Acoustic Bearing Lubrication Monitoring by Means of Ultrasonic Signals
Bearing lubrication is a crucial issue. It remains the leading cause of bearing failure: 40 percent are replaced prematurely due to over lubrication. Too much lubrication or not enough? When and how? Condition-based lubrication defined by acoustic measurement provides the answer.
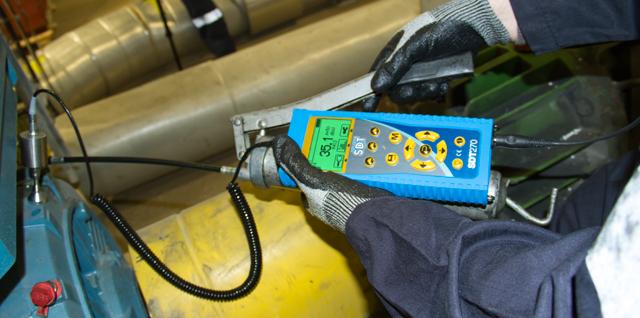
It also enables optimizing relubrication intervals. With SDT, performance is simple and quick, bearing lifespan is increased, and maintenance costs and lubricant consumption are reduced.
Proper lubrication is fundamental for rolling bearings. The main roles of bearing lubrication are:
- Reducing friction
- Avoiding metal-to-metal contact
- Evacuating part of the thermal energy
- Avoiding external contamination.
A leading bearing company has stated that incorrect lubrication is responsible for more than 40% of bearing failures. For sure, inadequate lubrication - under greasing, over greasing or inappropriate lubricant - will be the cause of an reduced life time for your equipment.
Benefit of using ultrasound for Lubrication Control
Defects on rotating machines produce a broad sound spectrum. But only specific problems like friction produce acoustic waves with a rich content shock pulses generating high frequencies.
Moreover, the use of ultrasonic resonant sensors acts as a mechanical amplifier of high frequencies. In addition, the SDT270 ultrasound detector has an excellent signal-to-noise ratio which allows detection of weak variations from background vibrations.
As a result, ultrasound spectrum is very selective technique:
- Highlighting the high frequency phenomena, revealing the lubrication condition.
- Strongly minimizing unwanted low frequencies which could mask lubrication condition.
An other important point is that Ultrasound is an easy method, usable by every Maintenance Operator including the greasing Team. The lubrication diagnosis is simple, immediate and doesn't require complicate post analysis.
On the other hand, solutions -automatic or manual- based on fixed re-lubrication intervals of lubrication are often inappropriate: they do not take account of variations of:
- Working conditions such as temperature, rotational speed, load or bearing type.
- Environmental conditions such as ambient temperature, corrosion or dust.
However these parameters have a huge influence on the bearing requirements in grease. They could be different for one bearing type installed on different machines. They could also vary for one equipment during its use.
For the organizations which do not use ultrasound to optimise the greasing, one generally observes that the equipment are over lubricated. Over lubrication involves an increase of temperature, a seal dilatation, an internal contamination and consequently a premature wear of bearings.
Finally, Ultrasound answer the three fundamental problems encountered by the Operators in charge with the greasing:
- This bearing needs to be greased yes or not?
- If yes, which quantity of lubricant needs to be added?
- What will be the next re-lubrication interval?
More: www.sdt.eu
A Heat Pump Plant Turns the Carbon Footprint of Textile Fibre Production Negative
Valmet launches intelligent fiber furnish control to secure better refiner operation
Valmet introduces the Valmet Fiber Furnish Control application package for board and papermakers to stabilize refiner operation for maximized production efficiency with ensured furnish quality. Based on real-time measurements of multiple fiber properties and freeness, the control features advanced feedback and feedforward solutions together with model predictive control.