polysius SAS specialises in the construction of production lines or turnkey plants for the cement and minerals sectors. The company also offers a wide range of services ranging from the supply of spare parts to predictive maintenance auditing.
With a view to assisting one of its customers in establishing the condition of the bearings fitted to its production equipment, Polysius organised an ultrasonic inspection, which involved monitoring the bearings in service and analysing the measurements made. In this specific case, the waste gas treatment tube is supported by spherical roller bearings that rotate at a very low speed.
This type of problem diagnosis task is not straightforward. However, it is crucially important to be able to detect a potential failure at an early stage.
Ultrasound techniques are well suited to this application since they can detect two important phenomena: impacts and high frequencies. Ultrasonic detection is sensitive to low-energy impact phenomena (indicative of a failure) but ignores the low-frequency, high-energy phenomena often associated with operation that can mask a potential problem.
The Inspection Scenario
In this case, the condition monitoring was provided in the context of the maintenance of anaerobic digestion tubes. Polysius wanted to check the condition of all the roller bearings supporting the two waste gas treatment tubes.
The rollers in the bearings rotate very slowly, at just 4 rpm. The company already suspected that one of the bearings was faulty, and had arranged for it to be replaced. The aim of the ultrasonic inspection was to confirm the deterioration of this bearing and to determine whether the other bearings were in good working order.
The two parties involved were keen to avoid the consequences of an unexpected catastrophic failure; especially since a third tube had failed in this way just a few weeks earlier. That failure brought production to a halt in one part of the plant. The bearing had to be replaced as an emergency procedure requiring the hire of a crane and disassembly of the support weighing 20 tonnes.
Data Acquisition and Analysis
For tube 1, static and dynamic measurements were acquired over a very short period of time – just 80 seconds with the bearings rotating at 4 rpm. All that was needed to check the condition of the bearings was a state-of-the-art ultrasonic measuring device and its data management software.
These static measurements revealed that bearings 3 and 4 had both suffered deterioration. A 20 dBµV increase in sound level was recorded compared with the bearings that were in good working order. This diagnosis was confirmed by time-based analysis of the dynamic signal.
The measurements confirmed the suspected failure of bearing 4, but also detected a problem with bearing 3, which the customer had not identified.
For tube 3, in fault-detection mode, static measurements made by the device identified a problem with one of the bearings. The analysis can be taken to the next level where it can identify the cause of the failure, based on dynamic measurements processed by the diagnostic function.
On bearing 8 of tube 3, recurrent impacts were detected, as well as a very high Crest Factor. These are two indicators of early-stage bearing deterioration. Bearing 6 was found to be operating normally.
This predictive maintenance inspection highlighted the need for enhanced monitoring of the bearing showing the early signs of deterioration.
By combining the analysis of static measurements with listening to the signal, the technician detected every bearing anomaly. The display of the dynamic measurements allowed him to pinpoint the fault frequencies for these bearings.
The results of this inspection highlight three points regarding ultrasonic detection: the technique is effective at low rotation speeds; it is well-suited to the diagnosis of faults; and this type of inspection is a valuable preventative maintenance technology which provides reliable indicators.
What Conclusions Can Be Drawn?
Alexandre Vigean works for Polysiusis as an Engineering Project Manager in its Maintenance Department, and is perhaps best placed to assess the inspection.
– Ultrasonic inspection is very well-suited to equipment fitted with low-speed bearings. The slow rotation speed of these bearings does not generate any problems for this technique.
– This type of inspection can also confirm suspected cases of deterioration: the bearing we thought was suffering from excessive wear was quickly identified from the measurements taken. A second bearing, not thought to be defective, showed signs of advanced wear.
– This meant we could plan its replacement before its failure – which causes more serious problems. The inspection also identified signs of degradation in a third bearing. We can act on this early warning to be more attentive to any further changes to this third bearing.
For this specific case, Polysius called on the services of SDT International which designs and manufactures instruments for monitoring production facilities. The ultrasonic measuring instrument used was an SDT270 and the data was analysed using the SDT Ultranalysis software. The waste gas treatment tube is supported by spherical roller bearings that rotate at a very low speed.
A Heat Pump Plant Turns the Carbon Footprint of Textile Fibre Production Negative
Valmet launches intelligent fiber furnish control to secure better refiner operation
Valmet introduces the Valmet Fiber Furnish Control application package for board and papermakers to stabilize refiner operation for maximized production efficiency with ensured furnish quality. Based on real-time measurements of multiple fiber properties and freeness, the control features advanced feedback and feedforward solutions together with model predictive control.